Welded Fittings And Their Applications
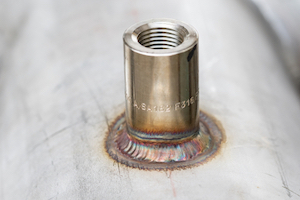
Figure 1: A coupling made of stainless steel 316L welded to a small diameter pressure vessel.
A welding fitting connects pipes and components with a weld to ensure a leak-proof and robust connection. Due to their permanent bond and superior strength, they are widely used across industries such as petrochemical, pharmaceutical, food processing, automotive, and water treatment plants. This article explores the various welded fittings available, their features, and selection criteria.
Table of contents
- What are welded fittings
- Butt weld fittings
- Socket weld fittings
- Selecting between butt weld and socket weld fittings
- FAQs
View our online selection of fittings!
What are welded fittings
Welded fittings are connectors designed to be welded to stainless steel or carbon steel pipes to join components in a piping system.
- Welded connections provide secure, leak-proof connections, and a continuous metal structure.
- Welded fittings do not need additional sealing materials, as welding ensures a leakproof, lasting connection.
Welded fittings can have different configurations depending on the application and design requirements. In some cases, both sides of the welded fitting are weldable, allowing for a direct welded connection to pipes without threads. There are also welded fittings with one end weldable, while the other has another connector, like a threaded connection. They feature a weldable end that can be joined to a pipe through welding, while the threaded end allows for the attachment of another component using a threaded connection. Butt weld and socket weld fittings are the main types of welded fittings.
Butt weld fittings
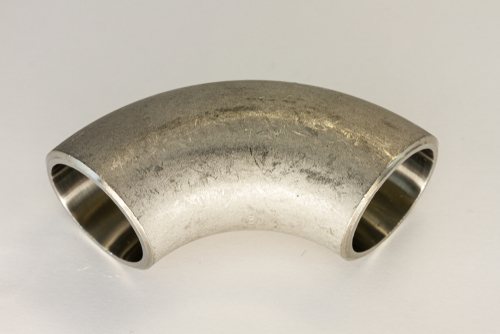
Figure 2: Butt weld fitting
A butt weld is the process of welding two same-sized diameters joined end to end. The thickness and diameter of the end of the fitting and the pipe should be the same. The ends of butt weld fittings are beveled; the bevel shape depends on the wall thickness the pipe it is being attached to. The bevel creates a valley the welding bead can fill to form the butt weld. There are different types of butt weld joints, as seen in Figure 2. Consider the following factors while selecting a proper butt weld profile for an application:
- Refer to applicable industry codes and standards. Codes such as ASME B31.3 for process piping or ASME B31.1 for power piping provide guidelines and requirements for joint preparation, including recommended beveling profiles.
- Consider the material and wall thickness of the fitting and pipe. Thicker-walled pipes or fittings may require a larger beveling angle or double bevel to ensure proper penetration and fusion.
- Evaluate the operating conditions, including pressure, temperature, and corrosiveness. Higher-pressure or critical applications may require a more robust beveling profile, such as a double V bevel, to enhance joint strength and integrity.
The fitting material is typically the same as the pipe it welded to, but it can also be materials like nickel alloy, super duplex, or 6% Molybdenum (for high temperature resistance or other specialized properties). Using the same material ensures compatibility, consistent mechanical properties, and avoids issues such as galvanic corrosion or differential expansion that can arise when different materials are joined together. For instance, using different materials for the pipe and the fitting means different coefficients of thermal expansion; Both materials expand and contract at different rates, leading to stress concentration, distortion, or leaks in the joint if not addressed during design and installation.
Butt weld fittings are used in high-temperature and high-pressure applications to control the flow of products whenever liquids or gasses need to be transported over a long distance. Butt weld fittings are defined under ASME B16.9 standards; lightweight corrosion-resistant fittings adhere to MSS SP43 specifications.
- The ASME B16.9 standard provides guidelines for dimensions, tolerances, materials, testing, and marking of butt weld fittings, ensuring quality and interchangeability.
- MSS SP-43 specifies lightweight corrosion-resistant fittings made of stainless steel, covering dimensions, material requirements, and fabrication guidelines.
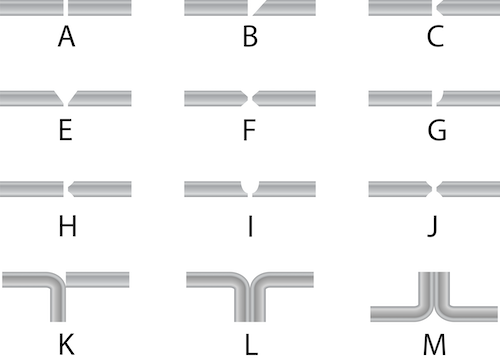
Figure 3: Illustration of butt weld joints: Single square (A), single bevel (B), double bevel (C), single V (D), double V (E), single J (F), double J (G), single U (H), double U (I), flare bevel (J), flare V (K), and flare butt joint (L).
Advantages
- Butt weld fittings are robust and resilient in harsh environments.
- Smooth inner surfaces and gradual directional changes ensure seamless flow and minimize pressure drops.
- Butt weld fittings offer various turn radii (a measure of the curvature of the fitting, which determines the smoothness of the change in the direction of the pipe) options compared to threaded fittings. Welded fittings can be tailored to specific angles and curvatures, allowing for smoother changes in the direction of flow.
- They have a long service life and superior resistance to corrosion and erosion.
Disadvantage
- Higher cost and complexity due to welding requirements
- Time-consuming installation process
- Strict fit-up requirements for proper alignment
- Sensitivity to weld quality, requiring skilled welders
Applications
Butt weld fittings are used for pipe joints that are not changed or assembled, like long-distance and underground piping systems.
- Wastewater treatment plants: Pipelines with butt weld fittings safely handle human waste flow within industrial plants.
- Alcohol production: Butt weld fittings provide a secure and reliable connection in transporting alcohol products from production facilities to distribution centers and, ultimately, consumers.
- Chemical factories: butt weld fittings minimize the risk of leaks, spills, and accidents, protecting the environment in chemical factories that produce potentially hazardous compounds.
Socket weld fittings
A socket weld fitting fits on the outside of the pipe it is being welded to. Socket fittings have a recess into which the pipe end is inserted, and they are then connected by fillet welding the pipe to the fitting, creating a strong and leak-resistant joint. Socket fittings are typically used in small pipe diameters (up to 4 inches or 10.1 cm). They are commonly made of forged carbon steel or stainless steel. These fittings are manufactured in accordance with ASTM A234 or ASME B16.11 standards.
- ASTM A234 specifies the requirements for wrought carbon and alloy steel socket welding fittings, ensuring their material properties, dimensions, and manufacturing processes meet industry standards.
- ASME B16.11 establishes the dimensions, ratings, materials, and testing requirements for forged socket welding and threaded fittings, ensuring their interchangeability, structural integrity, and safe operation within piping systems.
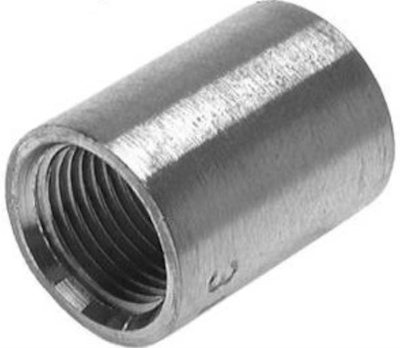
Figure 4: Socket weld fitting
Advantages
- Easy to install and low construction costs as the pipe ends are not beveled.
- The sockets enable easy alignment of pipes for welding.
- Compact compared to flanged fittings
- The weld metal does not flow into the pipe bore due to the socket design
Disadvantage
- Socket weld requires nearly 4.2 mm (1/6 inch) the gap between the pipe and the shoulder of the socket to allow thermal expansion. This gap can increase the stress that cracks the fillet weld (the weld that joins the fitting to the pipe) of the fitting.
- Socket weld may not be suitable for corrosive fluid service due to crevice corrosion. The crevice in socket weld fittings refers to the small gap or recess between the socket and the inserted pipe or tubing. This crevice can create an environment that is susceptible to crevice corrosion, particularly in the presence of corrosive fluids.
Applications
Socket weld fittings are half as strong as butt weld fittings. Hence, they are used for small pipelines with diameters. They are used in pipelines to convey flammable, toxic, or expensive media with zero leakage and are commonly used in plumbing systems and small-scale industrial applications.
Selecting between butt weld and socket weld fittings
While there is some overlap in the applications of socket weld and butt weld fittings, they have different uses based on the specific requirements of the piping systems, such as pipe size, pressure handling capabilities, and installation needs.
- Pipe size and pressure rating: Butt weld fittings for larger sizes and higher pressure, socket weld fittings for smaller sizes, and lower pressure systems.
- Welding requirements: Butt weld fittings require skilled welders and specialized equipment, while socket weld fittings are easier to install with less welding expertise.
- Assess space constraints: Socket weld fittings have a more compact design, making them suitable for limited space applications.
- Joint integrity: Butt weld fittings generally provide higher joint integrity due to full penetration welding.
- Cost: Evaluate the cost of fittings and associated labor costs for installation, as butt weld fittings may require more labor and specialized equipment.
Note: Welded fittings are available in various shapes, including elbows, tees, reducers, and caps.
- Elbows alter the pathway of a pipeline.
- Reducers increase or decrease the pipe bore size.
- Crosses or tees split the fluid flow in multiple directions.
- Caps are used to close off the pipeline.
FAQs
How do I select the right size of welded fittings for my piping system?
Choose welded fittings based on your application's nominal pipe size (NPS) or outside diameter (OD) of your pipes, considering system requirements and standards.
Can welded fittings be disassembled and reused?
Welded fittings are typically not designed for easy disassembly. They are intended to remain in place permanently, and modifications may require cutting and re-welding.
What are some common industries where welded fittings are used?
Welded fittings are widely used in industries such as oil and gas, petrochemical, chemical processing, power generation, and water treatment.