Learn About Gate Valves
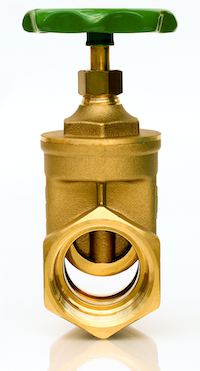
Figure 1: Gate valve
A gate valve is designed to control fluid flow by either fully opening or closing the passage. It's called a gate valve because it uses a flat or wedge-shaped gate to block or allow flow. The gate moves perpendicular to the flow path, similar to how a gate opens and closes to control passage. A gate valve's primary advantage is the straight, unobstructed path it provides, minimizing pressure loss and allowing for pipeline cleaning with pigs, unlike butterfly valves. While slower than quarter-turn valves, gate valves are ideal for applications requiring infrequent operation and should not be used for throttling. They are available in manual versions, which are cost-effective, or automated with electric or pneumatic actuators for more convenience.
Table of contents
View our online selection of gate valves!
Diagram of a gate valve and its parts
As seen in Figure 2, a gate valve has seven main parts: handwheel (A), stem (B), gasket (C), bonnet (D), valve body (E), flange (F), and gate (G). A flanged gate valve or threaded gate valve is the most common connection type to connect the valve to an application. In addition, depending on the specific design and application, the handwheel, stem, bonnet, and gate can have different designs to accommodate different applications. However, the main function of the gate valve parts remains the same. Continue reading to find those sections.
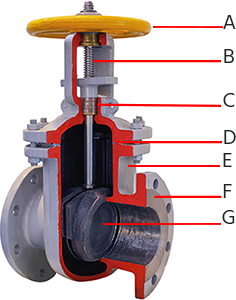
Figure 2: Gate valve parts: handwheel (A), stem (B), gasket (C), bonnet (D), valve body (E), flange (F), and gate (G).
Gate valve symbol
The gate valve symbol has two triangles pointing towards the center of a vertical line, as seen in Figure 3. This figure is commonly used in piping and instrumentation diagrams (P&IDs). Read our valve symbols article for more information.
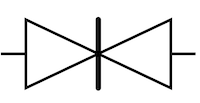
Figure 3: Gate valve symbol
Operation
A gate valve operates similarly to other valves. To open the valve, turn the handwheel (Figure 2 labeled A), which moves the gate (Figure 2 labeled G) up or down on the stem (Figure 2 labeled B) via the threads. A gate valve requires more than one 360° turn of the handwheel to open or close the valve fully. When the gate is lifted up, it opens the inlet to the outlet allowing an unobstructed passageway for the media to flow. When the gate is lowered, it closes and blocks the media flow.
The relationship between the gate's vertical travel and the flow rate is nonlinear for a gate valve, with the greatest changes occurring near complete closure. When used to regulate flow, the relatively high velocity of the flow at partial opening results in gate and seat wear, which, along with possible vibrations of the gate, shortens the valve's service life. Therefore, a gate valve should only be used for on/off control.
A gate valve is best for on/off control with minimal pressure drop when fully open. It is not suitable for throttling. In comparison, ball valves are excellent for on/off control with low-pressure drop and quick operation. They can be used for regulating flow but are not as precise as other valve types, such as needle valves. Read more in our gate valve vs. ball valve article.
A globe valve is best for precise flow control and throttling, but has a higher pressure drop. More about the differences between globe valves vs. gate valves can be found in our article.
Finally, butterfly valves are versatile for on/off and throttling applications, with a compact design and low-pressure drop. For more information, read our article on gate valve vs. butterfly valve. Each type of valve has its own advantages and is suited for different applications based on the system's specific requirements.
Gate valve actuation method
There are three main types of gate valve actuation methods:
- Manual gate valve: A manual gate valve has a manually spun handwheel to open or close the valve, as shown in Figure 2. This requires a user on-site to spin the wheel. A manual gate valve is the most economical, especially since the usage of gate valves, once installed, is typically low.
- Pneumatic gate valve: A pneumatic gate valve uses a pneumatic actuator instead of a handwheel. By utilizing compressed air, the actuator can spin the stem to raise or lower the gate. This allows it to be operated remotely with no user on-site but requires a pneumatic system on site.
- Electric gate valve: An electric gate valve uses an electric motor instead of a handwheel. By utilizing electrical power, the actuator spins the stem to raise or lower the gate. This allows it to be operated remotely with no user on-site but requires electrical power on-site. These are also referred to as motorized gate valves.
Types
The gate comes in various designs and technologies to produce effective sealing for differing applications.
Knife gate valve
A knife gate valve is used for thick fluids and dry bulk solids. The gate is only one piece of metal, which is typically pointed like a knife. These valves are self-cleaning as they pass the seat rings every time they open and close.
Wedge gate valve
A wedge gate valve has a gate in the shape of a wedge that sits on two inclined seats, as seen in Figure 4, Labeled A. In addition to the primary force created by fluid pressure, a high wedging force on the seats created by the stem's tightening assists with the sealing. The wedge-shaped gate does not stick to the seat in case of high fluid differential pressure and has an increased service life due to less "rubbing" on the seats. However, wedge-shaped gate valves have an additional compression load on the seats that may result in thermal binding and restricted valve opening due to expansion.
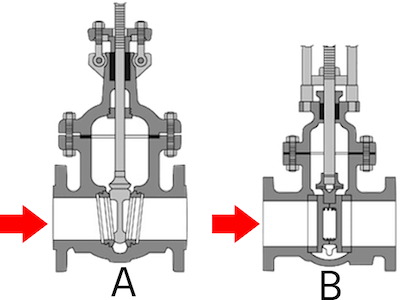
Figure 4: Wedge gate valve (A) vs parallel gate valve (B)
Parallel slide gate valve
A parallel slide gate valve has a flat gate and seats parallel to it. Parallel slide gate valves use line pressure and positioning to make a tight seal. Flat gates consist of two pieces and have a spring in the middle. The spring pushes the pieces towards the seats for enhanced sealing. Due to their inherent design, parallel gate valves have a safety advantage in higher-temperature applications. Furthermore, since there is no wedging action in parallel gates, closing torques are comparatively smaller, resulting in smaller, less expensive actuators or less manual effort. Due to their sliding into position, parallel gates keep dirt away from the seating surfaces.
Slab gate valves
Slab gates, also called through-conduit gate valves, are one-unit gates that include a bore-size hole. The bore is in line with the two-seat rings in the open state. This alignment creates a smooth flow with minimal turbulence. This unique design allows for minimal pressure loss in the system and is perfect for the transportation of crude oil and natural gas liquids (NGLs). The valve seats remain clean. However, the disc cavity can capture foreign material. Therefore, the cavity typically has a built-in plug for maintenance purposes of draining the accumulated foreign material.
Parallel expanding gates
Expanding gate valves have two slab gates matched together that provide sealing through the mechanical expansion of the gate, as seen in Figure 5. When lifted, both of the slab gate's cavities allow the media to flow. The upward force on one slab and the stoppage of the second slab by a step in the valve body, allows for outward mechanical expansion for a proper seal. When closed, the slab gates block the media flow, and the downward force (stem) on one slab and upward force (step in valve body) allow for outward mechanical expansion for a proper seal.
These valves provide an effective seal simultaneously for both upstream and downstream seats. This seal makes them ideal for applications like isolation valves in power plants, block valves in process systems, and high-temperature valves in refineries.
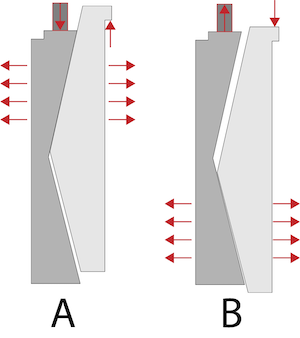
Figure 5: Expanding gate functioning with the closed position (A) and the open position (B)
Bonnets
The bonnet of a gate valve protects its internal parts by creating a leak-proof seal. Therefore, it is removable for repair or maintenance purposes. Depending on the application, gate valves can have screw-in, union, bolted, or pressure seal bonnets.
Screw-in bonnets
Screw-in bonnets are the simplest in construction, as shown in Figure 1. They are common in small valves and provide a durable leak-proof seal.
Union bonnets
Union bonnets are held in place by a union nut. The union nut sits on the lower edge of the bonnet and screws into the valve body threads. This type of design ensures that the leak-proof seal created by the nut does not deteriorate by frequent removal of the bonnet. Therefore, union bonnets are common for applications that require regular inspection or maintenance.
Bolted bonnets
Bolted bonnets provide sealing in larger valves and higher-pressure applications.
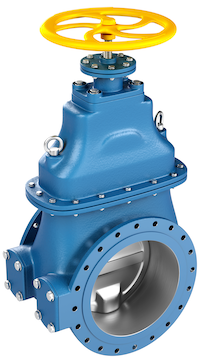
Figure 6: Bolted bonnet gate valve
Pressure seal bonnets
Pressure seal bonnet gate valves are ideal for high-pressure applications (more than 15 MPa). They have a downward-facing cup inserted into the valve body. When internal fluid pressure increases, the cup is forced outward, improving the seal.
Stem design
The gate is raised and lowered by the spinning of a threaded stem (Figure 2 Labeled B). As discussed, a manual wheel or actuator spins the stem. Depending on the design, it is either considered a rising stem gate valve or a non-rising stem gate valve. So, as you spin the stem, it either raises or stays in place with the spin.
Outside Screw and Yoke (OS&Y), also referred to as rising stems, are fixed to the gate. Therefore, the threads are on the actuation side. So, as the gate is raised or lowered, the stem moves with it up and down. Consequently, they have built-in visual indicators of the state of the valve and are easily lubricated. Since they have moving components, they cannot be used with bevel gears or actuators. Therefore, rising gate valves are suitable for manual actuation.
On the other hand, a non-rising stem is fixed to the actuator and threaded into the gate. An indicator is often threaded onto the stem to show the valve's open or closed state. Non-rising gate valves are common in underground installations and applications with limited vertical space.
Applications
Gate valves have numerous industrial and residential applications.
Slurries: Gate valves are often used in applications that contain slurries as their media. This is because a gate valve has an unobstructed passageway for the fluid, so the slurry can easily pass through the valve. In addition, knife gate valves can easily cut right through the slurry to close
Viscous media: Gate valves are commonly used for viscous media like light grease and oils. The unobstructed passageway allows these media to flow easily. The valve can be pigged, a common cleaning method for these applications. In addition, valves for these applications are typically on or off for long periods of time.
Water gate valves: For water applications, water gate valves are commonly used since flow control is typically not done for these applications. The valve can be fully open or fully closed, allowing for proper water control.
FAQs
What is a gate valve?
A gate valve is a control valve that either allows media to flow through unobstructed or stops the fluid flow.
How does a gate valve work?
A gate valve works by rotating the stem (manually or with an actuator) to raise or lower a gate. The gate either allows unobstructed fluid flow or stops it.
What are gate valves used for?
Gate valves are used to allow for unobstructed fluid flow or to stop the fluid flow.