3/2-Way Pneumatic Valve - How They Work
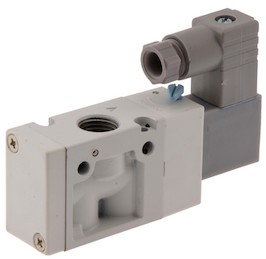
Figure 1: A 3/2-way pneumatic solenoid valve
3/2-way pneumatic control valves are essential for regulating air flow in a variety of applications, including single-acting cylinders, driving pneumatic actuators, and managing tasks such as blow-off, pressure release, and vacuum operations. These valves feature three ports and two positions, functioning by introducing air into the cylinder and then releasing it, which facilitates a new working stroke. The need for a third port for venting makes two-way valves inadequate for these purposes. 3/2-way pneumatic valves can be actuated through several methods:
- Pneumatically: Actuated by compressed air
- Mechanically: Actuated by a mechanical force, such as a lever or cam, which may or may not involve direct human intervention
- Manually: Actuated by a manual operator, like a push button or foot pedal, which is a specific type of mechanical actuation involving direct human interaction
- Electrically (Solenoid): Actuated by an electric solenoid
This article explores the circuit function, design, operation, and common applications of 3/2-way pneumatic valves, with a particular emphasis on 3/2 solenoid valves.
Table of contents
- Circuit function of 3-way air valves
- Design of 3/2-way valves
- 3/2 way pneumatic solenoid valve working
- Versatility and environmental considerations of pneumatic valves
- Typical applications of 3/2-way valves
- FAQs
View our online selection of pneumatic products including directional 3/2-way valves!
Design of 3/2-way valves
3/2-way pneumatic valves come in various designs, with sealing mechanisms that can be either poppet or spool. These valves can be categorized based on their operation and stability.
Based on operation
-
Direct-operated valves: In direct-operated valves, the spool or poppet is moved directly by the actuator. The valve opens or closes by moving the spool or poppet. Various actuator types include:
- Solenoid (coil)
- Push button
- Lever
- Foot pedal
- Indirectly-operated valves: In indirectly operated valves, the spool is not directly actuated by the solenoid. Instead, the system pressure moves the spool. This requires an additional pilot valve, which is a small direct-operated 3/2-way valve. The pilot valve delivers compressed air to a small air cylinder inside the valve, pushing against a piston to actuate the solenoid and switch the valve. This allows for the use of a relatively small solenoid to switch the valve.
Based on stability
- Monostable valves: Monostable valves return to their default position using spring force. They typically have one coil.
- Bistable valves: Bistable valves have a coil at each position and are pulse-operated. They can maintain their position without the need for continuous power, switching between two stable states.
Circuit function of 3-way air valves
The 3/2-way pneumatic valve, or air actuated valve, has three connection ports and two states. The ports are:
- Inlet (P, 1)
- Outlet (A, 2)
- Exhaust (R, 3)
The two states of the valve are open and closed. When the valve is open, air flows from the inlet (P, 1) to the outlet (A, 2). When the valve is closed, air flows from the outlet (A, 2) to the exhaust (R, 3). A valve that is closed in its non-actuated state is called a normally closed (NC), while one that is open in its non-actuated state is called a normally open (NO) valve.
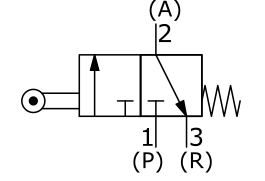
Figure 2: Circuit function of a mono stable, normally closed, 3/2-way valve
Most 3/2-way valves are monostable and return to their default position when not actuated, typically using a spring mechanism. Bistable 3/2-way valves retain their position during power loss and require a separate action to switch states. So, bistable valves cannot be called NC or NO.
In summary, the different functions of the 3/2-way valve are:
- 3/2-way monostable NC
- 3/2-way monostable NO
- 3/2-way bistable
The circuit functions are represented using valve and pneumatic symbols. Figure 3 shows the symbols of an indirect operated 3/2 solenoid valve. Learn about other pneumatic valve symbols and their explanation in our valve symbol article.

Figure 3: Symbols of 3/2-way pneumatic solenoid valves, from left to right: normally open mono stable (left), normally closed mono stable (center), bistable (right).
3/2-way pneumatic solenoid valve working
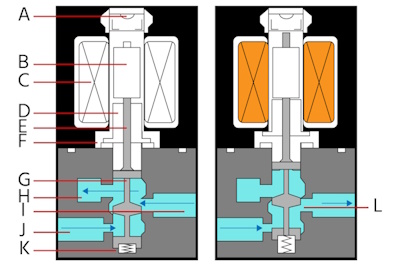
Figure 4: Solenoid-operated 3/2-way pneumatic valve design in the closed (left) an open (right) states: Manual operator (A), fixe core (B), solenoid (C), armature (D), push pin (E), return spring 1 (F), spool (G), atmosphere (H), valve output (I), air supply (J), return spring 2 (K), and orifice (L)
In a solenoid-operated 3/2-way pneumatic valve, the main components and their functions are:
- Manual operator (A): Allows for manual control of the valve.
- Fixed core (B): Provides a stationary magnetic core for the solenoid.
- Solenoid (C): Generates a magnetic field to move the armature.
- Armature (D): Moves in response to the magnetic field generated by the solenoid.
- Push pin (E): Transfers the movement of the armature to the spool.
- Return spring 1 (F): Returns the armature to its default position when the solenoid is de-energized.
- Spool (G): Controls the flow of air through the valve.
- Atmosphere (H): The exhaust port where air is released.
- Valve output (I): The port through which the media exits the valve.
- Air supply (J): The port where compressed air enters the valve.
- Return spring 2 (K): Assists in returning the spool to its default position.
- Orifice (L): The opening through which air flows within the valve.
When the solenoid (C) is energized, it creates a magnetic field that moves the armature (D). The movement of the armature is transferred via the push pin (E) to the spool (G), which shifts to open or close the orifice (L). This action allows compressed air from the air supply (J) to flow through the valve and out through the valve output (I).
When the solenoid is de-energized, return springs (F) and (K) return the armature and spool to their default positions, stopping the flow of air and allowing any remaining air to be exhausted to the atmosphere (H).
Note: All 3/2 solenoid valves need not have all the specific components listed above. The exact design and components can vary depending on the manufacturer and the specific application requirements. For example, some designs may integrate the armature and spool directly, eliminating the need for a separate push pin.
Versatility and environmental considerations of pneumatic valves
With a NAMUR housing, the valve can be directly mounted to an actuator that also meets the NAMUR standard. Manifolds can be used to save space and group valves. Multiple 3/2-way valves can be built into one manifold, and it is possible to mix valve types, such as mounting a 5/2-way valve next to a 3/2-way valve. The combinations depend on the manifold's type and design.
Environmental considerations are crucial in pneumatic systems. Valves and seals must be resistant to corrosion when exposed to aggressive substances. Special valves are available for clean room areas, ATEX environments, and the food industry.
A 5/2-way valve can function as a 3/2-way valve by using only one inlet and the corresponding outlet port. Additionally, the function of a 3/2-way valve can be mimicked using two 2/2-way valves.
Typical applications of 3/2-way valves
3/2-way valves are suitable for several tasks: driving pneumatic actuators, blow-off, pressure release and vacuum applications.
Controlling a single-acting cylinder
A single-acting cylinder has one pneumatic port for filling and emptying the air chamber. The cylinder moves in one direction when the air chamber is filled and returns to its original position by spring force. The 3/2-way valve either fills the air chamber or vents it to the atmosphere. Figure 5 shows a basic pneumatic circuit for a single-acting cylinder.
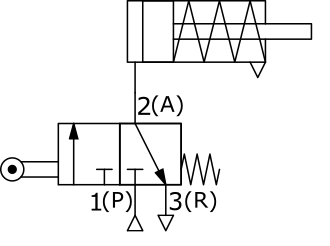
Figure 5: Schematic representation of a single-acting cylinder drive with a 3/2-way valve
Controlling a double-acting cylinder
A double-acting cylinder has two air chambers, each with its own connection port. The cylinder moves by filling one air chamber while venting the other. Typically, a 5/2-way valve is used to operate a double-acting cylinder. However, this can also be achieved using two 3/2-way valves, each connected to one of the cylinder's ports. One valve drives the piston rod to the extended position (a1), while the other valve returns the piston to its initial position (a0) (Figure 6). Advantages of using two 3/2-way valves are:
- Different pressures: Two different pressures can be applied to the cylinder ports without needing a pressure regulator between the valve and the cylinder.
- Simultaneous venting: Both air chambers can be vented simultaneously, allowing free movement of the piston rod, which is not possible with a 5/2-way valve.
To drive the piston from position a0 to a1 using two normally closed valves, one valve must be energized (switched on,'1') while the other de-energized (switched off, '0'). The de-energized valve allows compressed air to exhaust at port (R, 3), causing the piston to move in the required direction. Tables 1 and 2 provide more details on the valve states ('0' and '1' refer to the unactuated and actuated states of the valve respectively) when driving a double-acting cylinder.
At least one of the two valves should be in the "exhaust" position to avoid pressurizing both cylinder ports simultaneously. If both ports are pressurized, the piston's movement will depend on factors such as the previous state of the piston, the amount of pressure, and the cylinder type.
Table 1: Double-acting cylinder drive with one NC and one NO valve
NC valve (Left) | NO valve (right) | Piston position |
0 | 0 | a0 |
1 | 0 | No stable state |
0 | 1 | Free movement between a0 and a1 |
1 | 1 | a1 |
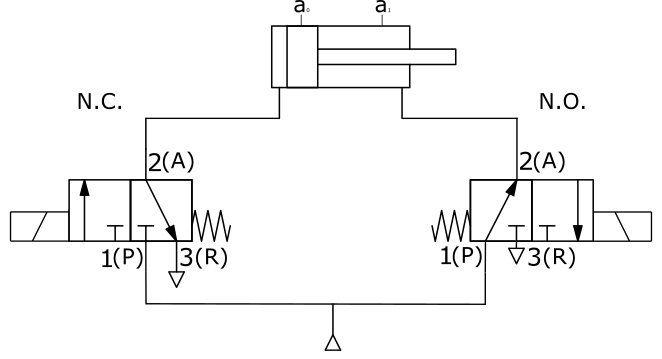
Figure 6: Double-acting cylinder drive with one NC and one NO valve
Table 2: Two NC pneumatic solenoid valves controlling a double-acting cylinder
NC valve (Left) | NC valve (Right) | Piston position |
0 | 0 | Free movement between a0 and a1 |
1 | 0 | a1 |
0 | 1 | a0 |
1 | 1 | No stable state |
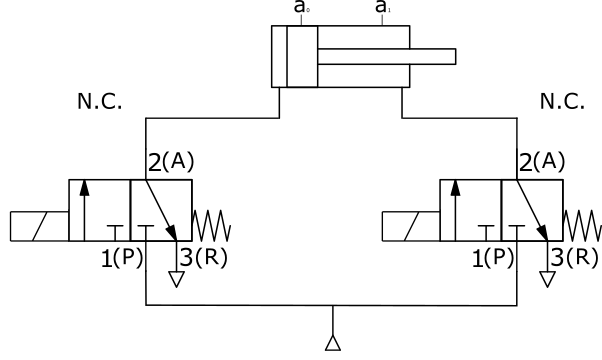
Figure 7: Pneumatic double-acting cylinder with two NC valves
Blow off, pressure release, and vacuum applications
3/2-way valves are ideal for blow-off, pressure release, and vacuum applications. Externally piloted or direct-actuated valves are often necessary because they do not require a minimum pressure differential. Figure 8 shows blow-off, pressure release, and vacuum valve configurations.
In the vacuum circuit, the vacuum pump is connected to port (P, 1), and atmospheric pressure is connected to port (R, 3). The vacuum is broken when port (A, 2) is connected to port (R, 3). The vacuum pad picks up the object when the vacuum pump (connected to port P, 1) is switched on.
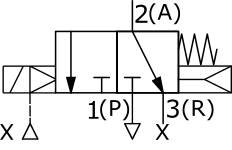
Figure 8: Externally piloted blow-off 3/2-way valve (left), externally piloted pressure relief valve (right)
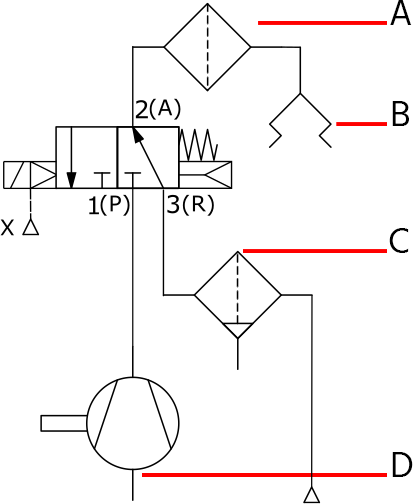
Figure 9: Valve symbol of a 3/2-way valve used for a vacuum application: Vacuum filter (A), vacuum pad (B), filter with separator, manual drain (C), vacuum pump
FAQs
How does a 3 way 2 position valve work?
A 3-way 2-position valve has three ports and two positions. It directs flow between two of the three ports in each position, allowing for control of fluid direction, typically used for diverting or mixing flows.
What is the difference between a 2-way and 3-way valve?
A 2-way valve is any type of valve with two ports: an inlet and an outlet port. A 3-way valve has three ports within the valve body which are used as inlet, outlet, and exhaust.