Comparing Manual vs Electric vs Pneumatic Valves
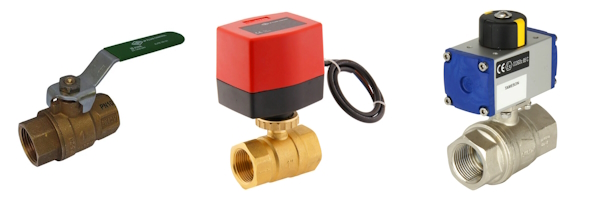
Figure 1: 2-way ball valves. Manual (left), electric (center), and pneumatic (right)
Choosing between manual, electric, or pneumatic actuated valves depends on system requirements, cost, and environmental conditions. Manual valves are simple and cost-effective but require physical operation. Electric valves offer high precision and automation but are more expensive. Pneumatic valves provide fast response times and are suitable for hazardous environments but can be less efficient and noisier. This article explores each valve type's mechanisms, advantages, and disadvantages and their applications in various scenarios.
Table of contents
- Comparison table
- Valve use in non-critical systems
- Integrating different types of valves into a single application
- Valve symbols
- FAQs
Comparison table
Table 1 provides an overview of how manual, electric, and pneumatic valves work and their advantages and disadvantages. It's important to note that in the scope of this article, pneumatic valve refers specifically to valves with a pneumatic actuator that uses compressed air to generate mechanical motion. In this article, pneumatic valves do not necessarily refer to valves used in pneumatic systems to control compressed air flow.
Table 1: Comparison table for manual, electric, and pneumatic valves
Type of valve | Mechanism | Advantages | Disadvantages |
---|---|---|---|
Manual valves | Operated by physically turning a handle or lever to open or close the valve. |
Simplicity: Easy to use and operate. Durability: Robust construction suitable for harsh environments. Cost: Generally less expensive than automated valves. Maintenance: Requires minimal maintenance and no external power source. |
Flexibility: Limited control over flow rates; requires physical presence for operation. Precision: Less precise compared to automated valves. High-pressure systems: Not ideal for high-pressure applications Frequent adjustments: Not ideal for frequent adjustments. |
Electric valves | Electric actuator valves use an electric motor to control the valve's position, converting electrical energy into mechanical motion to regulate fluid or gas flow. |
Precision: High accuracy in controlling flow rates. Automation: Can be integrated into automated systems for remote control. Maintenance: Lower maintenance requirements compared to manual valves due to their precision, reducing errors and wear and tear. |
Cost: Higher initial cost and installation expenses. Complexity: More complex design requiring specialized maintenance. Power dependency: Requires a reliable power source, which may not be available in all environments. |
Pneumatic valves | Pneumatic flow control valves use compressed air to generate mechanical motion. Available in two main types: double-acting and spring-return. |
Cost: Generally lower purchase price compared to electric valves. Durability: High durability and can operate in extreme temperatures. NAMUR: Some pneumatic actuators have NAMUR interface for easy mounting of accessories, such as limit switch boxes. Speed: Fast response times, suitable for high-speed applications. Safety: Explosion-proof and suitable for hazardous environments. |
Efficiency: Less efficient due to pressure losses and air compressibility. Maintenance: Requires a source of compressed air and associated equipment. Noise: Can be noisy, which may be an issue in certain applications. |
Valve use in non-critical systems
In many industrial and commercial applications, the choice between manual, electric, and pneumatic control valves may not be critical due to overlapping capabilities. Here are some application parameters where multiple or all types of valves can be effectively used:
- Moderate pressure systems: In systems where the pressure is moderate and does not require the high precision of electric valves or the rapid response of pneumatic valves, manual valves can be just as effective. For instance, water distribution systems in residential or commercial buildings can utilize any of the three types of valves.
- Temperature range: For applications operating within a standard temperature range (not extremely high or low), all three types of valves can be suitable. This includes HVAC systems, where the temperature is typically controlled within a moderate range.
- Non-critical flow control: In applications where precise flow control is not essential, such as in simple on/off operations, any type of valve can be used. Examples include irrigation systems or basic fluid transfer operations.
- Intermittent operation: For systems that do not require continuous operation or frequent adjustments, manual, electric, and pneumatic valves can all be appropriate. Examples include emergency shut-off systems or backup systems that are only activated occasionally.
- Environmental conditions: In environments that are not particularly harsh or hazardous, all three types of valves can be used interchangeably. For example, in a controlled indoor environment, the durability and specific advantages of each valve type may not be as critical.
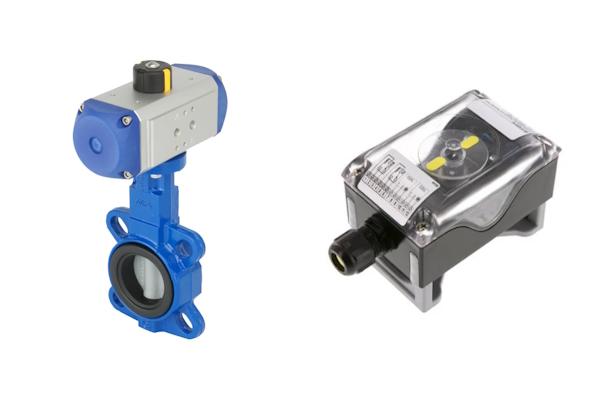
Figure 2: Pneumatic actuators, such on this butterfly valve (left), can have NAMUR interface for easy mounting of limit switch boxes (right).
Integrating different types of valves into a single application
Integrating manual, electric, and pneumatic valves into a single application can offer a balanced approach, leveraging the strengths of each type while mitigating their weaknesses. Here’s how they can work together:
- Primary and secondary control: Electric valves can be used for primary control due to their precision and ability to integrate with automated systems. Manual valves can serve as secondary or backup controls, providing a fail-safe mechanism in case of power failure or system malfunction.
- Zoning and isolation: Pneumatic valves, with their fast response times, can be used in critical zones requiring quick actuation, such as safety shut-off areas. Manual valves can be used for isolating sections of the system for maintenance or emergency purposes.
- Redundancy and reliability: Combining different types of valves can enhance system reliability. For example, in a high-stakes application like a chemical processing plant, electric valves can provide precise control, while manual valves offer a reliable backup. Pneumatic valves can be used in hazardous areas where electric sparks could pose a risk.
- Cost management: By strategically placing manual valves in less critical areas and reserving electric or pneumatic valves for high-precision or high-speed sections, overall system costs can be managed more effectively. This hybrid approach ensures that resources are allocated efficiently without compromising performance.
- Maintenance and accessibility: Electric and pneumatic valves can be integrated into hard-to-reach areas where manual operation would be impractical. Manual valves can be placed in accessible locations for easy maintenance and manual override if necessary.
- System feedback and monitoring: Electric valves can provide real-time data and feedback, which can be used to monitor and adjust the performance of manual and pneumatic valves. This integration allows for a more comprehensive and responsive control system.
Valve symbols
Manual valve symbols (Figure 3 top) can include a T shape to represent the lever or handwheel. Electric valve symbols (Figure 3 middle) can include a square with an M inside to represent the motor and pneumatic valve symbols (Figure 3 bottom) can include a semi-circle.
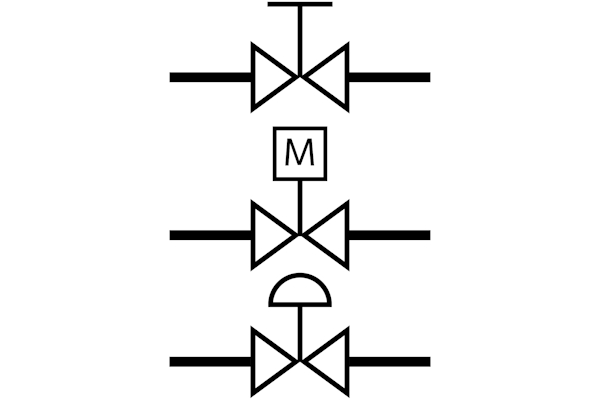
Figure 3: A manual valve symbol (top), electric valve symbol (middle), and pneumatic valve symbol (bottom).
FAQs
What are motor-operated valves?
Motor-operated valves are automated valves controlled by electric motors, providing precise control and remote operation in various applications.
What is a pneumatic valve?
A pneumatic valve uses compressed air to control the flow of fluids, offering quick response times and suitability for hazardous environments.
What is an electric valve actuator?
An electric valve actuator converts electrical energy into mechanical motion to operate a valve, providing high precision and automation.
How do electric valve actuators compare to pneumatic valve actuators?
Electric valve actuators offer high precision and automation, while pneumatic actuators provide faster response times and are suitable for hazardous environments.