Air Pressure Regulator Troubleshooting & Replacement
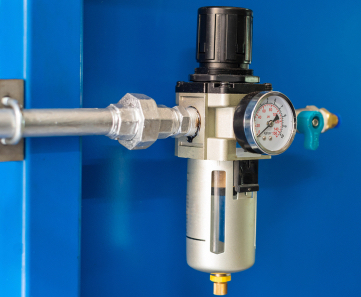
Figure 1: An air pressure regulator
An air pressure regulator controls downstream and upstream pressure. This device is an important component in pneumatic systems, so air pressure regulator replacement is essential when it stops working. This article focuses on troubleshooting issues around air pressure regulators and how to replace them when necessary.
Table of contents
View our online selection of filters, regulators & lubricators!
Troubleshooting a pneumatic pressure regulator
Read our pressure regulator overview article to learn more about air pressure regulator design and operation.
There are three common issues that pneumatic pressure regulators face:
- Leakage: Air can leak from the air pressure regulator through the weep hole or cracked or broken seals (e.g., o-rings).
- Downstream pressure fluctuations: The downstream pressure drops below or rises above the pressure set by the regulator.
- Upstream pressure fluctuations: The upstream pressure drops below or rises above the pressure set by the back-pressure regulator.
Air pressure regulator leakage
Air compressor regulator leakage leads to the air compressor over cycling, which uses extra energy and causes more wear on the compressor. Therefore, identifying and fixing leakage as soon as possible is essential.
Normal air leakage occurs through the regulator’s weep hole when a user reduces the set pressure for downstream pressure. When this happens, the pressure downstream of the regulator is higher than its set point, so that pressure needs to escape through the weep hole until the downstream pressure reaches the regulator’s set pressure.
If air leakage through the regulator’s weep hole is frequent whenever there is air in the tank, the likely cause is a cracked diaphragm. The diaphragm controls how much air flows downstream. Improper lubricating oils or too many pressure change cycles can eventually break the diaphragm. While air leaks through the diaphragm and out the weep hole or regulator handle, the downstream pressure can not be adequately controlled. Small, inexpensive regulators are easier to replace than repair. However, replacing the diaphragm can be the best solution for large regulators.
Pressure fluctuations
Pressure fluctuations, either downstream or upstream of the regulator, may indicate that the pressure regulator is not working correctly. The first troubleshooting step is ensuring the system uses the correct regulator. A pressure-reducing regulator controls downstream pressure, and a back-pressure regulator controls upstream pressure. If the incorrect regulator is in the system, replacement with the correct regulator is necessary. If the proper regulator is in place, there are other reasons why the pressure may rise beyond the set limit: creep, supply pressure effect, and an improperly sized regulator.
Creep
If the correct regulator is in place, there are other reasons why the pressure is rising beyond the set limit. One of the most common causes is creep. Creep occurs when the regulator fails to close completely, and high-pressure air can leak through the regulator. To test for creep in a regulator:
- Close the regulator to stop air flow downstream.
- Slowly turn on the regulator’s air source until the inlet gauge reaches the desired delivery pressure.
- Open the regulator until the inlet gauge reads approximately half the desired delivery pressure.
- Close the regulator and note the outlet pressure.
- After fifteen minutes, if an increase in outlet pressure is seen, creep is happening.
Creep can lead to downstream components receiving air at higher pressures than their design allows. The following actions can help reduce the possibility of creep occurring:
- Installation: Take extra care during installation to ensure that no foreign material gets into the regulator.
- Filter: An upstream filter can remove particulates large enough to prevent the regulator from fully closing.
Supply Pressure Effect
The supply pressure effect (SPE) is the inverse proportional relationship between the inlet and outlet pressure. For example, as an air tank empties, the pressure it delivers to the regulator drops. This drop leads to a rise in outlet pressure from the regulator. This phenomenon occurs in spring-supported regulators when the inlet pressure is high enough to keep the diaphragm open but not high enough to work fully against the spring supporting the diaphragm. As the diaphragm closes slightly, the outlet pressure increases. Most, if not all, manufacturers will give SPE values in their regulator’s manuals. When selecting a regulator, ensure that any outlet pressure rises will not damage downstream components.
The best method for reducing the effect of SPE is to use two regulators in sequence. This setup has two benefits:
- Pressure drop: If a large pressure drop is necessary, each regulator can reduce a portion of the pressure. The combined portions will equal the required large pressure drop.
- Outlet pressure: Using two regulators in series allows for finer control over the outlet pressure. The second regulator can adjust for any changes in outlet pressure from the first regulator. A two-stage pressure regulator combines this process in a single device.
Regulator size
A regulator that is too small for a system’s flow rate will cause droop. Droop is an increase in flow rate through the regulator that leads to a decrease in outlet pressure. The best solution to droop is to correctly size a regulator before choosing one. Most manufacturers will provide flow curves that help users determine the right regulator size for the system’s flow properties.
Replacing a pneumatic pressure regulator
The following cases require replacing a pneumatic pressure regulator:
- A small regulator’s diaphragm cracks. Replacing the entire regulator is not expensive and much simpler than replacing the diaphragm.
- The system requires a pressure-reducing regulator but has a back-pressure regulator or vice versa.
- The regulator is too small for the system’s flow properties, which leads to unacceptable amounts of droop.
- Flushing water through the pressure regulator does not remove the fine particles that prevent the regulator from fully closing, leading to creep.
The following safety and installation guidelines will help ensure that air regulator replacement is successful.
Safety guidelines
When selecting an air pressure regulator, ensure it meets the proper international standards. When a device meets international standards, it has the best chance of not prematurely breaking or failing dangerously. The following standards cover pneumatic pressure regulators:
- ISO 4414: ISO 4414 covers hazards related to pneumatic fluid systems and methods for mitigating hazards under normal operating conditions.
- IEC 60204-1: IEC 60204-1 applies to electronic equipment. This covers electronic pneumatic regulators.
Before replacing an air regulator
Before replacing a regulator with another that is properly certified:
- Ensure the regulator is compatible with the system’s flow requirements.
- If the regulator to be replaced connects to an electric source, ensure electricity has been cut.
- Have proper training for managing regulator handling and replacement.
- Do not use the regulator outside of conditions that the manufacturer set.
- Ensure a clean environment so foreign material cannot enter the regulator and cause creep.
- Consider installing a filter upstream of the regulator if one is not already present.
While replacing an air regulator
During the replacement process:
- Cut off the upstream air supply.
- Ensure any sealant on pipes or fittings does not enter the regulator.
- If using tape as a sealant, leave the last 1 or two threads of the fitting bare.
- Ensure the regulator is facing in the right direction.
- To prevent undue torque on a regulator with a threaded connection, hold it by hand and use the other hand to screw the pipe or fitting into it. Tighten to the manufacturer’s recommended torque to prevent leaking and excessive vibration.
After installing an air regulator
- Use the gauge on the air pressure regulator to check the upstream pressure before adjusting for the downstream pressure.
- Adjust the outlet pressure to no higher than 90% of the inlet pressure. If the outlet pressure is higher than that, fluctuations in the pressure can cause damage to downstream components.
- Apply power and pressure to the regulator to check for leaking.
- If there are any electrical connections, perform safety checks according to national standards.
FAQs
What happens when a pressure regulator fails?
If a pressure regulator fails, downstream pressure can rise to levels high enough to damage downstream components.
Can a pressure regulator get clogged?
A pressure regulator can be clogged by even small particles that prevent the regulator from fully closing. This leads to creep.