Analog Vs Digital Transducers

Figure 1: Pressure transducers in oil and gas industry
Analog transducers and digital transducers convert physical quantities into proportional electrical signals. Analog transducers are widely used in traditional measurement systems due to their simplicity and low cost. Digital transducers, on the other hand, are increasingly used in modern intelligent systems because of their high accuracy, high interference immunity, and ease of integration. This article explores the fundamental differences between these two types of transducers, examining their operational principles, advantages, and applications in fields.
View our online selection of pressure transducers!
What is an analog transducer?
An analog transducer converts a physical quantity, such as temperature, pressure, or light intensity, into a continuous electrical signal. This signal typically varies in voltage or current and directly reflects the changes in the measured physical quantity. For instance, if the pressure ranges from 0 to 60 bar, the transducer might output 4 mA at 0 bar and 20 mA at 60 bar. At 30 bar, the output would be 12 mA. This means it promptly responds to any changes in the input pressure as it rises up or goes down.
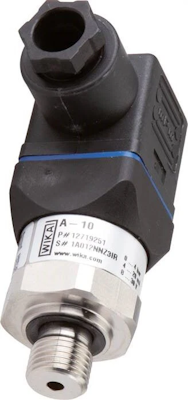
Figure 2: Wika analog pressure transducer
What is a digital transducer?
A digital transducer converts a physical quantity into discrete digital signals, represented by binary values (1s and 0s). Digital transducers use algorithms and digital processing to interpret their inputs and produce the desired output. They often incorporate additional components, such as analog-to-digital converters (ADCs), to transform analog signals into a digital format.
Digital transducers have high accuracy and resistance to interference, making them suitable for complex and high-precision applications. An example of a digital transducer is a digital temperature sensor, which converts temperature readings into digital data that can be easily processed by microcontrollers or computers. For instance, a digital temperature sensor outputs a binary value of 0001 1001 0001 0001 at 25 𐩑C and 0011 0010 0000 0000 at 50 𐩑C.
Note: Sensors detect and measure physical quantities, such as temperature or pressure, and convert them into raw signals. Transducers, on the other hand, convert these raw signals into standardized electrical signals, often incorporating sensors along with additional signal conditioning components. For example, a pressure sensor detects pressure and outputs a raw signal and a pressure transducer converts the raw signal from the pressure sensor into a 4-20 mA current signal. Learn more about their differences in our sensor vs transducer article.
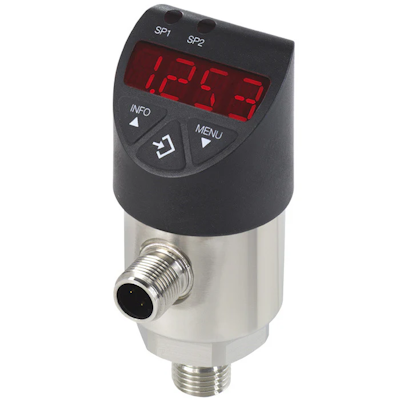
Figure 3: Wika pressure switch and pressure transducer in one device with a digital display
Key considerations for choosing analog or digital transducers
Choosing the right transducer type depends on the specific application's needs.
-
Resolution and accuracy:
- Analog: Offers continuous output, potentially providing higher resolution depending on the analog-to-digital converter (ADC) used for reading. However, accuracy can degrade due to noise and signal drift over time.
- Digital: Provides discrete output values with fixed accuracy determined by the bit depth. Higher bit depth translates to greater accuracy but may require additional processing power.
-
Signal processing and interface:
- Analog: Often requires additional signal conditioning circuitry (amplifiers, filters) before interfacing with data acquisition systems. This adds complexity and potential noise.
- Digital: May integrate internal signal conditioning, simplifying interface with digital input devices. This reduces noise and simplifies system design.
-
Data transmission:
- Analog: Signals are susceptible to noise and interference over long distances.
- Digital: Less prone to noise and interference, making them ideal for long-distance data transmission.
-
Cost and complexity:
- Analog: Generally lower initial cost, but additional signal conditioning circuitry can increase overall system complexity.
- Digital: May have a higher initial cost due to internal processing circuitry, but the simpler interface reduces overall system complexity.
Table 1: Differences between analog and digital transducers
Feature | Analog transducer | Digital transducer |
Data output | Outputs continuous voltage or current signals representing the analog value | Outputs discrete digital signals, usually in binary form |
Accuracy | Depends on the quality of the sensor and circuit design, may be affected by noise | High accuracy, less affected by noise and interference |
Resolution | Limited by the sensor and ADC resolution, usually lower | High resolution, typically 12-bit, 16-bit, or higher |
Signal processing | Requires an ADC to convert analog signals to digital for processing | Usually integrates ADC internally, no external conversion needed |
Transmission distance | Limited transmission distance, susceptible to electromagnetic interference | Can be transmitted over long distances via serial interfaces, strong anti-interference ability |
Interface complexity | Simple interface, typically reads signals through voltage or current changes | Complex interface, requires protocols and standards to read and transmit data |
Power consumption | Usually low, depending on specific circuit design | May be higher due to more integrated circuits and processing functions |
Cost | Generally cheaper, suitable for simple and low-cost applications | Generally more expensive, but has advantages in accuracy and reliability |
Calibration | May require frequent calibration to maintain accuracy | Lower calibration frequency, usually calibrated at the factory |
Response time | Short response time, suitable for measuring rapidly changing signals | Response time may be longer due to data processing and conversion |
Read our pressure transducer selection criteria for a more comprehensive understanding of the various parameters while selecting a pressure transducer.
Applications
Analog sensor/transducer applications
- Analog pressure transducers: Convert gas or liquid pressure into an analog electrical signal for monitoring and control in machine building, measurement and control technology, hydraulics and pneumatics, pumps and compressors, and shipbuilding
- Thermocouples: Used for temperature measurement in industrial boilers, furnaces, and chemical equipment
- Photodiodes: Employed for light intensity detection in camera light sensors, auto-dimming lamps, and ambient light sensors
- Analog microphones: Used for audio input in recording equipment, telephones, and hearing aids
Digital sensor/transducer applications
- Digital temperature transducer: Used for high-precision temperature monitoring in industrial applications, mainly HVAC systems, as well as in manufacturing processes, food and beverage production, chemical processing, and energy management systems
- Digital pressure transducers: Utilized in hydraulic systems, HVAC systems, and process control
- Accelerometers: Employed for motion detection and location tracking in smartphones, game controllers, and automotive safety systems
- Light transducers: Used for light intensity detection and automatic adjustment in smartphone screen brightness and automatic lighting systems
- Gas transducers: Applied in air quality monitoring devices, industrial gas detectors, and agricultural environmental monitoring
- Liquid transducers: Used for detecting and measuring various properties of liquids in liquid level monitoring systems, flow meters, and liquid composition analyzers
FAQ
What is the difference between analog and digital speed sensors?
Analog speed sensors produce a continuous signal proportional to speed, while digital speed sensors generate discrete pulses or signals, often in binary form, representing speed data.