How To Solder A Ball Valve
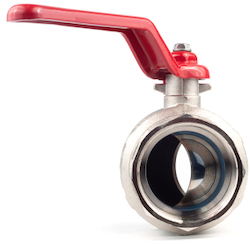
Figure 1: Ball valve
Soldering is an essential process in the plumbing, electronic industry, and jewelry industry, and it is a vital skill for electronics hobbyists working on home projects. Soldering a ball valve to a copper pipe ensures a tight leak-free connection between the valve and the pipe. When the valve and pipe ends are heated to a suitable temperature, the plumbing solder melts into the joint between the valve and the pipe by capillary action and makes a watertight seal upon cooling.
Table of contents
- Soldering a ball valve
- Difference between plumbing solder and electrical solder
- How to solder a ball valve
- Precautions
- Soldered ball valve advantages
- Soldered ball valve disadvantage
- FAQs
View our online selection of ball valves!
Soldering a ball valve
Soldering uses metal with a low melting point (solder) to join two or more connections. Heat is delivered to the solder, which melts and flows into the joint between the workpieces. The solder cools in a few seconds, creating the soldered joint. The chosen solder should have a lower melting point than that of the components being connected in the process; otherwise, parts of the components may melt. A soldered connection between a ball valve and a pipe ensures a strong and reliable bond that lasts for years.
Difference between plumbing solder and electrical solder
Electrical solder and plumbing solder have different compositions.
- Electric solder needs to melt at a low temperature to avoid causing any potential damage to the electronic components. But copper pipes can withstand much higher temperatures; hence, soldering for pipes is done at a higher temperature.
- Mechanical strength is not a crucial factor for electric soldering, whereas, for soldering copper pipes, the mechanical strength of the pipes and connected installation is vital.
- The solder flux used in electric and plumbing solder is different in composition. The plumbing flux is more aggressive (corrosive) in nature and it can lead to corrosion of electronic components if used on electronic components.
The soldering process used in plumbing systems is explained in the next section.
How to solder a ball valve
Materials required
- Solder flux
- Emory cloth
- MAPP gas/propane torch
- Solder
Ball valve soldering process
- Inspect both ports of the ball valve, sockets, and seating surfaces to ensure they are clean and free of foreign particles. Ensure the ends of the copper pipe being soldered is square cut and free of foreign materials and metal shavings. Use steel wool or emery cloth to thoroughly clean the pipe ends and solder sockets.
- Apply flux paste over the entire area that is to be soldered, like the outside of the pipe ends and the inside portion of the valve solder sockets. The flux paste cleans and removes oxides and impurities from metal surfaces, thereby preparing the metal surfaces for soldering.
- Soldering a ball valve can be done in either an open or closed position. However, we recommend soldering the ball valve in the closed position. It’s safe and there’s less chance of damaging any internal parts. Always refer to the valve manufacturer’s sheet for directions on soldering the valve open or closed.
- Fit and align the valve and pipe properly using pipe supports. These supports must keep the pipe in alignment with the valve and bear the weight of the fittings, valves, pipes, and contents.
- A torch nozzle is a device that produces concentrated heat by the combustion of fuels within. It can be used to heat and melt the solder material to make the joint between the valve and the pipe. Select a torch nozzle based on the following parameters:
-
The fuel gas: The fuel gas being used for combustion like propane, MAPP gas, propylene, and acetylene.
- MAPP gas and propane are the most commonly used fuel gasses for torch nozzles. The propane torch is cheap and works well for most plumbing works. The most significant advantage of MAPP gas (methyl acetylene-propadiene) is that the gas burns twice as much as how propane burns. Therefore, the joint gets hot twice as fast to melt the solder. This saves approximately 15- 30 seconds per joint. MAPP gas also enables soldering large pipes (pipes having more than 1-inch diameter are difficult with propane). But MAPP gas is costly compared to propane.
-
Type of the valve and pipe used: For pipes with larger diameters, select a torch nozzle that burns more, thereby melting the solder twice as fast.
- Use a soft solder that is no-lead certified with a melting temperature of less than 500 degrees fahrenheit, ideal for the solder to melt.
- While using ball valves made from silicon brass alloys, always use special solder, flux, and higher soldering temperature to make the connection.
- Always consult the valve manufacturer for their installation directions.
- The soldering process produces heat that can heat up the valve. Take extreme care to prevent valve overheating which can cause damage to valve seals and seats. Wrap the valve’s center portion using a wet cloth to help prevent the center portion from getting overheated. Do not use cloth materials like cotton that can easily catch fire upon being heated. Emory cloth is an excellent option for handling soldering works.
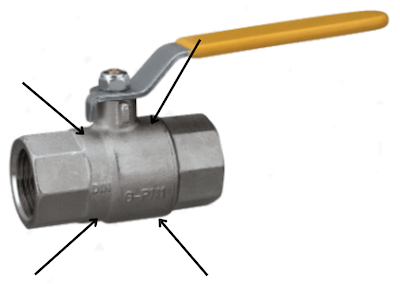
Figure 2: Arrows pointing to the center portion of the valve to be covered by a wet cloth
- Concentrate the heat on the copper tube, and always direct the flame in an angled position away from the valve body joint. Next, direct the heat onto the socket area of the valve, avoiding the body joint. Keep moving the flame around the circumference of the connection to avoid heat concentration in one area, which could damage the valve seats and seals.
- Touch the solder to the joint. As soon as the solder begins to melt, continue applying the solder around the socket (whole 360°) for vertical installations. The solder will be drawn into the joint, and the filler metal in the molten state will cover the whole area on which the solder flux was put on.
- For ball valves with threaded fittings, the presence of even a tiny amount of solder on the thread can make the fitting extremely difficult to tighten. Therefore, protect the threads with a heavy coat of pipe dope (thread sealant) before soldering the fitting. At times, the heat from the torch can dry out the thread sealant completely, in which case reapply the product onto the threaded fitting.
- Allow the valve to cool naturally when the first joint is complete. Wait until the valve is cool to touch before beginning the second joint.
- Verify the tightness of the packing nut when the installation is complete, and the valve has cooled down completely.
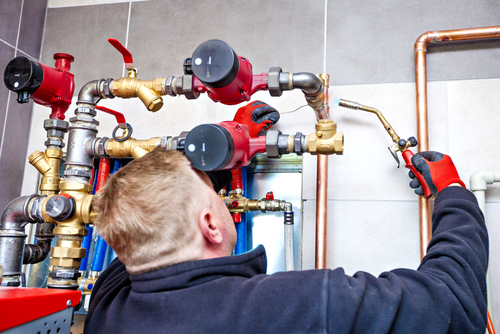
Figure 3: A torch nozzle is being used for soldering a ball valve. Heat is applied to a concentrated area of solder flux where the melted solder gets attached.
Precautions
- Allow the soldered joints to cool: Hot solder is delicate in nature. Even gentle movements from the surroundings can ruin a soldered joint when it is still hot. Allow the joint to cool properly before putting any stress on it.
-
Don’t burn the flux: While heating the joint, if the flux begins to smoke or get blackened, it means one of two things:
- The torch is held too close to the joint. In this case, pull the torch back and try to heat the joint slowly.
- The joint gets overheated due to holding the torch on it for too long.
- Protect nearby joints from heat: If the soldering is done 2-3 inches or less from another joint, wrap the joint with a wet rag so that it doesn’t get hot enough to soften the solder.
- Resolder a leaking joint: Turn off the water supply first and allow the pipe to drain by opening a faucet that is lower than the leaky joint. Then coat the joint with solder, heat it, and add more solder. If this method doesn’t work, take the joint apart and start over.
- Personal protection: Obtain the required open flame permits, wear personal protection equipment during the soldering process, and always keep a fire extinguisher on hand.
Soldered ball valve advantages
- Low cost
- The long-lasting connection between the valve and pipe
Soldered ball valve disadvantage
- Overheating, bad solder, or old flux can result in bad connections
FAQs
Should the ball valve be kept open or closed while soldering?
Soldering a ball valve can be done in an open or closed position. But, soldering ball valves in the closed position are better because they’re safe, and there is less chance of damaging any internal parts like seats and seals.
Can you damage a ball valve while soldering?
Ball valves are not easily damaged by heat. But make sure to concentrate the heat only at the valve body’s fitting ends.
How to sweat a copper pipe?
‘Sweating’ and ‘soldering’ are two terms used interchangeably to describe the process of using solder and heat to join copper pipe and related fittings to one another. The basic soldering process used on copper pipes is explained in the sections above.