Burkert 8605 Solenoid Valve Controller - How They Work
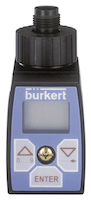
Figure 1: Burkert 8605 proportional valve controller
The Burkert 8605 controller is a dedicated proportional solenoid controller. The 8605 features a simple parameter set specific to proportional solenoid valves for easy configuration and programming. Software features such as coil heating compensation, parameter selectable inputs, ramp function, and coil current adaption allows for proper valve operation over its full stroke range. Additionally, the 8605 is offered in various design options to satisfy a variety of mounting and configuration requirements.
Table of contents
- Open loop control
- How the Burkert 8605 controller works
- Mounting options
- Software features
- Accessories
- Approvals and standards
- Controller selection criteria
- 8605 selection chart
- Integration with non-Burkert products
View our online selection of proportional solenoid valves!
Open loop control
In contrast with the 8611 controller, the 8605 controller does not use process feedback to influence the output PWM signal to the solenoid valve. The output of an open loop system is based strictly off its inputs. Open loop control systems are commonly used with systems that are stable and process disturbances are rare. The advantages of an open loop control system include:
- Reduced component complexity
- Reduced system configuration
- Reduced cost
How the Burkert 8605 controller works
Read our proportional solenoid valve controllers article to further understand how pulse width modulation (PWM) works in the Burkert 8605 controller. The 8605 controller is designed to control proportional solenoid valves in an open loop system, which can be seen in Figure 2. Therefore, the controller input signal will directly control the output PWM signal. The PWM signal frequency will be proportional to the input signal. The operation of the 8605 is dependent on two critical parameter settings:
- Input: Selection of the input signal which will be used as the set-point signal. The input signal is software selectable and can be selected between the 0 – 5V, 0-10V, 0-20mA, and 4-24mA.
- Output: Selection of the valve output settings. The output settings are used to define the valve type and the frequency limits (HI and LO) of the PWM control. Once the valve type is set, the frequency limits will be automatically set according to the valve type. During operation, the PWM control will operate within the range defined by the limits. Set values for PWM frequencies are also available by Burkert. The output signal will influence the controlled variable.
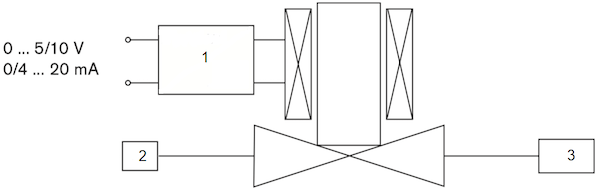
Figure 2: 8605 operation: set-point signal (1), manipulated variable (2), and controlled variable (3)
Proper configuration of the input and output settings is required for proper valve operation. The valve can be damaged if the wrong valve type is selected.
Mounting options
The 8605 controller is available in two different versions with different housing, degrees of protection, and electrical connections. Each housing style can be ordered in options with varying current ranges from 40 to 2000 mA. The software programming and control function is the same regardless of housing style. Consult the selection chart to determine if the device is compatible with your valve.
Cable plug
The cable plug form can be ordered with a PG or M12 connector for electrical wiring. The PG connection version allows for wiring to a 4-pin terminal strip inside the device. The M12 connection version requires a standard M12 connector with the correct wiring pin out. Pin out for both connection versions can be referenced in the 8605 operating manual. When considering the cable plug housing style, the current range of the valve should be verified. The cable plug version is offered in 200 to 1000 mA and 500 to 2000 mA options. If the max current range falls below 200 mA, the DIN rail version controller should be considered instead. Each version of the cable plug form 8605 can be ordered with (Figure 3 left) or without (Figure 3 right) an operating unit which is used to program the controller. The controller will operate properly without the operating unit. The operating unit is commonly used to transfer parameters between several devices via the upload and download functionality of the operating unit. The cable plug version is IP65 rated and is well suited for adverse operating conditions.
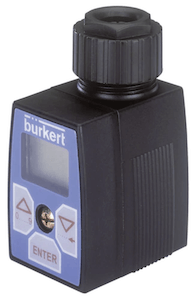
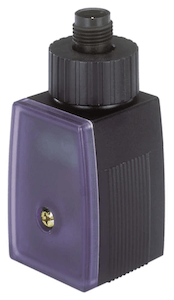
Figure 3: Burkert 8605 cable plug with an operator (left) and without an operator (right)
DIN-rail mounting
The DIN rail version of the type 8605 can be conveniently mounted on a DIN rail (Figure 4). Wiring is easily accessible and secured using the screw terminals at the housing. The DIN rail version meets DIN EN 50022 standards and offers variants in the 40 to 220 mA, 200 to 1000 mA, and 500 to 2000 mA range. The operating unit cannot be removed from the DIN rail version controller. This controller version offers an IP40 rating for protection.
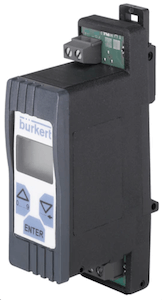
Figure 4: 8605 DIN-mount
Software features
The software features integrated in the 8605 are designed to optimize performance, extend valve lifetime, and decrease installation time. This is achieved by adjusting PWM output response time, current control, and parameter upload and download features.
Ramp function
This function is used for applications in which sudden changes of an input signal would adversely affect the process. Since the 8605 uses an open loop control system, changes to the input signal will directly modify the output signal. The ramp function can be used to adjust the PWM output to its desired set point over an adjustable time period to decrease the impact of a sudden change to the input signal.
Coil current adaption
Increased coil temperature will alter the inductive properties of the coil and thus alter the magnetic response of the PWM signals. The 8605 is equipped with an internal current control to compensate for coil heating by tracking the duty cycle and modifying the PWM output. The benefit of this feature is consistent performance over the operating temperate range of the valve.
Adjustable zero-point cut off
The zero-point cut off is used to guarantee leak-tight closing of the solenoid valve and can be adjusted in the 8605. This parameter can be set between 0.1 to 5.0 % of the set input signal to activate the zero-point shutdown. When configuring this parameter, it is important to note that once the input signal is below the set threshold the controller, the PWM output will be completely shut off.
Parameter upload and download
The upload and download feature is used to transfer parameters from the operating unit to the controller device. This function is useful to reduce installation time of many controllers with a common valve. This function is only available for the cable plug version.
Accessories
Communication interfaces
For further integration into a control system a RS485/RS232 is available on request. These communication modules allow for writing and reading of the 8605 parameters. Telegram transmission to the 8605 is based on the HART protocol. Telegram structure and available commands for developers can be found in the 8605 serial communication manual. The RS485 and RS232 modules are available for the Cable plug and DIN rail mount housing styles.
Operating unit
Separate operating units can be ordered for the cable plug housing version.
Electrical connection accessories
M12 connector accessories such as cables and right-angle plugs are available.
Approvals and standards
This controller is available with the below listed approvals and standards:
- CE: Conforms to the EMC Directive EN61326
- IP65
Controller selection criteria
Determining the correct controller for your application depends heavily on the process you are trying to control. The following considerations should be taken when selecting a controller:
-
Control Type
- Determine if your application requires an open loop or closed loop controller. How stable is the system your valve is controlling? How will error affect the process? An open loop controller such as the Burkert 8605 is suitable for stable systems which operate consistently around a set-point. A closed loop controller such as the Burkert 8611 is suitable for applications that require automatic changes. These applications tend to be unstable and require error regulation.
-
Control Inputs
- The set-point signal should be compatible with the controller.
- Closed loop systems using the Burkert 8611 require sensor input to measure system error. A sensor that meets the signal requirements of the controller should be used.
-
Control Outputs
- Ensure that controller has the proper outputs to control the connector valve. The Burkert 8605 can only control proportional valves. The Burkert 8611 is a universal controller and can control proportional valves, process valves, and more. The control signal must also be compatible with the valve input.
-
Mounting Style
- There are different mounting options for each controller type. Ensure that the controller can be properly mounted and the inputs and outputs are sufficient for the sensors and valves used in your system.
8605 selection chart
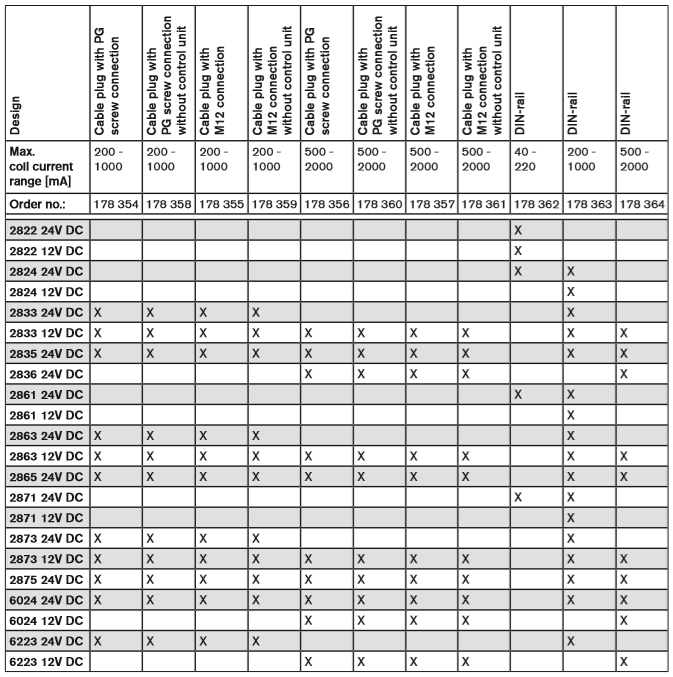
Integration with non-Burkert products
The 8605 controllers is designed and tested with Burkert products. They can be used with other brand’s components, but parameters must be manually entered in and tuned. To ensure proper performance third-party devices and components should be authorized by Burkert before using.