How To Clean a Pneumatic Solenoid Valve
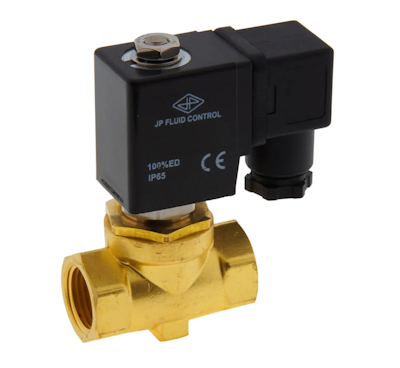
Figure 1: 3/2-way pneumatic solenoid valve
Cleaning and maintaining pneumatic solenoid valves are essential for ensuring the efficient and reliable operation of pneumatic systems. These directional control valves play a crucial role in controlling the flow of compressed air, and their performance can be significantly impacted by the accumulation of dust, dirt, and other contaminants. This article provides a detailed, step-by-step guide on how to clean a pneumatic solenoid valve.
Table of contents
- When to clean a pneumatic solenoid valve
- How to clean a pneumatic solenoid valve
- Test the pneumatic valve
View our online selection of pneumatic solenoid valves!
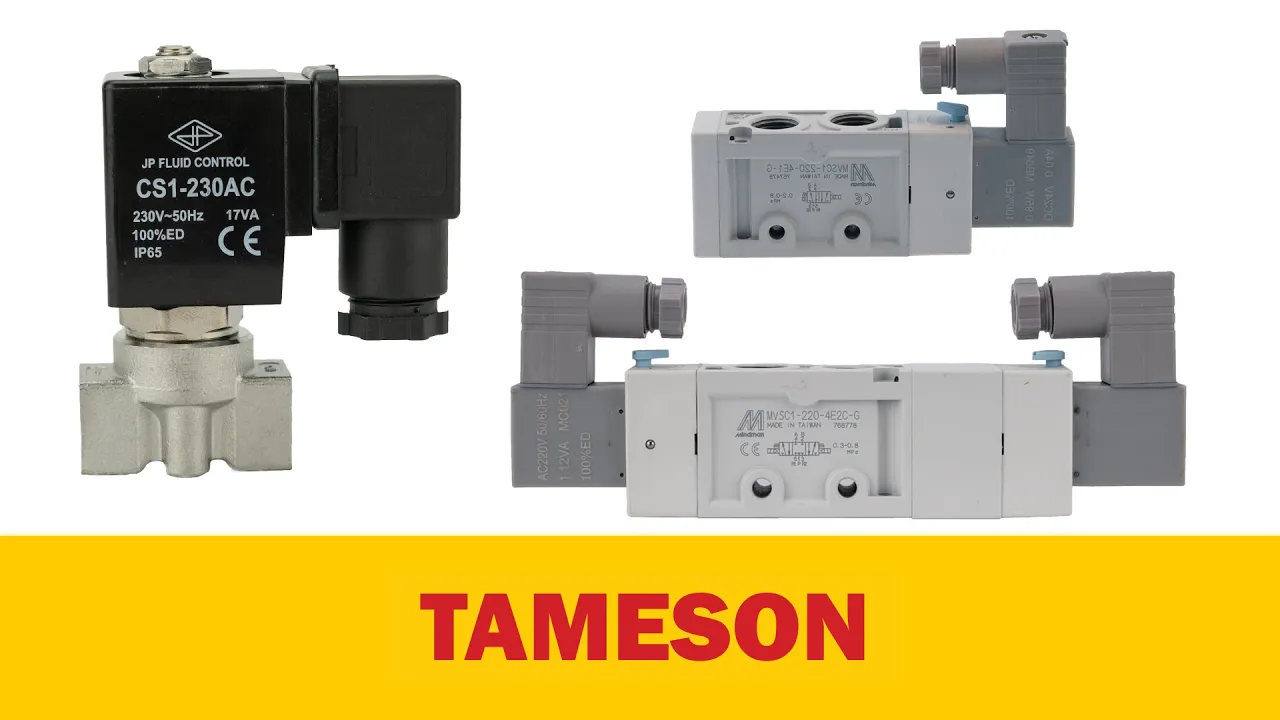
When to clean a pneumatic solenoid valve
Determining when to clean a pneumatic solenoid valve requires regular inspection and attention to its performance. Here are some indicators that it might be time for cleaning a pneumatic solenoid valve:
- Decreased performance: If the valve is not operating as efficiently as before, such as slower response times or reduced flow, it could be due to internal contamination.
- Unusual noise: Increased noise or a change in the valve's operating sound can indicate a problem, often related to debris or wear.
- Leakage: Any noticeable leakage around the valve body or spool is a clear sign of contamination or seal wear, necessitating cleaning or repair.
- Frequent cycling: Valves subjected to frequent on/off cycles are more prone to contamination and wear, requiring more frequent cleaning.
- Operating environment: Valves in harsh environments with exposure to dust, dirt, or corrosive substances will require more frequent cleaning.
- Maintenance schedule: Regular cleaning as part of a preventive maintenance program can extend valve life and prevent unexpected failures.
Read our pneumatic solenoid valve article for more information on the design and working of 5/2- and 4/2-way pneumatic solenoid valves.
How to clean a pneumatic solenoid valve
- Isolate and depressurize the system: Isolate the valve from the pneumatic system by closing the upstream and downstream air supply. Depressurize the system by venting any residual air through the exhaust ports or using a manual override if available.
- Disconnect the electrical connections: Disconnect the electrical connectors from the solenoid coil. Note the wiring configuration for reassembly. Remove the solenoid coil by unscrewing the retaining nut or clip. Carefully slide the coil off the valve stem.
- Remove the pneumatic valve from the manifold (optional): If the valve is mounted on a manifold, use an adjustable wrench to loosen the mounting bolts. Gently lift the valve off the manifold, ensuring no damage to the o-rings or sealing surfaces.
- Disassemble and clean the valve body:
- Place the valve on a clean, flat surface. Identify and remove the screws or bolts securing the valve body.
- Carefully separate the valve body halves, taking note of the orientation and position of internal components such as the spool, springs, and seals.
- Clean the external surface of the valve body. Use warm water and a mild detergent or neutral cleaner to gently wipe the external surface of the valve body. This will help remove dust and dirt buildup. Avoid spraying water or cleaner directly into the valve's internal components.
-
Extract the internal components:
- Remove the spool and associated springs from the valve body. The piston and spools may be held in place by springs or other mechanisms. Inspect the spool for wear, scoring, or contamination. In a 3/2 directional control valve, the spool has three positions for the supply, exhaust, and actuator ports. During disassembly, carefully note the spool orientation and spring positions, as they determine switching behavior. A 5/2 valve, with five ports and two positions, has a more complex spool with multiple seals and passages. Properly positioning each seal during reassembly is crucial to prevent internal leaks and ensure proper operation.
- Remove other internal components like diaphragms, seals, and any o-rings. If the valve includes a pilot-operated mechanism, disassemble the pilot section by removing the retaining screws and separating the pilot valve components
-
Clean the internal components:Inspect all internal components for signs of damage, wear, or blockages. Identify any parts that need replacement.
- Use a compressed air source or an air tank to blow air through the various passages inside the control valve. This will help dislodge accumulated dust and debris. Begin by blowing air from one end of the valve and gradually move to other openings, ensuring all passages are thoroughly cleaned.
- If there are stubborn deposits or residue inside the valve, use a solvent recommended by the manufacturer. Apply the solvent to a clean brush or cloth and gently scrub the affected areas to dissolve and remove the deposits. Be careful not to use too much solvent, as it can damage seals or other components. After cleaning, ensure all parts are thoroughly dried using a lint-free cloth. Moisture can lead to corrosion or affect air flow.
6. Reassemble the valve: Once all the internal components are cleaned and dried, follow the manufacturer's instructions to reassemble the valve. Make sure all parts are properly aligned and tightened according to the recommended torque specifications.
Note: Always disassemble the pneumatic solenoid valve by following the manufacturer's guidelines. Ensure to have the appropriate tools and user manual or technical documentation provided by the manufacturer. Also, pay close attention to any specific instructions regarding the order of disassembly and the handling of delicate parts to avoid damage.
Test the pneumatic valve
- Reconnect power and air supply: Reconnect the valve to the power source and turn on the air supply. Check for any air leaks around the valve body and connections.
- Test valve operation: Activate the solenoid valve and observe its operation. Ensure the valve shifts smoothly and responds correctly to control signals.
- Conduct leak test: After reassembly, conduct a thorough leak test to ensure that the pneumatic control valve is functioning properly. Reconnect the valve to the pneumatic system, restore the air supply, and check for any air leaks. Adjust the valve settings if necessary.