Copper, Brass, & Bronze Comparison
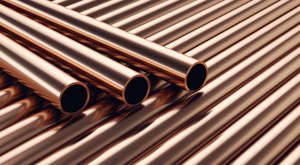
Figure 1: Copper pipes
Understanding the important differences between copper, brass, and bronze will ensure that the correct material is chosen for various applications. These metals are known as "red metals" because of their color. The article will examine what each metal is made of, how they differ, and how they are used. Understanding these factors can help users select materials better for specific applications.
What is copper?
Copper is an elemental metal with high thermal and electrical conductivity, making it ideal for electrical wiring. Its physical properties include strength, excellent ductility, and superior corrosion resistance. It has good formability; it can be readily soldered, brazed, and welded. Copper is also recognized for its antimicrobial properties, proven to kill more than 99.9% of bacteria within two hours of contact.
See one example of how copper is used in our copper and compression fittings article.
What is brass?
Brass is an alloy composed primarily of copper and zinc. The properties of brass vary depending on the amount of zinc added; increased quantities enhance the material's strength and ductility. Brass exhibits a color range from red to yellow, depending on the zinc content. When the brass contains 32% to 39% zinc, it has higher heat resistance, and its cold resistance is limited. If the zinc content surpasses 39%, the brass will have higher strength but lower ductility at room temperature. Brass is known for its workability, durability, and aesthetic appeal.
What is bronze?
Bronze is primarily composed of copper and tin. Adding tin or other elements like arsenic, phosphorus, aluminum, manganese, and silicon hardens the alloy, making it tougher than copper. The color of bronze is typically dull-gold, and faint rings on its surface distinguish it from brass. Bronze is appreciated for its low metal-on-metal friction, making it ideal for bushings and bearings in industrial applications. Its corrosion resistance also makes it suitable for salt water applications. Finally, bronze can coat other metals to make them look like bronze or to generate good oil and grease distribution in the case of shafts and pistons.
Differences between copper, brass, and bronze
- Composition: Copper is a pure mineral, whereas brass and bronze are alloys containing copper and other minerals.
- Color: Copper is reddish-brown, brass is bright, gold-like, and bronze is dull gold-like (Figure 2).
- Primary uses: Copper has high thermal and electrical conductivity. Brass has decorative appeal, making it popular for hardware and ornamental objects. Bronze is ideal for components like bushings, bearings, and gears.
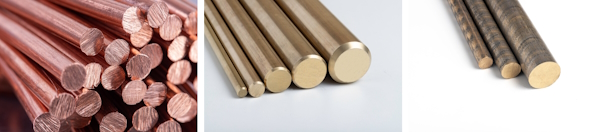
Figure 2: Rods made out of copper (left), brass (middle), and bronze (right).
Common grades
The following are common copper, brass, and bronze grades used in industrial applications.
Common copper grades
- C11000: Electrolytic tough pitch (ETP) copper. This is the most common copper grade; it is 99.9% pure copper. It's used in electrical applications due to its high electrical and thermal conductivity.
- C10100 & C10200: Oxygen-free copper. Oxygen-free copper grades have high conductivity and formability. They are used when cosmetic appearance is important or in processes that require brazing and welding.
- C12200 & C12000: Phosphorus-deoxidized copper. These grades are often for plumbing, heating, air conditioning, and refrigeration applications.
- C14500: Tellurium copper. This grade is known for its machinability and is commonly used to produce screw machine parts.
- C17200 & C17500: Beryllium copper. These grades have high strength, hardness, and thermal conductivity. Beryllium copper is used to manufacture tools, in aerospace applications, and oil and gas equipment.
Common brass grades
- C36000: Free cutting brass. This is the most common brass used in machining. It's ideal for producing parts in high volume.
- C23000: Red brass. This is also known as 85% brass. It has excellent corrosion resistance and is used for pipe and pipe fittings.
- C26000: Yellow brass. This grade is used to manufacture components that require moderate strength and good corrosion resistance. It's used for architectural applications, general-purpose screw machine parts, hinges, locks, and gears.
- C46400: Naval brass. This grade has good strength and rigidity, especially in salt water. It's used in marine hardware, propeller shafts, and marine fasteners.
- C28000: Muntz metal. This grade is about 60% copper, 40% zinc, and a trace of iron. It is commonly used in architectural structures for its corrosion resistance.
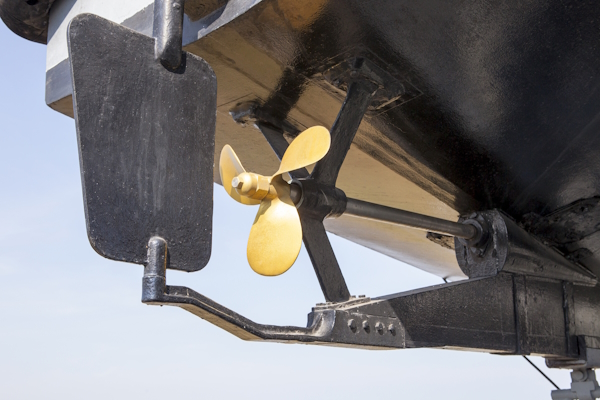
Figure 3: Naval brass is suitable for boat propellers
Common bronze grades
- C51000 & C52100: Phosphor bronze. These bronze grades have high strength, toughness, and good electrical conductivity. They are commonly used in electrical products, springs, and various types of hardware.
- C61400, C95400, & C95500: Aluminum bronze. These grades have high strength, excellent wear and corrosion resistance, and are commonly used in heavy-duty mechanical and marine components.
- C65500: Silicon bronze. This grade has easy pouring ability, corrosion resistance, and strength. It's used in power plants, saltwater piping systems, and the manufacturing of fasteners and pump components.
- C67500 & C86300: Manganese bronze. These grades have high strength and hardness, good wear resistance, and excellent machinability. They're commonly used in industrial machinery applications.
- C90700 & C90500: Tin bronze. These grades have good load-carrying capacities, wear resistance, and machinability. They are often used for gears, bushings, bearings, and other heavy-duty mechanical parts.
Selecting between copper, brass, and bronze
Consider the following criteria when choosing between copper, brass, and bronze products for industrial or DIY applications.
- Electrical conductivity: If the application involves electricity or heat transfer, copper is often the best choice due to its high electrical and thermal conductivity.
- Corrosion resistance: If the product will be exposed to the elements or used in a marine environment, bronze offers good corrosion resistance. Bronze, particularly aluminum bronze, is often used in marine applications due to its superior resistance to corrosion in salt water.
- Machinability: Free cutting brass (C36000) has excellent machinability so it is suitable for high-volume production applications.
- Strength & durability: Bronze is generally harder and more durable than copper and brass.
- Aesthetics: Brass has a bright, gold-like appearance, so it is used for decorative hardware. Copper has a distinctive reddish color. Bronze has a dull, gold-like appearance.
- Cost: Copper is generally more expensive than bronze which is generally more expensive than brass.
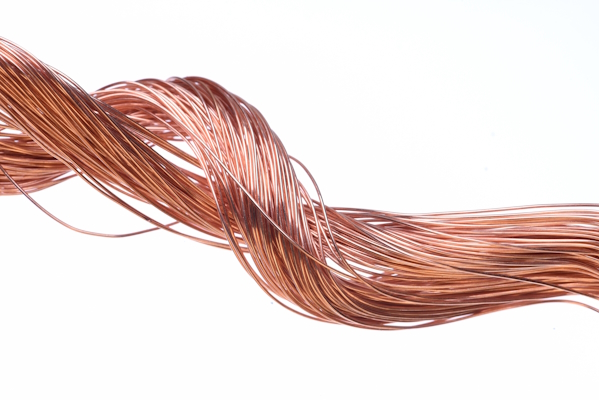
Figure 4: Copper is common wiring due to its excellent electric and heat conductivity.
FAQs
Which is better, copper or brass or bronze?
The better metal depends on the application. Copper has great electrical conductivity, brass has excellent machinability, and bronze offers excellent corrosion resistance.
Does bronze rust?
Most bronze alloys do not contain iron and therefore do not rust.