Compression Fittings & Copper Pipes
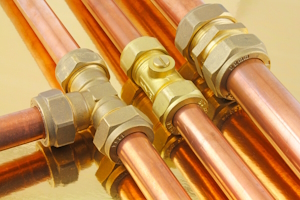
Figure 1: Brass compression fittings on copper pipes
Compression fittings offer a reliable and straightforward method for joining copper pipes without welding or soldering. This article explores compression fittings available for copper piping, describing their applications, installation procedures, and the factors to consider when choosing the right fitting for an application. Compression fittings are practical and efficient and provide a versatile solution for professional plumbers and DIY enthusiasts.
View our online selection of compression fittings!
Table of contents
- Compression fitting design
- Applications
- Best practices and what to avoid
- How to replace compression fittings on copper pipes
- Compression fittings vs soldering copper pipes
- FAQs
Compression fitting design
As seen in Figure 2, a typical compression fitting consists of three parts:
- The fitting body: This is the main part of the fitting and contains the threads that connect to the pipe or tubing.
- The compression ring: Also known as the ferrule, this ring is placed over the tubing and provides the actual sealing force when compressed.
- The compression nut: This part is threaded onto the fitting body and, when tightened, compresses the ferrule against the tubing, creating a seal.
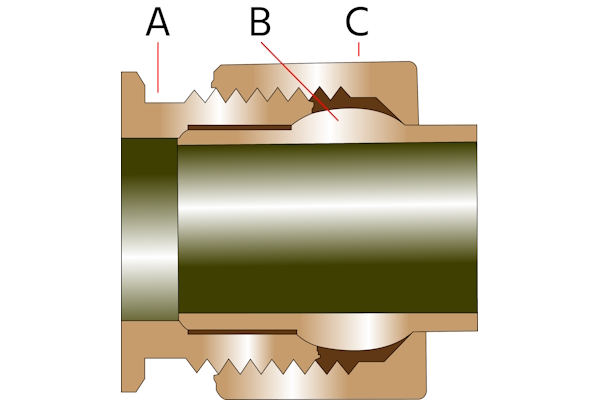
Figure 2: The typical components of a compression fitting: body (A), compression ring/ferrule (B), and nut (C).
When the compression nut is tightened, the ferrule is forced into contact with the fitting body and the piping. The pressure results in the ferrule deforming slightly, conforming to the shape of the piping and the fitting, which ensures a tight and secure seal that prevents fluid or gas from leaking.
Compression fitting materials for copper pipe
- Brass: Brass compression fittings for copper pipe make suitable connections due to their corrosion-resistant nature and ductility, which allow for a secure seal without damaging the copper piping. The compatibility of brass with copper ensures a long-lasting connection, making it ideal for water and gas applications within moderate temperature and pressure ranges.
- Stainless steel: Stainless steel compression fittings are also suitable for copper pipe connections. Their high strength and corrosion resistance make them suitable for high-pressure and temperature applications. Also, these fittings are suitable for aggressive fluids.
- Copper: Copper fittings can be used with copper pipes, offering a homogeneous connection that ensures compatibility in terms of thermal expansion and avoids galvanic corrosion. Their excellent thermal conductivity makes them particularly suitable for refrigeration applications where temperatures can vary significantly.
- Plastic: Plastic compression fittings are lightweight, corrosion-resistant, and often more cost-effective than metal options. They are suitable for copper pipes in low-pressure water applications, such as domestic plumbing systems. The non-conductive nature of plastic also means there's no risk of galvanic corrosion when used with copper piping.
Unsuitable material
- Carbon steel: Carbon steel fittings are not suitable for copper pipe connections. The dissimilar metals can induce galvanic corrosion, leading to the deterioration of the connection. Therefore, it is advisable to avoid using carbon steel fittings with copper piping to ensure the integrity of the piping system.
Applications
Compression fittings, known for their adaptability and ease of installation, are commonly used with copper pipes in various applications. These applications include plumbing, gas distribution, and HVAC systems, each with specific requirements that make compression fittings a good choice.
- Plumbing systems: Compression fittings work well in plumbing applications, where they allow the joining of copper pipes without the need for a soldered joint. This is a particular advantage in confined spaces or where the application of heat is impractical or unsafe.
- Gas lines: Copper pipes are commonly used to construct gas lines. Compression fittings can provide a secure, leak-proof connection. This secure connection is necessary in any environment because the safe distribution of gas helps prevent disasters.
- HVAC and refrigeration: Concerning HVAC fittings and refrigeration fittings, compression fittings are used to connect copper tubing in systems like air conditioners and refrigerators. The integrity of these connections is vital to prevent leaks of refrigerants and to maintain system efficiency.
- Instrumentation: Copper pipes in control and instrumentation systems benefit from the use of compression fittings. These applications demand precise connections, such as those in pressure gauges and sensors, where the integrity of the connection directly affects measurement accuracy.
Best practices and what to avoid
Best practices
- Ensure the copper tubing is cut squarely and without burrs before installation to prevent potential leaks.
- Inspect the compression fitting and ferrule for damage or imperfections that may compromise the integrity of the connection with copper pipes.
- Hand-tighten the compression nut to maintain proper alignment before fully securing it with tools.
- Use two wrenches when tightening: one to stabilize the fitting body and the other to turn the compression nut. This is particularly important with copper pipes to avoid twisting the tubing.
- Adhere to torque specifications provided by manufacturers when securing compression fittings to copper pipes. Avoid under- and over-tightening. Learn more in our article on how to tighten compression fittings.
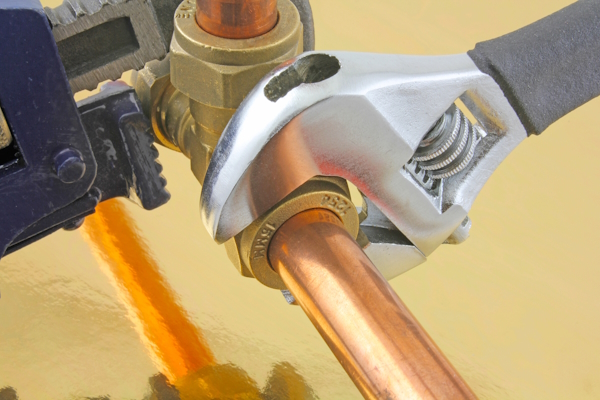
Figure 3: Use two wrenches when installing a compression fitting to prevent twisting the pipe.
What to avoid
- Do not reuse ferrules on copper pipes; a new ferrule ensures a reliable seal.
- Don't overtighten, as this may deform the ferrule or damage the copper pipe, leading to potential leaks.
- Don't use compression fittings on copper pipes that will experience dynamic stresses, such as vibration, which can loosen the fitting over time.
- Do not exceed the temperature and pressure ratings with copper pipes, as it can result in fitting failure.
- Don't install compression fittings on copper pipes in places where inspection and maintenance are challenging; regular checks are necessary to detect leaks early.
How to replace compression fittings on copper pipes
Removing and installing compression fittings on copper pipes is a relatively straightforward process that does not require specialized plumbing skills. It's important to proceed with caution to avoid damaging the pipe or fitting components.
How to remove a compression fitting from a copper pipe
- Shut off water supply: Before starting, ensure the water supply to the pipe is completely shut off to prevent water from spilling out during the process.
- Stabilize the fitting: Use one wrench to hold the fitting body steady. This prevents putting unnecessary stress on the copper pipe, which could cause it to bend or break.
- Loosen the compression nut: With another wrench, turn the compression nut counter-clockwise to loosen it. If the nut is stuck due to corrosion or over-tightening, apply penetrating oil around the nut and let it sit for a few minutes before attempting again.
- Remove the nut and ferrule: Once the nut is loose, slide it along the pipe, followed by the ferrule. If the ferrule does not come off easily, carefully cut it without damaging the pipe. A ferrule puller tool can also be used to remove a stubborn ferrule.
- Inspect the pipe: After removing the fitting, inspect the end of the copper pipe for any damage or deformity. If the pipe is damaged, it may need to be cut and re-prepared for a new fitting.
Installing compression fittings
- Prepare the copper pipe: Cut the pipe to the needed length with a pipe cutter for a clean, square cut. Remove any burrs with a deburring tool or sandpaper to ensure a smooth surface that will not damage the new ferrule.
- Slide on the components: First, slide the new compression nut onto the pipe, with the threads facing the end of the pipe. Next, place the new ferrule over the pipe.
- Insert the pipe into the fitting body: Insert the pipe into the fitting body until it stops. Ensure the pipe is straight and fully seated within the fitting.
- Hand-tighten the nut: Screw the compression nut onto the fitting body by hand until snug. Ensure the fitting is properly aligned and that the pipe is straight to avoid cross-threading.
- Tighten the compression nut: Using two wrenches, tighten the compression nut while holding the fitting body steady. It's important not to over-tighten; usually, a turn past finger-tight is sufficient to compress the ferrule and create a watertight seal.
- Check for leaks: Once the fitting is installed, slowly turn the water supply back on and check for leaks. If there's a slight weep, tighten the nut a bit more, but be cautious not to apply excessive force.
Compression fittings vs soldering copper pipes
When it comes to joining copper pipes, two common methods are using compression fittings and soldering. Each method has its advantages and disadvantages, and the choice between the two often depends on the specific needs of the project, skill level, and working conditions.
Factor | Compression fittings | Soldering |
Installation | Do not require special tools or skills. Accessible for DIYers and professionals. | Requires special skills and practice to ensure a reliable connection. |
Cost | More expensive than soldering materials | Cost-effective |
Size | Take up more space | Fit in line with the pipe |
Durability | Less durable | More durable than compression fittings |
Safety | No inherent risk | The use of an open flame increases hazards |
Reusability | Can be reused; sometimes the ferrule needs to be replaced | Not reusable |
When to choose each method
Choose compression fittings when working in a confined space, near flammable materials, or when the installation needs to be temporary or adjustable. They are also a good choice for those without soldering experience or when an immediate return to service is necessary.
Choose soldering for a permanent and less expensive solution in situations where aesthetics are important, such as in exposed piping. Soldering is preferable for large projects due to the lower material costs and when a low-profile joint is required.
FAQs
Is it OK to use compression fittings on copper pipe?
Yes, compression fittings are suitable for copper pipe. Ensure the fitting's material is suitable for copper pipe and the application the pipe is for.
Can you reuse a copper pipe compression fitting?
Some can be reused, but it's not recommended for a reliable seal.
Are compression fittings as good as soldering for copper pipes?
They're easier to fit but may not be as permanent as soldered joints.