Materials In Salt Water Applications
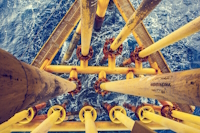
Figure 1: Corrosion is an unavoidable issue in salt water applications.
Various salt water-resistant materials are suitable for usage in marine environments due to their unique properties and resistance against corrosion. This article describes the characteristics, benefits, and potential drawbacks of stainless steel, cast iron, brass, and aluminum. Understanding these factors is crucial for selecting the ideal material for a given saltwater application, whether on the coast, above water, or submerged underwater.
Table of contents
- Corrosion in saltwater environments
- Metals in salt water applications
- PVC in salt water applications
- Rubbers in salt water applications
- Common material applications
- FAQs
View our online selection of salt water resistant products!
Corrosion in saltwater environments
Corrosion in a marine environment is a significant concern due to salt water's harsh and highly reactive nature. Corrosion in marine settings is accelerated by salt (sodium chloride), which acts as an excellent electrolyte, facilitating the flow of electric current and accelerating oxidation processes.
Several types of corrosion can occur in saltwater environments.
- General: General corrosion occurs when the entire surface of a metal corrodes at a uniform rate.
- Galvanic: Galvanic corrosion happens when two or more different metals come into electrical contact in a corrosive environment. The more active (anodic) metal corrodes at an accelerated rate, while the more noble (cathodic) metal is protected.
- Crevice: Crevice corrosion is localized corrosion in stagnant locations, such as those found under gaskets, washers, insulation material, fastener heads, surface deposits, and crevices in corroded metals.
- Pitting: Pitting is a form of highly localized corrosion that creates small holes in the metal.
- Intergranular: Intergranular corrosion, a selective attack on the grain boundaries of metal, can also occur in certain conditions, such as when metal is exposed to corrosive conditions for an extended period.
In each case, the corrosion process can lead to material loss, compromising the strength and integrity of structures, equipment, or vessels, potentially leading to failures and accidents. The economic cost of corrosion is high, requiring substantial resources for replacement and repair of the corroded material. Therefore, understanding and mitigating corrosion in saltwater environments is of critical importance.
Learn how to prevent corrosion in our anti-corrosion measures for valves article.
Metals in salt water applications
This section covers four metals that are commonly found in marine applications. The following table gives a brief overview of and comparison between the metals.
Table 1: Overview/Comparison table for the suitability of stainless steel, cast iron, brass, and aluminum in salt water applications
Metal type | Relative cost | Relative resistance to salt water | Relative strength and durability | Primary advantage | Primary disadvantage |
Stainless steel | High | High | High | Highly resistant to corrosion and high temperatures | Costly and not as malleable as other metals |
Cast iron | Medium | Low | High | High heat resistance and durability | Susceptible to rust |
Brass | Medium-High | High | Medium | Highly resistant to corrosion, good for hot water systems | Not as strong as steel, can be prone to dezincification |
Aluminum | Low | Medium | Low-Medium | Lightweight, good thermal and electrical conductivity | Lower strength, can corrode in highly alkaline or acidic environments |
Stainless steel
Stainless steel is a highly suitable material for use in saltwater environments. Stainless steel's factors that make it critical in marine settings are:
- Corrosion resistance: Stainless steel's primary characteristic is its remarkable resistance to corrosion, especially rust. This is mainly due to the presence of at least 10.5% chromium in its composition, which reacts with oxygen to form a thin, invisible layer of chromium oxide on the surface of the steel. This highly adhesive and non-reactive layer protects the steel from corrosive elements, including saltwater.
- Self-healing: If the chromium oxide layer is damaged, the exposed chromium in the steel will react with oxygen to restore the layer, providing a self-healing property not seen in most other metals.
- Durability: Stainless steel is durable, with high tensile strength and robustness. This makes it capable of withstanding the harsh conditions of marine environments, including the physical impacts that can occur in these settings.
-
Variety of grades: Different marine stainless steel grades are optimized for different environments. For instance, stainless steel 316, often called 316 marine-grade stainless steel, has an added element, molybdenum, which enhances its resistance to the corrosive effects of salt and other chemicals.
- 304 vs 316 marine grade stainless steel: While 304 and 316 stainless steel are both considered for salt water applications, 304 stainless steel's corrosion rates are much higher. Therefore, stainless steel 304 is not stainless steel for marine use.
- Low Maintenance: Stainless steel is easy to clean and requires minimal maintenance, making it a cost-effective option for long-term use in saltwater environments.
Cast iron
Cast iron is a significant material for products used in saltwater environments for the following reasons:
- Robustness and cost: Cast iron is robust, heavy, and durable. It requires minimal upkeep and is cost-effective to replace.
- Iron oxide layer: When cast iron is exposed to air, it naturally forms a thin and durable layer of iron oxide on its surface. This protective layer shields the underlying material from the corrosive effects of saltwater, expanding its lifespan and maintaining its structural integrity.
Cast iron is typically recommended for above water or near water applications. It is not recommended for underwater applications because it is particularly susceptible to rust when in direct contact with salt water for extended periods.
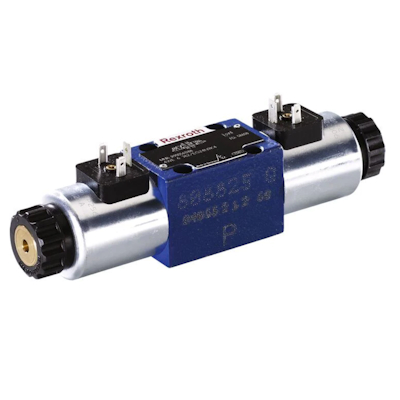
Figure 2: A cast iron hydraulic solenoid valve
Brass
Brass is a copper and zinc alloy. It is used in various applications, such as marine fittings, desalination systems, and heat exchangers. Naval brass is a common brass alloy used in saltwater applications. It consists of 59% copper, 40% zinc, and 1% tin with trace amounts of lead.
Dezincification
Brass will quickly tarnish when exposed to saltwater; however, it can still keep its structural integrity. In some situations, though, the zinc can be removed from the alloy, leaving only copper, which reduces its structural integrity significantly.
If there are red spots, mineral stains, or a white substance on the surface of brass, then dezincification has begun, and the brass component should be replaced as soon as possible. Dezincification occurs in polluted and acidic environments.
If the brass components may interact with an environment that leads to dezincification, there are several methods for slowing down and mitigating the process. A common method is to add arsenic into the naval brass alloy when manufacturing the component. However, anything done to protect brass against dezincification makes the process more complex and costly. Therefore, brass should be avoided if dezincification is likely and simpler material options are available.
Aluminum
Aluminum is used in saltwater environments because of its lightweight and high-strength properties. Also, aluminum is good at resisting corrosion. When a small amount of corrosion occurs, a thin layer of aluminum oxide naturally forms over the corroded surface, mitigating further corrosion. However, salt water and salt air can corrode faster than the protective layer can develop in some conditions. This can lead to pitting in the aluminum.
Protecting against aluminum corrosion in salt water is fairly simple. Traditionally, painting the aluminum's surface is enough to protect it. However, the paint must be quickly maintained whenever cracks or other flaws occur. More recently, however, powder coating has been developed. This creates a hard protective layer over the aluminum, leading to less maintenance over time.
Aluminum should not be used directly with more noble metals like copper. This contact can easily lead to galvanic corrosion.
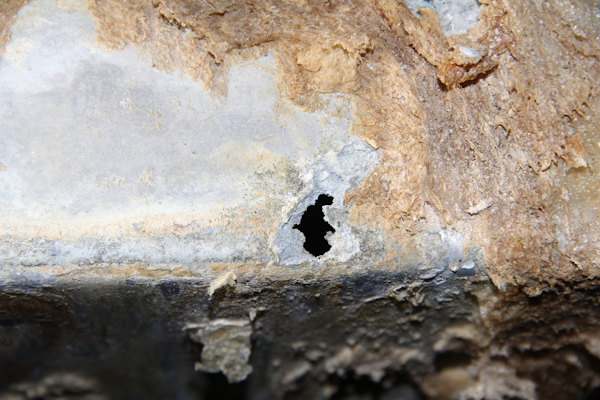
Figure 3: Corrosion in aluminum that was exposed to stagnant salt water for too long.
Aluminum alloys for marine applications
The most common aluminum alloys used in salt water applications are aluminum-silicon, aluminum-magnesium, and aluminum-magnesium-silicon alloys.
- Al-Si: Aluminum-silicon alloys have decent strength, making them suitable for engine block use. By adding elements like copper and magnesium, these alloys can also serve as welding filler. They are commonly used to create leak-proof, fatigue-resistant castings and crucial parts for marine uses.
- Al-Mg: Aluminum-magnesium alloys can't be heat-treated and are hard to shape, but they're very good at resisting rust, so they're great for parts that come into contact with seawater often.
- Al-Mg-Si: Aluminum-magnesium-silicon alloy is popular for its aesthetic and structural qualities and is great for finishing touches. It's commonly used for both indoor and outdoor architectural projects. These alloys can be heat-treated, have a fair amount of strength, can be shaped easily, and resist corrosion very well.
PVC in salt water applications
PVC and other plastic materials have long been recognized as suitable materials for salt water applications due to their unique properties that allow them to withstand the harsh environment of salt water.
- Corrosion resistance: PVC is resistant to salt water corrosion, which makes it an ideal material for salt water handling. Unlike metal pipes that erode over time due to salt water exposure, PVC pipes maintain their structure and functionality.
- Non-conductive: PVC does not conduct electricity. This is an essential characteristic in salt water applications as salt water is a good conductor of electricity. Thus, using PVC reduces the risk of electrical accidents.
- Cost-effectiveness: PVC components are generally less expensive than metal components. Also, due to being lightweight, it is easier and more cost-effective to transport and install. Finally, due to its resistance to corrosion, PVC requires less maintenance, reducing long-term costs.
Using PVC in salt water applications does have downsides:
- Sunlight sensitivity: Extended exposure to sunlight can cause PVC to become brittle and crack over time.
- Low chemical resistance: PVC has a relatively narrow range of chemical resistance. For example, exposure to organic solvents can cause PVC to become soft and lose its shape.
- Temperature and pressure: PVC typically has lower temperature and pressure ratings than metal. It can handle temperatures up to 60 °C (140 °F) and pressures up to 13.8 bar (200 psi).
Rubbers in salt water applications
System components that require a seal (e.g., valves) need the seal material also to be suitable for a saltwater environment. The three primary materials used are EPDM, neoprene rubber, and PTFE. Consider the following factors when selecting between them:
- Cost: If budget significantly affects material selection, EPDM and neoprene rubber seals are typically less expensive than PTFE seals.
- Resistance to salt water: All three materials have a high resistance to salt water. There is no significant difference between them.
- Resistance to the environment: EPDM has higher resistance to ozone, weathering, and UV radiation than the other two materials. This makes it especially suitable for outdoor salt water applications.
- Chemical resistance: PTFE has a wider resistance to chemicals than the other two materials. Read our chemical resistance guide to learn more.
-
Temperature range: The three materials, on average, have the following temperature ranges:
- PTFE: -20 °C to 180 °C (-4 °F to 356 °F)
- EPDM: -50 °C to 120 °C (-60 °F to 250 °F)
- Neoprene: -40 °C to 120 °C (-40 °F to 250 °F)
-
Pressure ratings: The three materials have the following pressure ratings:
- PTFE: 20 bar (290 psi)
- EPDM: 10 bar (145 psi)
- Neoprene: 15 bar (217 psi)
- Note: Temperature ranges and pressure ratings are subject to significant change depending on the seal's specific structure. Therefore, use the above information as a general guideline, but always check with a product's manufacturer for specific values.
Hydrocarbon applications
EPDM and neoprene are unsuitable for applications involving oils, gasoline, and other hydrocarbons. Only PTFE is highly resistant to these media.
Common material applications
Use the following example applications as guidelines for understanding which materials to choose for system components, such as valves and fittings:
- Stainless steel: Stainless steel valves and fittings can be used in a variety of salt water applications due to their corrosion resistance. In the maritime industry, they control fluid flow in ships, submarines, and offshore drilling platforms. In desalination plants, they manage the flow of seawater and the resulting fresh water.
- Cast iron: Cast iron valves and fittings are less corrosion-resistant than stainless steel. They are used where strength is required, and saltwater exposure is not constant. They can be found in salt water cooling systems, ballast systems in ships, and certain components of offshore platforms.
- Brass: Brass valves and fittings are saltwater resistant and used in marine plumbing systems. They are common in the cooling and heating systems of boats, ships, and saltwater treatment plants.
- Aluminum: Aluminum valves and fittings are often used in marine vessels, especially where weight is a concern. They might be used in certain lightweight boats' hydraulic systems or saltwater aquarium setups.
- PVC: PVC valves and fittings are highly saltwater resistant and often used in maritime applications where corrosion resistance is essential, but metal components are unnecessary. They are used extensively in seawater plumbing systems, desalination plants, and aquaculture industries to control water flow.
FAQs
Will stainless steel rust in salt water?
Stainless steel is highly resistant to corrosion from salt water; however, it will eventually rust and corrode if directly exposed to salt water for an extended period.
Is brass salt water resistant?
Brass is not salt water resistant. It will at least tarnish and, at most, go through dezincification, which ruins its structural integrity. Naval brass is a more resistant option.