Disc Valve - How They Work
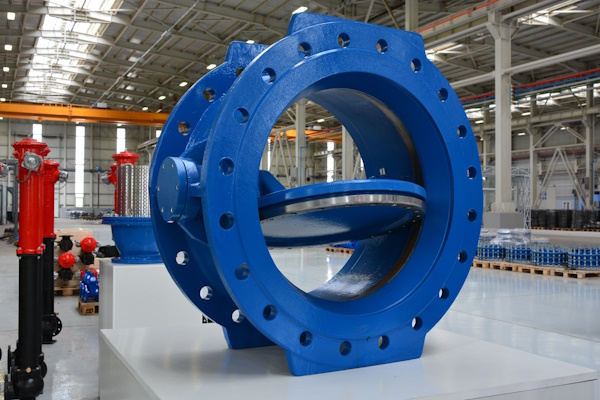
Figure 1: Butterfly valve showing an open disc
Disc valves have a disc within the valve to either completely block or partially allow flow through the pipe. The term 'disc valve' is not a specific valve type, but rather a general description for valves that utilize a disc to control flow. These discs are integral to the operation of several types of valves, including check valves, and butterfly valves, where they help create a pressure-tight seal. Disc valves are versatile, being suitable for a wide range of applications, from high to low pressure, and are particularly effective in process lines, hot water systems, and with viscous or corrosive materials. This article discusses the operation, types, and design features of disc valves.
Table of contents
View our online selection of disc valves!
How do disc valves work?
Disc valves typically function by utilizing a circular disc mounted on a central shaft or hinge. The disc can move to open or close the flow path. The rotation of the disc is typically achieved through a manual lever, geared operator, or actuator (pneumatic, electric, hydraulic) depending on the application requirements.
The operation of a disc valve varies depending on the valve it is part of. However, all disc valves share the common feature of having the disc act as the main barrier to pressure. The discs are usually made from durable metals to withstand such pressures, and different methods are used to position the disc accordingly. Their operations depend on their specific types. In the following section, we will look at different types of disc valves.
Types of disc valves
This section discusses the common types of disc valves. There are many more disc valves, each tailored to specific manufacturers or applications, within these general categories.
Butterfly valves
Butterfly valves use discs to completely close off a pipeline and are available in various designs. There are three primary types: zero offset, double offset, and triple offset butterfly valves.
- Zero offset valves, or concentric valves, feature a disc that rotates around the pipe's central axis and are typically used in conditions up to 13.7 bar (200 psi) and 204 𐩑C (400 𐩑F) for general purpose applications.
- Double offset valves, known as high-performance butterfly valves, have two offset stems that create a camming action to move the valve disc, allowing them to handle higher pressures.
- Triple offset valves are designed with three offset stems, enabling a frictionless seal with the disc seat. This reduction in friction ensures a uniform seal, making these valves suitable for use with superheated steam or gasses and other high-demand, leak-proof applications.
Read our butterfly valve design article for more information on the various design options available for butterfly valves.
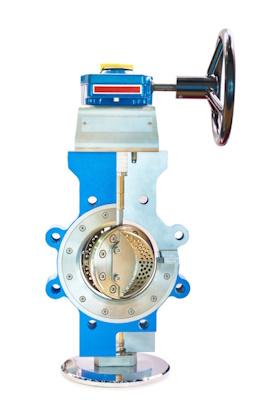
Figure 2: Triple offset butterfly valve
Disc check valves
Disc check valves are designed for preventing backflow, ensuring that process fluid flows only in the intended direction and not in reverse. These valves can be closed using various mechanisms, like a tilting disc, a spring-loaded mechanism, or wafer style. In each case, the valve disc functions to block any reverse flow into the pipe. They prevent backflow in pump discharge lines, gravity-fed systems, and protect equipment from pressure surges. Read our check valve overview article for more information on the design and operation of various check valve types.
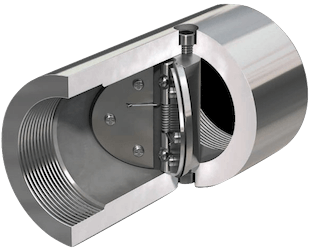
Figure 3: Butterfly, or wafer check valve
Disc valve for proportional control
Proportional control in disc valves allows for the precise regulation of flow rates through the valve. Unlike traditional on/off valves that are either fully open or fully closed, proportional control valves can adjust their opening to any position between fully open and fully closed. This enables the valve to regulate the flow of media with great precision, based on external control signals, typically in the form of 4-20 mA current loops. This is essential in applications requiring fine-tuned flow adjustments to maintain specific process conditions.
Burkert disc valve 3285
The Burkert 3285 is an advanced proportional integrated process controller disc valve, designed to offer precise control over the flow of media through the use of an integrated PID controller. This controller adjusts the flow based on external 4-20 mA input signals, ensuring accurate regulation tailored to specific requirements. The valve's design features two oxide ceramic discs: one stationary with a hole and one rotating disc that also contains a hole. By adjusting the rotation of the movable disc, the alignment of these holes can be finely controlled, allowing for the valve opening to be adjusted from fully open to proportional to fully closed. This mechanism provides exceptional control over the flow rate, ensuring efficient and precise flow regulation.
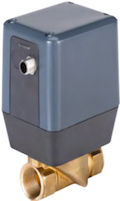
Figure 4: Burkert 3285 disc valve
Sanitary disc valve
Sanitary valves, while functionally similar to other disc valves, are specifically designed to maintain sterile conditions for the processed fluid. The disc in these valves is often rounded to facilitate a smooth flow of the product. Commonly constructed from inert materials like stainless steel, these valves are ideal for use with dairy products, pharmaceuticals, beverages, cooking oils, and other food-related or chemical substances. The disc valve, when utilized as a sanitary valve, is particularly favored for its versatility in handling different viscosities and slurries, as well as providing effective shut-off capabilities for such applications.
Design considerations
Disc design
-
Material: The disc material selection depends on the intended service and fluid characteristics. Common materials include:
- Metals: Cast iron, stainless steel (various grades for temperature and corrosion resistance), exotic alloys for high-pressure or corrosive applications.
- Plastics: PVC, CPVC, PP (Polypropylene) for lower pressure, non-corrosive media.
- Liners: Soft or resilient liners (e.g., PTFE - Teflon) can be used for better sealing or compatibility with specific fluids.
-
Shape: The disc shape can influence flow characteristics and pressure drop across the valve. Common shapes include:
- Circular: Most common, provides good shutoff and flow control.
- Eccentric: Offers improved shutoff and reduced wear on the sealing surfaces.
- Butterfly: Primarily used for on/off applications, offers a low-pressure drop design.
Seat design
- Material: Similar considerations as the disc material, ensuring compatibility and wear resistance.
-
Sealing mechanism: The design of the seat and its interaction with the disc determines sealing effectiveness. Common types include:
- Soft seat: Utilizes a compressible gasket or elastomeric material for tight shutoff. Suitable for lower pressure applications.
- Metal seat: Provides a more robust seal for high-pressure applications. May require lapping (rubbing the metal seat and disc together with an abrasive paste to remove imperfections) for optimal sealing.
Body design
- Material: The body material is chosen based on pressure rating, temperature requirements, and compatibility with the flowing fluid. Common materials include cast iron, ductile iron, stainless steel, and alloy steel.
- Flange or wafer style: The body style dictates how the valve connects to the piping system. Flanged valves have raised faces with bolt holes for direct connection with flanges on pipes. Wafer style valves fit between pipe flanges and are secured with bolts through the body.
- Port design: The size and configuration of the inlet and outlet ports (full or reduced bore) impact flow characteristics and pressure drop.
Shaft and bearing design
- The shaft material needs to be strong enough to handle the operating torque and ensure smooth disc rotation. Stainless steel is a common choice.
- Bearings support the shaft and minimize friction during operation. Depending on the application, bearings can be lubricated or self-lubricating.
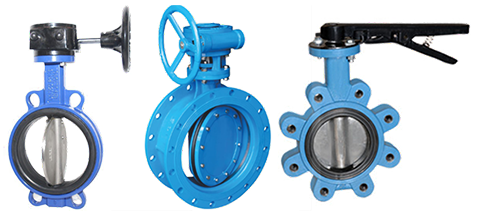
Figure 5: Butterfly valve connection types; wafer type butterfly valve (left), flanged butterfly valve (middle), and and lug-style butterfly valve (right)
Selection criteria
- Valve size: Identify the diameter of the pipe connecting to and leading from the valve. This helps select the appropriate valve size, the type of disc valve needed, necessary flow rates, and the forces the valve must endure. Consider the valve's external dimensions to ensure it fits within the available space without causing any spatial constraints.
- Pressure and temperature range: Understand the working pressures and temperatures of the process fluids. Disc valves are pressure-rated based on their design (e.g., concentric vs. double offset) and intended use, so knowing the operational pressure range is essential for narrowing down your options. If high temperatures are involved (e.g., with superheated vapors or hot chemicals), ensure the valve is rated for such conditions.
- Type of actuator: Disc valves can be operated by manual handwheels, electric actuators, pneumatic actuators, or hydraulic actuators. Selecting an actuator depends on the required control precision, speed of operation, available power sources, and environmental considerations. Electric actuators suit precise control, pneumatic for fast response, and hydraulic for high force applications.
- Connection type and material: The required pressure ratings decide the type of pipe connections needed. Options include threaded, riveted, flange, and welded connections, with threaded being suitable for lower pressures and flange or welded connections for higher pressures. Choose the most appropriate material for the valve, considering the process fluids. For instance, sanitary valves often use stainless steel to avoid chemical interactions with the fluids.
Applications
Disc valves are utilized across a wide range of industries due to their versatility and reliability. Here are some key applications where disc valves play an essential role:
- Hot water systems: Disc valves are used to control the flow and temperature of hot water, ensuring efficient operation and safety in residential, commercial, and industrial settings.
- Pharmaceutical manufacturing systems: In the pharmaceutical industry, maintaining sterility and precise control over process conditions is crucial. Disc valves, especially those designed for sanitary conditions, are used to control the flow of liquids and gasses without contaminating them.
- Food/chemical processing plants: Similar to pharmaceuticals, the food and chemical industries require valves that can handle various viscosities and maintain purity. Disc valves are chosen for their ability to provide a tight seal and resist corrosion from aggressive substances.
- High-pressure applications: Disc valves are designed to withstand high pressures, making them suitable for applications where controlling the flow under such conditions is necessary, including oil and gas pipelines, water treatment facilities, and power plants.
- Breweries: The brewing industry benefits from the use of disc valves in several stages of production, from controlling the flow of ingredients to managing the fermentation process. Their durability and ease of cleaning make them ideal for these applications.
- Corrosive applications: Disc valves made from materials like stainless steel can resist corrosion from harsh chemicals, making them suitable for use in environments where corrosive substances are processed.