Butterfly Valve Design Differences
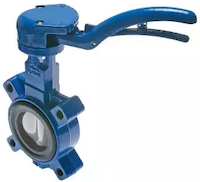
Figure 1: Butterfly valve
Butterfly valves are among the most popular industrial quarter-turn valves that control different fluid media flow-through systems. They come in different designs, offering varied advantages, such as the quarter-turn control, small dimensions for use in areas with limited space, and excellent control capabilities. They are also light, cheaper, and allow for a high flow coefficient, making them useful in many applications. However, their designs make them difficult to clean and prone to cavitation and choke. Throttling is limited to low differential pressure. This article discusses the various design options available for butterfly valves.
Table of contents
- What is a butterfly valve?
- Butterfly valve types
- Butterfly valves advantages and disadvantages
- Butterfly valve applications
- FAQs
View our online selection of butterfly valves!
What is a butterfly valve?
A butterfly valve is a quarter-turn valve that works similarly to a ball valve. As the name suggests, the butterfly is a disk connected to a rod or spindle that opens and closes in a way reminiscent of a butterfly's flapping wings. The butterfly valve closes when the rod rotates the disc 90° to a position perpendicular to the flow direction, thus restricting flow. It opens when the disc rotates back to allow the flow of media. Butterfly valves are used across many industries for throttling, on-off, or modulating services to control the flow of media (gas, liquid, or slurries) through industrial systems. They allow fluid flow in only one direction. Read our article on butterfly valves for more information.
Butterfly valve types
Butterfly valves have different designs, each serving specific applications and pressure ranges. They are classified in different ways, including their disc closure design, function, connection design, control or actuation method, actuator speed, and seat material.
Based on disc closure design
Butterfly valves can be concentric or eccentric depending on the spindle's or stem's position relative to the disc and the seat surface on which the disc closes.
Centric or concentric butterfly valves
Concentric butterfly valves are suitable for low-pressure applications. A concentric butterfly valve is the most basic type. The spindle passes through the centerline of the disc, located at the center of the pipe bore. The valve seat sits in the inside periphery of the valve body. The disc contacts the seat at around 85° during a 90° rotation. This design is known as resilient-seated because it relies on the rubber seat to efficiently seal the flow when closed.
Eccentric butterfly valves
Eccentric butterfly valves have the stem passing behind the disc’s centerline, on the opposite side of the disc to the flow direction. These valves can be single-offset, double-offset, or triple-offset.
- Single-offset: The stem is located right behind the centerline.
- Double-offset: Also referred to as doubly eccentric, these valves have the stem behind the disc with an additional offset to one side, enabling the disc to rub over the seat for only 1-3° of rotation during closure.
- Triple-offset butterfly valve (TOV or TOBV): These are similar to double-offset valves, but the third offset makes these valves more efficient and resistant to wear and tear.
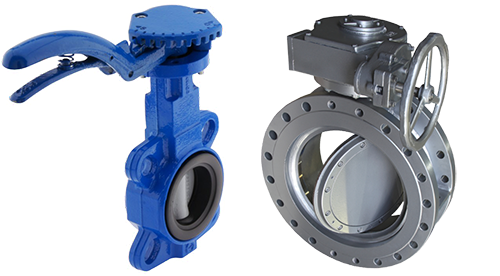
Figure 2: A zero offset butterfly valve with a lever handle (left) and an eccentric butterfly valve with a hand wheel and gearbox (right)
Based on body construction and connection design
Wafer-style butterfly valves
A wafer-style butterfly valve presents the most economical design. It is sandwiched between two pipe flanges to allow flow and sealing against bidirectional differential pressures and backflow in universal flow systems. It's light, offering a lower initial and installation cost.
These valves may or may not have flange holes outside their body (Figure 3, left). The pipe flanges are connected to piping using long bolts that run through the entire valve body. Gaskets, o-rings, and flat valve faces achieve the sealing between the valve and pipe flanges.
Flanged-style butterfly valves
Flanged butterfly valves use a disc or vane centrally mounted on a shaft, stem, or flange, which acts as the axis of the rotating disc. These valves have two flanges on either end (Figure 3, middle), giving them a larger face-to-face than lugged or wafer valves. The position and direction of the disc relative to the flanges determine the flow direction.
Flanged butterfly valves can be rotary, pneumatic, or hydraulic with applications in water distribution, chemical services, and ventilation, among others.
Butt-welded butterfly valves
Butt-welded butterfly valves are double- or triple-offset that are resistant to extreme temperatures, pressure, and corrossion. This makes them suitable for use in heating systems, natural gas, energy, chemical, refinery, and chemical services.
Lug-style butterfly valves
These valve types have threaded inserts (lugs) outside the valve (Figure 3, right). They have protruding legs providing bolt holes matching those in the pipe and flanges, and the valve is installed between two flanges using a set of bolts for each flange. The installation allows for dead-end service or eliminating downstream piping without affecting the other side. A comparison between lug-style and wafer-style butterfly valves is in the table below.
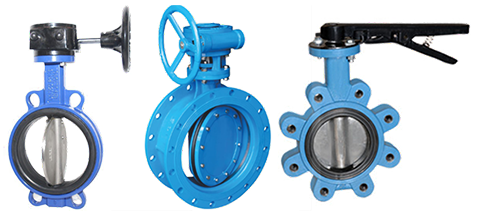
Figure 3: Butterfly valve connection types; wafer type butterfly valve (left), flanged butterfly valve (middle), and and lug-style butterfly valve (right).
Lug-style vs wafer-style butterfly valves
Lug-style butterfly valve | Wafer-style butterfly valve |
Suitable as an end valve | Not suitable as an end valve |
Easier to center | Difficult to center |
Less sensitive to extreme temperature differences | Unconducive for high-temperature applications |
Heavier with larger sizes | Lighter |
Only bolts are required for valve installation | Bolts and nuts required for valve installation |
More expensive | Less expensive |
Hard to install | Easy to install |
Based on seat material
The seat is what the disc seals against to allow or shut off flow. Butterfly valves have soft or metal seat materials, depending on application and cost. Inexpensive valves might have irreplaceable or unrepairable seats molded into the body. These are usually metal. Most precision valves, on the other hand, have soft seats. These seats are not permanently affixed to the body and are repairable and replaceable.
Metal seated butterfly valves
These valves have both sides of the seal made of a metal material such as steel, copper, graphite, combinations, alloys, or any other hard material. Although these seals are resistant to high temperatures, abrasion, and corrosion, they have relatively poor sealing performances.
Soft seated butterfly valves
One side of soft seated butterfly valves is metal material like steel. The other has a soft, elastic, non-metallic material such as rubber or tetrafluoroethylene, providing excellent sealing. However, this seal isn't resistant to high temperatures, wears quickly, and has poor mechanical properties.
Based on the actuation method
The butterfly valve actuator operates the stem and disc, controlling the opening and closing of the valve. Actuation can be manual (lever or hand-operated) or automatic (electric, pneumatic, or hydraulic).
Manual actuation
Manual butterfly valve actuators are operated manually with a hand-lever (Figure 4 labeled A) or a gear to open or close the valve. They're cheap and are widely applicable in remote systems that may lack access to power. However, gear-operated valves are self-locking and are used for slightly larger butterfly valves.
Automatic actuation
These are power-operated actuators that enable remote control of butterfly valves. They're more expensive than manual actuators and enable the rapid operation of larger valves. Automatic actuators can also be designed to fail-open or fail-close to keep the valve closed or open in case of actuator failure.
Automatic actuators can be:
- Electric: Use an electric motor and allow manual, semi-automatic, or automatic operation to control valves (Figure 4 labeled B).
- Pneumatic: Automatic or semi-automatic actuators that use compressed air to move a piston or diaphragm to control valve movement (Figure 4 labeled C).
- Hydraulic: Require hydraulic pressure to move a piston or diaphragm to open or close a valve automatically or semi-automatically.
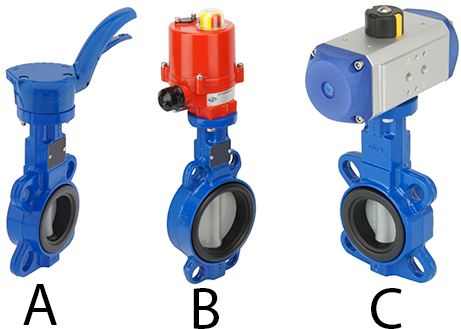
Figure 4: Butterfly valve actuation methods: manual (A), electrically actuated (B), and pneumatically actuated (C)
Butterfly valves advantages and disadvantages
Advantages
- Available in large sizes, from DN 40 to over DN 5000 for various industrial applications
- Compact, lightweight design
- It can be used with chemical or corrosive media under high temperatures
- High flow coefficient
- Minimal pressure drop and fast pressure recovery
- Has a bubble-tight seal
- Quarter-turn, which allows faster closing or opening
Disadvantages
- Difficulty with slurries
- Low differential pressure throttling only
- Potential cavitation and choking
- Unguided disc movement is affected by flow turbulence
- Difficult to clean
Butterfly valve applications
Butterfly valves have a wide range of applications in:
- Chemical services
- HVAC
- Oil, gas, and fuel handling
- Water and waste treatment
- Compressed air or gas applications
- Vacuum services
- Shipbuilding
- Pharmaceuticals
- Water supply
- Food processing
- Fire protection
FAQs
What is a butterfly valve?
A butterfly valve is a quarter-turn rotary motion valve that controls fluid or media flow, allowing fast control, low-pressure drop, and high-pressure recovery.
Are butterfly valves bidirectional?
Like most industrial valves, butterfly valves can be bi-directional. However, they often have a preferred flow direction that helps lower torque and extend their life.
What is a lug-style butterfly valve?
Lug-style butterfly valves have threaded lugs placed on the flanges for bolt connections. These valves are typically composed of metals and are suitable for end-of-line services.