Types, Use, and Functions of lubricants
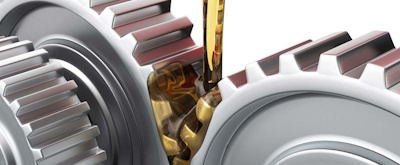
Figure 1: Oil as a lubricating agent
Lubricants are substances typically used to reduce friction between parts in contact. Depending on the type, lubricants also perform various other functions such as heat regulation, power transmission, sealing against dust or dirt, as well as reducing oxidation and preventing corrosion. Lubricants are typically in liquid or semi-solid form, but they may exist in different forms. Some examples include:
- Solid: Graphite, Molybdenum disulphide, Polytetrafluroethylene
- Semi-solid: Grease
- Liquid: Water, natural or synthetic oils
- Gaseous: Air
These lubricants are widely used in industries including automotive, aerospace, construction, chemical, or textile industries to ensure the smooth functioning of their machinery and equipment.
Note: Currently we do not sell any lubricants.
Table of contents
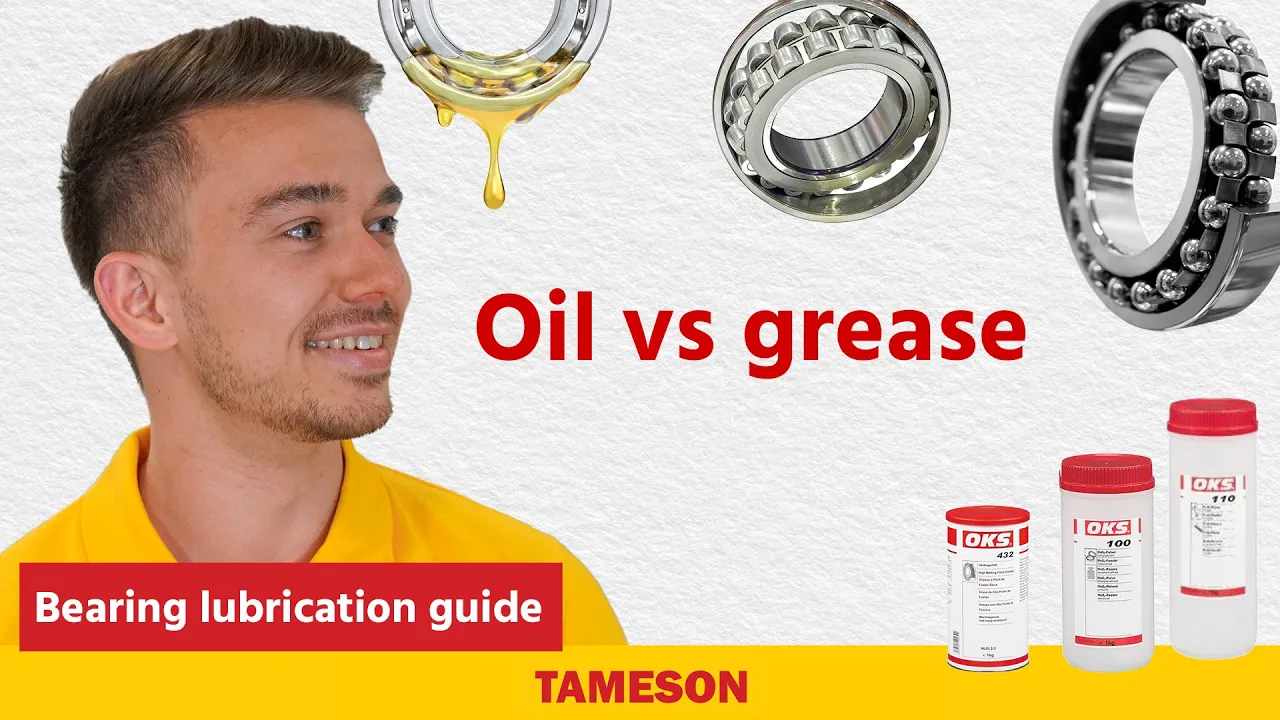
Why are lubricants important?
The movement of two surfaces can create resistance due to friction (figure 1 left). This can lead to the wear and tear of the machinery. In automotive or manufacturing applications, lubricants facilitate the uninterrupted movement between machinery parts. It does so by reducing the mechanical resistance between the material surfaces. As the lubricant is applied to the material surfaces, it creates a thin film and cushions the microscopic roughness in the surface to make the sliding of the materials easier with less resistance (figure 1 right). Liquid lubricants are especially beneficial in this case, as they can take any shape to smooth out the uneven surface and reduce friction.

Figure 2: Friction mechanism: The image on the left shows two rough surfaces with a high amount of friction, creating resistance. The image on the right shows how the addition of lubricant creates a thin film that makes sliding of materials easier.
The amount of friction can be calculated with the following Coefficient of friction formula, where:
- μ = static (μs) or kinetic (μk) frictional coefficient
- Fn = Applied normal force
- Fr = Friction force
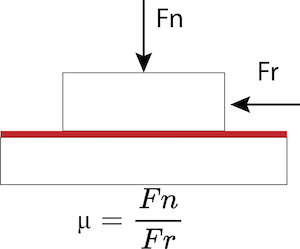
Figure 3: This shows the tribology system, here Fn is the force applied to the sliding surfaces, Fr is the friction force (movement), and the red line indicates the addition of lubricant which lowers the kinetic frictional coefficient.
Friction can be divided into sliding friction, pivoting friction, rolling friction and rolling resistance friction. Determining friction is an important step in any mechanical operation, learn more in our three-part Tribology series of articles.
The functions of Lubricants
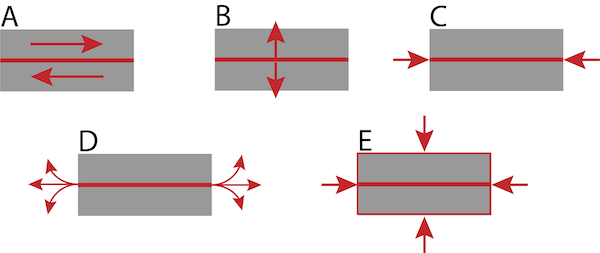
Figure 4: Lubricant functions: lubricating (A), separating (B), sealing (C), heat transfer (D), protecting (E)
Despite what the names suggests, lubricants have many more advantages than just lubricating and are responsible for extending the longevity and lifespan of machine components. The advantages include:
- Lubrication (A): For surfaces operating in contact with each other, lubricants such as grease and oil can be used to reduce friction and prevent wear and tear.
- Energy efficiency (B): The use of proper lubricants reduces friction, minimizes wear and tear, and maximizes performance. Thus, it is possible to reduce energy consumption and minimize resource usage.
- Seal against contaminants (C): Lubricants create a thin film in the material surface, which creates a barrier between the internal component of the material and the external environment. In addition, any contaminants are transported to the tank or filter with the help of lubricants where they can be removed.
- Heat reduction/control (D): The lubricant reduces the friction between parts, thus also reducing the heat generation. However, in the case where heat is generated, the lubricant can absorb and transfer it along with the help of flowing lubricants.
- Corrosion prevention (E): The surface coating provided by the lubricants prevents the possibility of oxidation or corrosion in the metal. Learn more about corrosion prevention in our anti-corrosion measures for valves article.
Types of lubricants
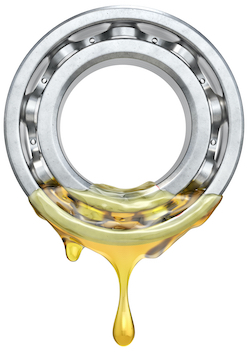
Figure 5: Oil used as lubricant on a bearing
Depending upon the application, one type of lubricant will work better then another. For intense friction and high-speed applications, oil-based lubricants are usually the best choice. However, for components that undergo heavy loads, or are positioned or move vertically, typically require a grease. Grease stays in place and provides a longer lasting barrier between components, such as wheel-bearings, nuts, bolts, etc. Read our bearings article to learn more about all the aspects involved with lubricating bearings.
Oils
Oil is the most commonly used lubricant in manufacturing plants. It is used for applications with gears, hinges, bearings, etc. They are suitable to use in high temperatures and high-speed applications. For oxidation and corrosion prevention, it is possible to use additives such as anti-oxidants or rust inhibitors with the base oil to enhance its properties. Base oil refers to the main ingredient that is present in most lubricants. For ease of selection, base oils are divided into the following types:
Table 1: Base oil classification
Base oil | Density [at 20°C (g/ml)] | Setting point [°C] | Flashing point [°C] |
---|---|---|---|
Mineral oils | 0.9 | -40 to -10 | < 250 |
Synthetic hydrocarbons | 0.85 | -50 to -30 | < 200 |
Ester oils | 0.9 | -70 to -35 | 200 to 270 |
Poly glycol oils | 0.9 to 1.1 | -55 to -20 | 150 to 300 |
Silicone oils | 0.9 to 1.05 | -80 to -30 | 150 to 350 |
Oil viscosity
Viscosity is an important parameter in the selection of oil. It refers to the nature of flow that oil exhibits at a specified temperature. Here are some general takeaways that apply to the viscous attribute of oil:
- Increase in temperature decreases the viscosity of the oil and vice versa.
- Low viscosity for low pressure stress and high sliding speeds.
- High viscosity for high pressure stress, low sliding speeds and high temperatures.
For determining the viscosity for your oil, it is necessary to understand the two categories of viscosity: dynamic viscosity and kinematic viscosity. Dynamic viscosity is the measure of fluid’s resistance to flow whereas kinematic viscosity is the measure of the velocity of fluid flow. Mathematically this can be shown as:

Figure 6: Dynamic viscosity calculation
Furthermore, industrial oils are divided into several viscosity grades according to ISO. These grades and their respective value are presented in the table below.
Kinematic ISO- viscosity grade | Viscosity [at 40°C] [mm²/s] |
---|---|
15 | 13.5 – 16.5 |
22 | 19.8 – 24.2 |
32 | 28.8 – 35.2 |
46 | 41.4 – 50.6 |
68 | 61.2 – 74.8 |
100 | 90 – 110 |
150 | 135 – 165 |
220 | 198 – 242 |
320 | 288 – 352 |
460 | 414 – 506 |
680 | 612 – 748 |
1000 | 900 – 1000 |
1500 | 1350 – 1650 |
Despite the base oil type and viscosity grade of the oil, how you apply it plays an important role. The oil applied after proper surface preparation prevents dust from gumming up. It is also inadvisable to use oil on the surfaces that are wet as the water can lower the adhesion of the oil and wash it away from the part over time.
Greases
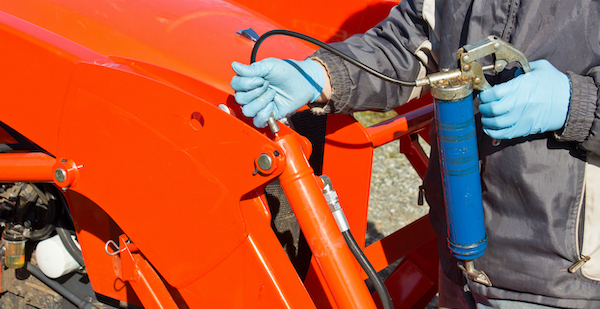
Figure 7: Applying grease with a grease gun.
Grease is the mix of oil, thickener (soap), and additional lubricants (such as Teflon). The mix of these components gives grease a different texture, thickness, and viscosity. However, it exhibits a similar lubricating property as oil. It is used in applications where oils cannot be used or where the cooling attribute of the oil is not required. Grease provides excellent protection against wear and tear and provides excellent sealing against foreign particles. It can often be used with gears, bearing, spindles, chains, linkages, etc.
The thickener is what provides consistency and fosters the performance of the grease. The types of thickeners and their specifications are indicated below:
Table 2: Maximum operating tempertaure of solid lubricants
Thickener (soap) | Operating temperature [°C], Mineral oil | Operating temperature [°C], Syntheseol | Drop point [°C] | Water resistance | Load capacity |
---|---|---|---|---|---|
Calcium | -30 to 50 | N/A | < 100 | ++ | + |
Lithium | -35 to 120 | -60 to 160 | 170 to 200 | + | - |
Al- complex | -30 to 140 | -60 to 160 | >230 | + | - |
Ba- complex | -25 to 140 | -60 to 160 | >220 | ++ | ++ |
Ca-complex | -30 to 140 | -60 to 160 | >190 | ++ | ++ |
Li- complex | -40 to 140 | -60 to 160 | >220 | + | - |
Bentonitee | -40 to 140 | -60 to 180 | N/A | + | - |
Polycarbamide | -30 to 160 | -40 to 160 | 250 | + | - |
Grease consistency
Consistency is a defining attribute in the assessment of grease strength. It is greatly influenced by the viscosity of the base oil and the amount of thickener used. Selection of correct consistency is important in the lubricating application as soft greases can move away from the area of application while hard greases may not be able to properly move to reduce the effectiveness of lubrication.
Pastes
Paste provides a similar working function as grease. However, it consists of a greater mix of solid lubricants which gives it its thick texture. The combined effect of base oil, thickeners (may or may not be included), and a solid lubricant such as PTFE protects against friction wear and tear. The addition of different solid lubricants makes the use of paste suitable in different types of applications.
Type | Maximum operating temperature [°C] |
---|---|
PTFE | < 300 |
MoS₂ (Molybdenum disulphide) | < 450 |
Aluminium | < 1100 |
Copper | < 1100 |
“Oxide” ceramics | < 1400 |
Graphite | < 600 |
PTFE and MoS₂ are two widely used solid lubricants. PTFE provides good load capacity and can withstand high compressive strength. It exhibits a low coefficient of friction. MoS₂ exhibits a nominal frictional coefficient. However, it provides excellent pressure absorption capacity and wear resistance.
Most pastes are reliable when it comes to corrosion protection and lubrication in high pressure and temperature applications. Most commonly, pastes are used as lubricants with nuts, bolts, or gear wheels.
Dry lubricants
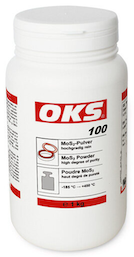
Figure 8: MoS2 powder with a high degree of purity
Dry lubricant is suitable when oil or grease cannot be used for lubrication purposes in extreme operating conditions such as vacuum, corrosive environment, or extreme temperatures. These can be classified into powdered form solid lubricants, sliding film, or bonded coatings and are usually available in spray form. They also can be mixed with water, alcohol, or other solvents. There are three major ways these dry lubricants can be applied:
- Immersion: Suitable for batches of fasteners, or other components with smaller diameters.
- Spraying: Most commonly used; application process can be hindered by internal bends or smaller diameters.
- Burnishing: Not commonly used; manual application is required.
Once the lubricant is applied using either of these methods, it is left to evaporate which eventually leaves a thin film of lubricant on the metal surface. Dry lubricants particles like graphite can be extremely slippery which means dust or dirt is not easily attracted to attached to the surface. Apart from graphite, PTFE and MoS₂ are also commonly used as solid particles in the dry lubricant.
Additives
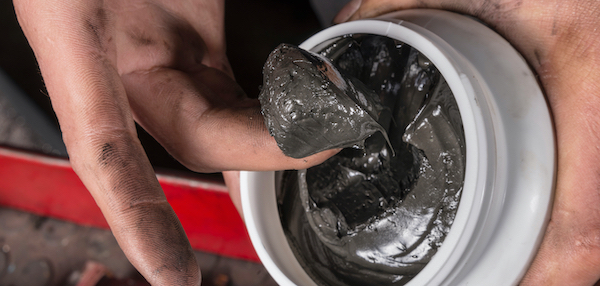
Figure 9: Graphite
Additives are an important addition to the base oil to enhance the properties of the lubricants. They are organic or inorganic chemical compounds that are usually blended at the rate of <1 to 35 % of the oil volume. Most industrial applications include the following types of additives in oil for the purpose of performance enhancement to address their problems:
- Antioxidant: To prevent oxygen from breaking down the lubricant and causing oxidation.
- Extreme pressure: To increase lubricant’s ability to carry the load, for instance in gears and bearing.
- Demulsifier: To enhance lubricants’ ability to repeal water.
- Defoaming: To help in the breakup of foam bubbles.
- Film strengtheners: To enhance the ability of lubricant film to attach to the surface.
- Viscosity improver: To improve the viscosity of the lubricant at high temperatures.
- Pour point: To decrease pour point temperature of lubricant in cold temperature. The pour point of an oil is measured to DIN ISO 3016. It lies a few degrees below the recommended lowest operating temperature.