Media-Separated Solenoid Valve - How They Work
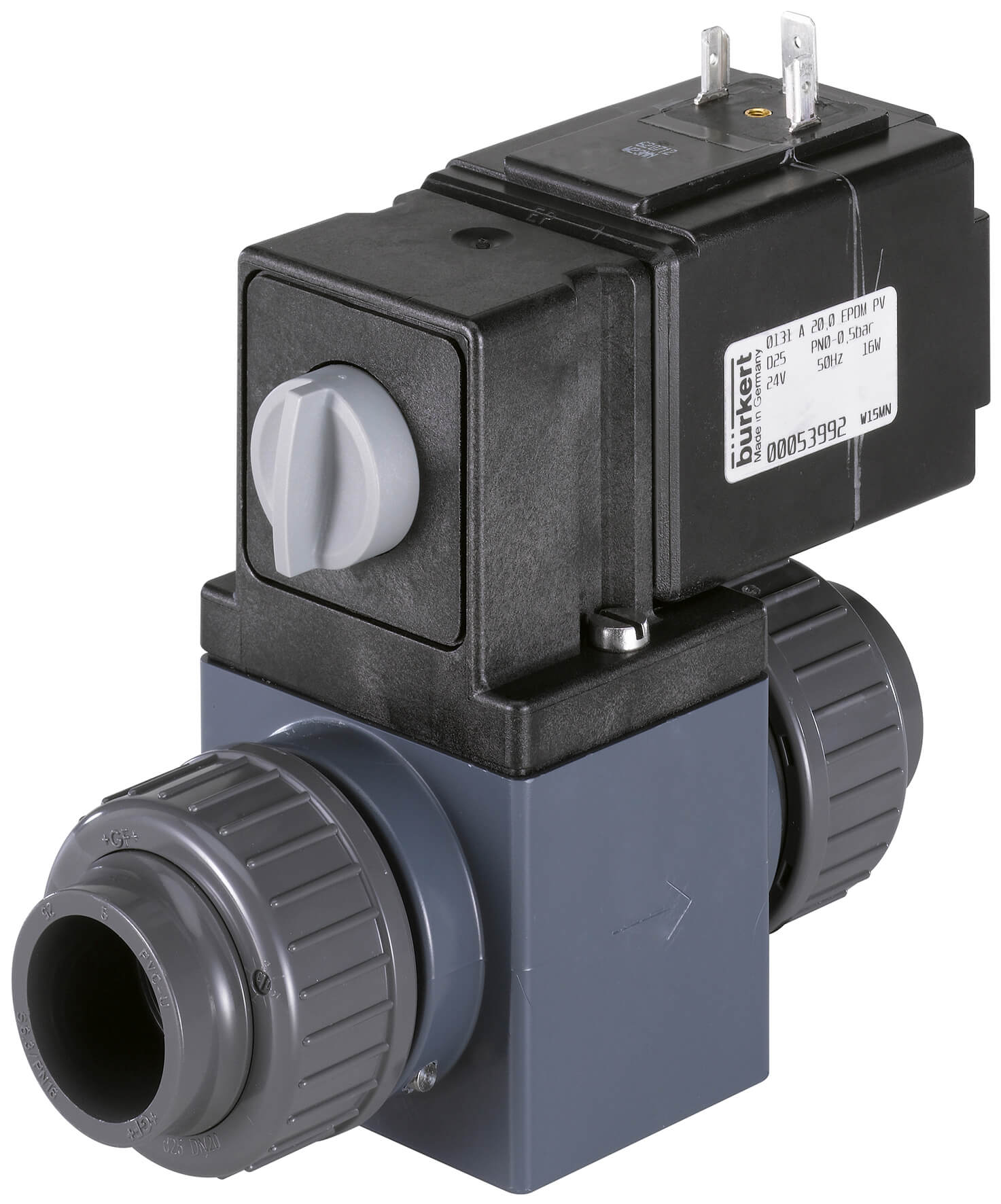
Figure 1: Medium separated solenoid valve
In a media-separated solenoid valve, the fluid is not in contact with the internal mechanical parts, such as the plunger and spring. These valves are particularly suitable for contaminated or corrosive fluids.
Table of contents
View our online selection of solenoid valves!
Risk of corrosion and contamination
In most solenoid valves the ferromagnetic plunger and the return spring are in contact with the media. Valves can be chosen with many different housing materials to be chemically compatible with the media, but the plunger always needs to be ferromagnetic. The most common plunger material is 430F stainless steel, which has a lower chemical resistance in comparison to common housing materials, such as 304 or 316 stainless steel.
Furthermore, due to the mechanism of the actuator in solenoid valves, they are very sensitive to dirt and only work with clean liquids or gases. Valves can allow media in dead spaces where build-up of small particles can interfere with valve motion, bring a risk of cross contamination for a next batch and cause wear on actuating parts. Contaminations in the medium are responsible for the largest share of solenoid valve problems. Care must be taken that valves are installed with their solenoid in a vertical position with the coil facing upwards to prevent accumulation of debris and foreign matter around the plunger. In case the solenoid valve is mounted at an angle, it is recommended to deviate maximally 90° from the vertical position.
Before installation, it is always recommended to shortly flush the pipes to clear them from any particles. If there is a chance of contamination, a filter can be installed upstream of the valve inlet. Routine maintenance can prevent such issues.
However, if media in the system is by nature contaminated, loaded by fine particles, aggressive, corrosive, temperature-sensitive or ultra-pure, it is recommended to use media-separated solenoid valves. Please note that media-separated solenoid valves can handle only slightly contaminated media and are not suitable for all particle-loaded media. For heavy contaminated media or slurries, other valve types are better suited. We’ll explain more about the alternatives later.
Media-separated solenoid valves
Media-separated valves are designed to handle critical media such as aggressive, particle-loaded or high purity liquids or gases. Therefore, it is essential to separate the hydraulic and electrical parts of the valve from the flow path. These types of valves are designed in a way that media is only in contact with valve body, seal and isolation diaphragm. The actuator is located outside the fluid space which protects it from corrosion or accumulation of foreign matter. Consequently, media is protected from contamination and excessive temperature fluctuations. The isolation diaphragm and valve body are made of resistant materials and the valve can be flushed easily due to the reduced dead spaces.
Types
Media-separated solenoid valves exist in many different configurations. In general, the main actuation mechanism falls into two categories: direct operated and indirect operated. The most important criteria to keep in mind while choosing the right valve type is that direct operated valves work from zero bar pressure difference at inlet and outlet, while indirect operated solenoid valves require a minimum pressure difference of around 0.5 bar between the ports. Indirect operated solenoid valves are designed to control larger flow rates using a relatively small solenoid. In the following sections, the operating principle of commonly used media-separated solenoid valves is discussed.
Direct Operated Toggle Solenoid Valve
To explain this example, the Bürkert type 0131 is taken as reference. This toggle valve operates according to the law of lever. A lever pivots at a fixed hinge and can be used to exert a large force over a small distance at one end by exerting only a small force over a greater distance at the other. In a solenoid direct acting toggle valve, the plunger is connected perpendicular to the lever at the upper end (Figure 2) and the sealing cylinder is located on the lower end of the lever. The input force created by the horizontal motion of the plunger is translated through the lever to the sealing cylinder onto the valve seats. This characteristic can therefore directly switch large diameters in a valve.
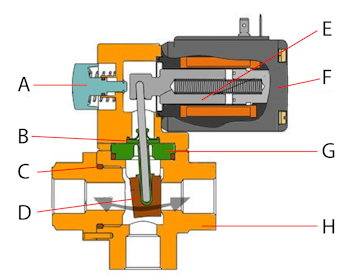
Figure 2: 2/2-way direct-acting solenoid toggle valve: manual override with locking function (A), lateral flange PC (B), o-ring (C), closing body (D), plunger (E), coil (F), PTFE toggle pin (G), brass housing (H)
Since the lever passes through an isolating diaphragm the actuator is separated from the fluid body. Media separation makes this valve especially suitable for use in critical acidic and alkaline solutions or in media that contain particles. Due to the large diameters, this valve is often used as an emptying and mixing valve. This valve can operate as a 2/2-way or 3/2-way.
Direct Operated Pivoted Armature Solenoid Valve
In this type of valve, the plunger is the armature that is pivoted at one point, passes through a flexible isolating diaphragm and enters the valve body on the other side of the diaphragm. When the solenoid is energized, the pivoted armature (the plunger) is pulled in the solenoid and pivots against the force of a return spring. Similar to the toggle valve, the sealing cylinder therefore is pushed against the valve seat (in normally open valves) to stop the flow. Without current, the pivoted armature pivots back by the force of the return spring causing the sealing cylinder to move away from valve seat letting medium to flow.
A 3/2 way direct-acting pivoted armature solenoid valve is shown in figure 3. In the de-energised state the sealing cylinder is forced against valve seat 1 by spring force. In the energised state the solenoid pivots the core armature against the force of the spring and the sealing cylinder is forced against valve seat 2.
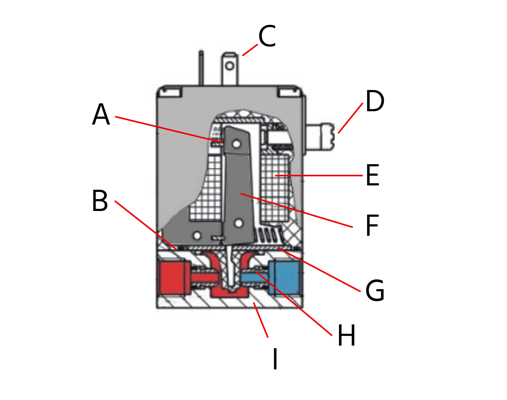
Figure 3: 2/3 direct-acting pivoted armature solenoid valve: return spring (A), valve seat (B), electrical connection (C), manual override (D), coil (E), pivoting armature (F), isolating membrane (G), valve seat 2 (H), and valve body (I)
The use of a separating diaphragm, which separates the media chamber from the electro-magnetic system, makes it possible to use these valves for the control of corrosive, contaminated and aggressive fluids as well as for vacuum.
Indirect Operated (Servo Operated) Solenoid Valves
Opening large orifices using the direct acting method would require enormous and expensive coils. Servo assisted valves use the differential pressure of the medium over the valve ports to open and close. The working principles of a servo assisted solenoid valve is discussed further here.
In a servo assisted valve with pivoted armature pilot control, the pilot valve is a direct acting pivoted armature valve, while the seal of the main valve is a larger flexible diaphragm or a piston.
The main area of application for this valve is the reliable switching of mildly contaminated and aggressive gases and fluids for larger diameters. With this valve type there is very little danger of clogging, since the actuator and media chamber are separated by a diaphragm.
Other Valve Types
Among other media-separated valves, pinch valves, ball valves and butterfly valves are also commonly used for flow control of contaminated or aggressive fluids:
Pinch valves are placed around process tubing and force the tubing together (pinch) to create a seal that shuts off the flow. Pinch valves are commonly used in medical instruments, clinical or chemical analyzers, and a wide range of laboratory equipment. Pinch valves are full bore (full port) valves minimizing loss of pressure when fully open.
Ball Valves use a hollow perforated pivoting ball to control fluid. When the ball’s hole is in line with the flow, the valve is fully open, and when it is pivoted 90 degrees the valve is fully closed. Ball valves are durable, easy to operate and can operate in high pressures and temperatures.
Butterfly Valves use a disk that rotates by a quarter-turn to shift between open and closed states. Butterfly valves usually have lowers costs, and weigh less in comparison to ball valves. However, since the disc is always present within the flow, even when fully open, they always induce a pressure drop in the system.
Selection criteria
The main selection criteria for media-separated solenoid valves after figuring out the required minimum differential pressure at the ports, KV value, and valve orifice, is the choice of material of construction namely body and seal material. All materials of construction have specific properties that make them suitable for different applications. It is essential to choose the appropriate body and seal material for your media.