Solenoid Valve Maintenance
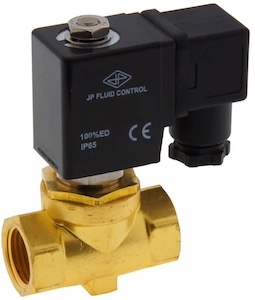
Figure 1: Solenoid valve
Solenoid valves are essential components in many industrial applications; their reliable operation is crucial for maintaining the overall functionality and productivity of the system. Regular maintenance of solenoid valves is necessary to prevent costly breakdowns and ensure optimal performance. This article explores the importance of solenoid valve maintenance, including when to service the valve, how frequently it should be serviced, and whether to repair or replace a valve. We will also provide a step-by-step guide on maintaining solenoid valves.
Table of contents
- Solenoid valve maintenance
- When to service a solenoid valve
- Challenges in controlling common media
- Solenoid valve troubleshooting
- FAQs
View our online selection of solenoid valves!
Solenoid valve maintenance
Solenoid valve maintenance involves replacing any worn-out components and ensuring that the valve parts are clean and free of any debris. Excessive noise, leakage, or sluggish operation indicates that the valve needs to be cleaned and inspected for possible issues. A proper maintenance routine ensures a predictable valve operation and an extended life. Here is a step-by-step guide on maintaining a solenoid valve:
- Disconnect power source: Disconnect the power supply and depressurize the system before performing any maintenance on the solenoid valve. This will prevent any accidental valve actuation during maintenance, which could result in injury.
- Inspect the coil: Inspect the solenoid valve for cracks or burnout. Never power up the coil if it is not installed on the valve stem, as the high current can burn it. Also, moisture penetrating the coil can lead to valve failure. Check the connections to the coil for damage or corrosion.
- Clean the internal parts: Use a wrench to remove the valve stem. This exposes the internal components of the solenoid valve, like the plunger, seal, spring, and o-ring . Wipe dust or debris from the valve body and the internal components using a clean cloth. Clean these components in running water to remove any accumulated dirt. Examine the components for damage and replace them as needed. Read our article on cleaning solenoid valves for more details on the cleaning materials and a step-wise guide on cleaning a solenoid valve.
-
Inspect the internal parts:
- Check for signs of swelling, cracking, or general deterioration on the seal.
- Inspect the spring for broken coils.
- Inspect the interior of the valve for deposits, swelling, or rust that may affect the movement of internal parts or cause leakage.
- Look for any indications of general crest deterioration or scratches near the orifice. Additionally, examine the top part of the plunger and the interior part of the stem for signs of deterioration.
- If the solenoid valve has more complex components such as diaphragms, pistons, or spools, make sure to adhere to the product instructions.
-
Repair or replace:After inspecting the solenoid valve for possible faults, it's time to determine if it's best to repair or replace a few components or replace the entire valve.
- If it's a small part to replace, like an o-ring, it's best to just replace the component and reassemble the valve.
- Often, it is more cost-effective to replace the entire valve unit in basic applications.
- In cases where the valve body has sweat fittings (soldered pipe fittings) or removing it poses a potential hazard, it may be preferable to rebuild (disassemble the valve, replace any worn or damaged parts, and reassemble the valve) the valve's components regularly rather than opting for a complete replacement.
- For solenoid valves catering to high-end applications, replacing the entire valve may pose a higher risk than just replacing the individual parts. The valve may be an integral part of a larger system, and changing the valve's characteristics may impact the system's overall performance. Also, solenoid valves used in high-end applications can be quite expensive, and opting for a complete replacement valve may not always be the most economical choice. In this case, purchasing the replacement kits from the valve manufacturer is a better option.
- Reassemble the solenoid valve: Once the necessary parts have been replaced and any buildup removed, attach the coil again and reinstall the solenoid valve, following the manufacturer's instructions for your particular application.Confirm the parts are correctly installed before switching on the power. Read our article on solenoid valve installation for more information.
- Test the valve: Once the solenoid valve is reassembled, ensure it functions correctly. Apply power to the valve and observe its operation. Check for any leaks, unusual noises, or other signs of malfunction. Read our article on solenoid valve testing for more details.
- Record the maintenance: Record the maintenance performed on the valve, including the date, type of maintenance, and any observations or notes. This information will be useful in tracking the valve's performance over time and planning future maintenance.
When to service a solenoid valve
Determining when to service a solenoid valve requires careful consideration of the risks and costs associated with failure and regular maintenance and servicing costs. In general, the best time to complete solenoid valve maintenance is when the machinery is being taken apart for another service. Consider these points to determine when to service a solenoid valve:
- Risk of hazards during failure: In certain systems, such as those used in the chemical or nuclear industries, solenoid valve failure can result in catastrophic consequences. In such cases, it is crucial to have a rigorous maintenance schedule and to replace the solenoid valves at the slightest malfunctions, even if there are no visible signs of wear and tear.
- Opportunity cost of valve failure: A solenoid valve failure at a critical moment, such as during a production run, results in significant downtime and loss of revenue. In such cases, design a schedule to regularly inspect and maintain the solenoid valve to minimize the risk of failure.
- The financial cost of a valve failure: A solenoid valve failure can result in scrapped work, damaged equipment, and lost productivity. The financial cost of such failures can be significant, especially in industries where downtime and lost production impact revenue. Therefore, it is essential to have a proactive maintenance plan that includes regular inspections and servicing of solenoid valves.
- Cost for service: While regular maintenance and servicing of solenoid valves can help to minimize the risk of failure, it is essential to balance the cost of such maintenance against the potential cost of a failure. In some cases, replacing the solenoid valve at regular intervals may be more cost-effective than investing in regular maintenance and repairs.
Frequency of servicing
The frequency of servicing a solenoid valve depends on its design and application. Some applications can be particularly harmful to the valve's internal and external components, requiring more frequent attention. Components may wear quickly without proper lubrication, resulting in the need to replace them after 100,000 cycles or less. Media that provide lubrication can extend component life up to millions of cycles.
Challenges in controlling common media
Controlling common media like air and water can be challenging for standard solenoid valves.
- Applications involving dry air and rapid cycling can be particularly damaging due to the lack of lubrication and the frequent pounding of internal parts, causing valves to deform and deteriorate.
- Solenoid valves controlling water can have mineral buildup if the water sits idle for extended periods.
- The solenoid valve's small clearances between moving parts can substantially increase the likelihood of premature failure with unfiltered, or viscous media.
Building a maintenance schedule for the solenoid valve's use for the above applications can extend its life and maintain the application's overall functionality consistency.
Solenoid valve troubleshooting
Solenoid valves can experience various issues that can cause them to malfunction, resulting in a loss of control over the fluid they are controlling. Here are some common problems to look out for:
- There is reduced flow output from the valve
- The valve produces a chattering noise when energized
- The valve does not energize when power is applied
- The valve is sluggish or sticks in position
- The solenoid valve does not open
- The presence of internal or external leakage
Read our article on troubleshooting solenoid valves for more details on solenoid valve issues and their solutions, and our solenoid valve overview article to understand the construction, working, and types of solenoid valves.
FAQs
How do I know if my solenoid valve needs maintenance?
If your solenoid valve is not functioning properly, such as if it is slow to open or close or makes strange noises, it may need maintenance. Regular inspections can also help detect potential issues before they become more significant problems.
How often should solenoid valves be maintained?
Solenoid valves should be maintained regularly, typically every 6 to 12 months, depending on the application and the manufacturer's recommendations.