Understanding Torque For Quarter-turn Valves
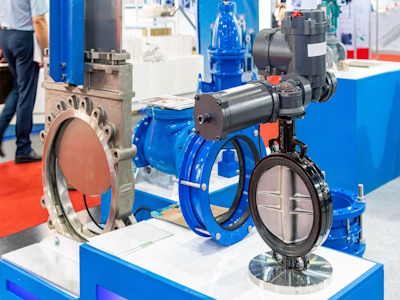
Figure 1: Electric actuator assembly with metal butterfly valve
Torque is the force required to turn a valve stem, turning the valve on or off. Estimating the torque helps determine what kind and size of the actuator is needed for the valve system. This article discusses how to estimate torque for various designs.
Table of contents
- Actuator torque for valves
- Significance of right actuator torque
- Different torque measurements
- Safety margin
- Torque in different valve types
- FAQ
View our online selection of valves!
Actuator torque for valves
Actuator torque refers to the torque an actuator can create. By rotating the valve stem, an actuator converts torque to valve movement (opening, closing, or maintaining movement).
It's important to note that each kind of valve needs a specific amount of torque to open or close fully. The amount of torque an actuator can produce is a key factor in defining its performance capabilities. Based on their torque capacities, different actuators are suitable for various tasks. The actuator torque should be larger than the valve's breaking torque (discussed later).
Significance of right actuator torque
Not having enough turning force for a particular valve can cause serious problems. For example, if an actuator doesn't have enough force to turn the valve's stem, the valve won't open and could get stuck halfway. But if an actuator has too much force, it could damage the valve and the system.
Valve torque characteristics
The torque needed to operate different valves varies based on their application, design, and kind.
- A butterfly valve needs significant turning force to turn it on or off but requires minimal force to throttle the flow. In contrast, a ball valve with a metal seat requires much turning force ( the hard materials used for both the ball and seat create a high-friction, metal-to-metal contact) to turn it on or off and adjust the flow.
- A control valve typically needs more torque than on-off valves with straightforward functions like opening or closing. Control valves require more torque because they operate within varying degrees of flow and pressure, needing to hold position against fluid forces to maintain precise control. On-off valves only cycle between fully open or closed positions without modulating or resisting continuous pressure variations, thus requiring less torque.
Different torque measurements
There are different types of torque:
- Breaking torque: Breaking torque, also known as opening torque, is the torque needed to open a valve from its closed position.
- Running torque: Running torque, or mid-stroke torque, is the torque required to overcome frictional forces while the valve is in motion, maintaining its position at any point between fully open and fully closed.
- Closing torque: Closing torque, also called seating torque, is needed to close a valve fully.
- Maximum allowable stem torque (MAST): MAST, or maximum shaft torque, is the highest torque that can be applied to a valve's components, such as the stem, without causing damage or failure.
The actuator's maximum torque must never exceed the valve's MAST during operation. For applications that use manual actuators, the torque produced by the handle or gearbox is typically not very high, so the concern about exceeding the valve's MAST is less pronounced. Manual quarter-turn valves are often used in applications where power is not available or where a fail-safe mechanism is desired. However, manual valves can also become stuck, requiring more torque to open than can be applied by hand. In this case, the user should extend the 'torque arm' by using a longer handle or a wrench.
Safety margin
When calculating the maximum torque value for a valve, there can be errors, which might lead to accidents within the industry. These accidents can be expensive and cause significant damage. It's recommended to keep a 25% safety margin. For example, if it takes 125 inch-pounds (in-lb) of torque to close a valve, the user should plan as if it requires 150 in-lb of torque to close, thereby upholding a 25% safety margin.
As a general rule of thumb, MAST should be
- 1.2 times the actuator torque for valves used in general services.
- 1.5 times the actuator torque for heavy process duties like blowdown
- 2 times the actuator torque for safety duty applications like shutting down the plant
Torque in different valve types
For all valve styles, manufacturers consider the following factors when calculating torque:
- Valve size and pressure rating: Larger valves and valves designed for higher pressures will generally require more torque.
- Pressure differential: Higher pressure differentials typically require more torque to operate.
- Media properties: The type of media (liquid, gas, slurry), its viscosity, and whether it contains particulates can affect the required torque.
- Temperature: Higher temperatures can change the seat material properties, which affects torque.
- Seat material: Valves with softer seats typically require less torque to operate.
- Period of standstill: Valves that have been in a stationary position for an extended period may require more torque to operate due to increased friction.
- Lubrication: Proper lubrication reduces torque requirements.
Butterfly valve torque
Torque calculations vary among different styles of butterfly valves due to their unique design characteristics.
-
Resilient seated butterfly valves:
- A resilient seated butterfly valve's seat is slightly larger than the disc, and when the valve is closed, the disc compresses the seat. This ensures a tight seal and increases the torque required to operate the valve.
- Over time, the rubber seat may wear or change due to the compression, potentially altering the torque requirements.
-
High-performance butterfly valves:
- High-performance butterfly valves often have a metal seat or a combination of metal and softer materials, which can withstand higher temperatures and pressures than resilient seated valves.
- The torque calculation for these valves must include factors such as the interference between the disc and seat, bearing friction, and the characteristics of the flow media at high pressures or temperatures.
- High-performance valves tend to have consistent torque requirements throughout their lifecycle, as metal seats do not degrade as quickly as rubber.
-
Triple-offset butterfly valves:
- Unlike resilient seat butterfly valves, triple-offset butterfly valves usually have a metal-to-metal seat and seal. This design can withstand higher temperatures and pressures but requires more precision in manufacturing to ensure a tight seal. The torque required to achieve this seal is mostly affected by the precision of the components and the force needed to overcome the initial resistance when the laminated or solid metal seal contacts the seat.
Example
Consider selecting a butterfly valve for a water distribution system. The customer has the following specifications for the system:
- Medium: Water
- Maximum operating pressure: 150 psi (pound-force per square inch)
- Maximum operating temperature: 25°C (77°F)
- Pipe size: 8 inches (DN200)
The customer intends to use an electric actuator to operate the valve and wants to ensure that the selected actuator can provide enough torque to open and close the valve under all operating conditions.
Refer to the valve manufacturer's torque charts or curves to calculate the exact torque requirements. In this example, the torque corresponding to an 8-inch pipe and 150 psi pressure is 1,180 inch-pounds (Table 1). Considering a safety factor of 1.5, choose an actuator that provides a 1,770 inch-pound torque. Some manufacturers also provide the exact safety factor to multiply with the estimated torque for various applications.
Table 1: Butterfly valve torque chart example
Torque values (inch-pounds) |
||||
Size (inches) |
Differential pressure |
|||
125 psi | 150 psi | 200 psi | 250 psi | |
2 | 100 | 106 | 111 | 117 |
2 ½ | 150 | 160 | 176 | 189 |
3 | 200 | 220 | 322 | 244 |
4 | 290 | 320 | 357 | 390 |
5 | 420 | 480 | 540 | 598 |
6 | 600 | 690 | 783 | 875 |
8 | 1,060 | 1,180 | 1,300 | 1,430 |
10 | 1,670 | 1,872 | 2,000 | 2,275 |
12 | 2.568 | 2,790 | 3,000 | 3,250 |
14 | 2,640 | 3,000 | - | - |
16 | 4,260 | 4,880 | - | - |
18 | 6,280 | 7,243 | - | - |
20 | 8,360 | 9,180 | - | - |
24 | 15,427 | 16,813 | - | - |
Ball valve torque calculation
Variations in ball valve designs can lead to significant differences in torque requirements.
- Floating ball valves: In a floating ball valve, the ball is placed by the compression of the two elastomeric seats against it. The ball is free to pivot, hence termed 'floating.' When the valve is closed, the fluid pressure pushes the ball against the seat, creating a seal. The torque requirement for a floating ball valve increases with the fluid pressure because higher pressure pushes the ball harder against the seat, increasing friction.
- Trunnion-mounted ball valves: Trunnion-mounted valves have additional support for the ball, typically with a shaft at the top and bottom. This design reduces the torque required to turn the valve, preventing the ball from pushing against the seats under pressure. Consequently, trunnion-mounted ball valves are often preferred for larger sizes and higher-pressure applications where a floating ball valve would require excessive torque.
- Top-entry ball valves: The torque required to operate a top-entry ball valve is generally relatively low. However, the torque required can increase significantly if the valve is not properly sized, the pressure differential is high, or the valve is not lubricated.
- Full port vs reduced port: Full port ball valves have a bore internal diameter equal to the pipeline's diameter, which minimizes the pressure drop across the valve but can require more torque due to the larger ball surface in contact with the seats. Reduced port valves have a smaller bore and may require less torque.
- Seat material: Soft-seated ball valves, which typically use materials like PTFE, have lower torque requirements due to the lower friction characteristics of the seat material. Metal-seated valves, used in more severe service conditions, require more torque.
Read our hydrogen service valves article for more details on the parameters to consider when selecting a valve for hydrogen service.
FAQ
What is the torque of a control valve?
The torque of a control valve is the measure of force required to rotate the valve's closure member, such as a ball, disc, or plug, to achieve the desired flow control.