Valves For Hydrogen Applications
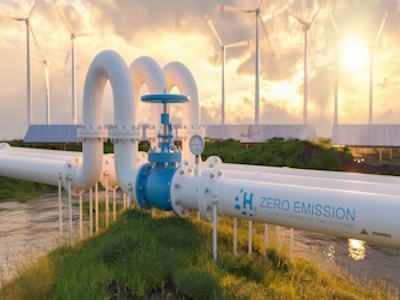
Figure 1: Hydrogen pipeline system
As hydrogen gains momentum as a clean energy carrier, the demand for valves specifically designed for hydrogen applications is growing rapidly. Hydrogen valves must meet stringent safety and performance requirements to ensure the safe and efficient handling of the highly flammable and volatile nature of hydrogen. This article provides an overview of the key considerations when specifying valves for hydrogen applications, encompassing material selection, design features, and testing standards.
Table of contents
- Challenges with hydrogen
- Significance of high performance in hydrogen valves
- Valves for hydrogen service
- FAQs
View our online selection of valves!
Challenges with hydrogen
Hydrogen plays a vital role in environmentally friendly transportation and energy sources. It has several applications, from providing an alternative fuel source for transport to being utilized in fuel cells. Further, when mixed with natural gas in a ratio of 20:80, it produces a power-generating gas that can reduce CO2 emissions by roughly 6-7%.
When choosing and sizing control valves for hydrogen applications, various factors need to be considered.
- Hydrogen has one of the smallest molecular sizes. These tiny molecules can penetrate lower-quality stainless steel, leading to hydrogen embrittlement. Over time, this can cause the material to crack and potentially create significant problems in hydrogen services.
- Given its lightweight nature, hydrogen molecules are small, raising the possibility of leaks in packings and joints and influencing the size of the valve. Ensuring the integrity of hydrogen systems is crucial due to the requirement for complete sealing at every junction. Leakages pose safety risks, particularly during refueling pumps, and result in unnecessary loss when the gas escapes from vehicles or storage facilities.
- Hydrogen's propensity to ignite in the presence of high and low air concentrations is another factor that impacts the selection of valves, particularly packings and joints.
Significance of high performance in hydrogen valves
The conditions for operating hydrogen fuel systems are naturally tough. All hydrogen valves should meet the following requirements.
- Pressures: Hydrogen should be stored in vehicle tanks at 350 - 700 bar (5076 - 10152 psi) to achieve the required density.
- Stress and vibration: The systems must be resilient enough to handle high speeds, rough roads, and harsh weather.
- Safety: Refueling stations should be safe enough to operate.
- Maintenance: The system should allow for easy repairs of tight seals during servicing.
They should show leak-proof performance at the point of connection and their shut-off or control point while handling the operating conditions specific to hydrogen applications.
Material selection
Hydrogen embrittlement (HE) is the degradation of the mechanical properties of a metal caused by the presence of hydrogen. It can result from improper choice of materials and environmental conditions and leads to reduced flexibility in metals due to the absorption of hydrogen atoms.
Most metals are immune to HE at temperatures above 150š©C (302 š©F). The optimal hydrogen pressure for embrittlement is between 20 and 103 bar (300 - 1500 psi). HE happens in steels and similar metals at relatively low hydrogen concentrations. Standards like NACE MR-0175 and NACE MR-0103 define control valve requirements for hydrogen gasses.
- Materials suitable for hydrogen service include aluminum alloys, austenitic stainless steels, copper, and copper alloys. Nickel and most alloys of nickel, as well as ductile, gray, and malleable cast irons, should not be used as they are susceptible to severe hydrogen embrittlement.
- The ISO seal is an advanced mechanical seal engineered to satisfy the stringent needs of hydrogen service. Its structure comprises a sequence of rings constructed from materials such as PTFE or graphite. These are organized in a particular configuration to form a shield that prevents the pressurized hydrogen from interacting with the environment.
- The materials used for diaphragms and sealing in hydrogen applications should be carefully considered, with attention to temperature and pressure conditions. Hydrogen compatibility with polymers is still undergoing extensive field tests.
Fugitive emissions
A fugitive emission is an unintentional leak or discharge of gasses from pressure-containing equipment like valves. Fugitive emission testing refers to tests used to check the external leakage of the valve stem seals and body joints of control valves. These tests mirror actual service conditions, covering all operating temperatures and pressures. Common test standards include ISO-15848-1 and 2, TA-Luft/VDI 2440, ANSI/FCI 91-1, API-622, and ANSI/ISA S93.00.01.
Approximately 60% of escaping emissions are believed to originate from valves, with nearly 80% of the leakage per valve arising from its stem packing. Other contributors to these emissions include exhaust or bleed ports from solenoid valves, positioners, and additional control accessories. Routine inspections and upkeep can help in preventing these emissions.
Valves for hydrogen service
Hydrogen ball valves
Ball valves control the flow of hydrogen gas in hydrogen systems. When choosing ball valves for hydrogen gas applications, it's crucial to pick ones with durable stem seal designs. A good choice may be a trunnion-style ball with a direct-load design, which ensures a secure seal each time the valve's turned on and off. A bottom-loaded stem design can also minimize the chance of stem blowout, enhancing safety. Lastly, ensure they're highly compatible with fittings specifically designed for hydrogen use.
Hydrogen needle valves
Needle valves help make fine adjustments to fluid flow in a system. When using them in hydrogen systems, there are a few important factors to consider.
- Needle valves are usually all-metal and need a lot of force to seal correctly. This force can warp the needle or even the seat, producing a potential risk and leading to expensive maintenance.
- The force usually requires large pneumatic actuators to close and open the valves, which can take up to two minutes to operate fully.
Given these factors, it's crucial to use needle valves made from high-quality 316 stainless steel that can withstand deformation from repeated use. Also, pick a needle valve approved for high working pressures of hydrogen systems (350/700 bar). And, like with ball valves, ensure they are compatible with other hydrogen-approved components.
Hydrogen check valves
Check valves play a crucial safety role in hydrogen compressors used in refueling systems, as they manage excess backflow to safeguard the user. Hydrogen check valves have to deal with a few challenges compared to regular service applications.
Most check valves have springs typically made from material that hardens under strain, making it more prone to hydrogen embrittlement than high-quality 316 stainless steel. Also, refueling applications expose these valves to rapid and significant changes in temperature and pressure, putting extra stress on the valve's rubber seals. Considering these factors, ball check valves are a more fitting choice for hydrogen compressors.
Hydrogen solenoid valves
Solenoid valves control the flow of hydrogen in hydrogen refueling stations, power generation, petrochemical plants, and aerospace industries. Generally, the direct-acting solenoid valves can work from 0 - 1000 bar (0 - 14,503 psi), while the indirect-operated solenoid valves work from 10 - 1000 bar (145 - 14,503 psi). The valve body and other components must be made of materials resistant to hydrogen embrittlement and diffusion. Titanium, stainless steel, and other corrosion-resistant metals are typically used. Also, the polymer constructing the valve must be approved against explosive decompression (the rapid and uncontrolled pressure release in a sealed environment).
Hydrogen safety and pressure relief valves
Pressure relief valves and safety valves are used in hydrogen storage tanks, fuel cell systems, and production facilities to automatically release excess pressure from hydrogen systems when the pressure exceeds a predetermined setpoint. Stainless steel and nickel-based alloys are commonly used in valve construction as these materials resist cracking induced by hydrogen.
Read our article on torque for quarter turn valve for more details on the effect of torque for actuating quarter turn valves.
FAQs
What is a hydrogen gas valve?
A hydrogen gas valve is a specialized type designed to control the flow of hydrogen gas in various applications, like hydrogen fuel cell vehicles and hydrogen production and storage.
What are some of the applications of hydrogen control valves?
Hydrogen control valves are used in various applications, including fuel cell systems, hydrogen production facilities, and hydrogen storage systems.