Rotary Shaft seals – How they work
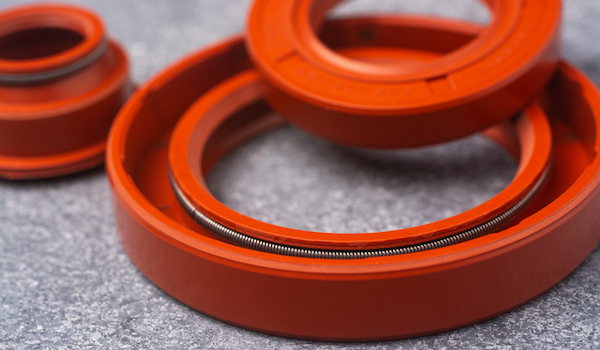
Figure 1: Rotary oil seal.
Rotary shaft seals, also called oil seals or just shaft seals, are used to close and seal the gap between stationary and rotating components. They prevent oil leakage and make sure no contaminants go through the clearance. There are different types of shaft seals for a wide range of applications. This article will give you an overview of shaft seals and assist you in choosing the right one for your application.
View our online selection of rotary shaft seals!
Table of contents
Shaft seal design
In Figure 2 shows the basic design of a shaft seal differs greatly from regular o-rings. It consists of two parts: a metal ring (Figure 2 labeled B) on the inside that provides stability and strength and the second, a sealing lip (Figure 2 labeled E), which creates a seal against the shaft. Depending on the application, the outside covering (Figure 2 labeled A) could be made from rubber or metal. The area in contact with the shaft is kept as small as possible and in most cases is formed into a V-shape (Figure 2 labeled E). This V-shape is especially effective to reduce seal generated heat by reducing lubricant shear and asperity contact. The V-shape is clamped with a garter spring (Figure 2 labeled D) that applies a radial seal against the shaft. Optionally, a dust lip (Figure 2 labeled C) can be added to protect the sealing edge by blocking any dirt or dust from the outside. This has the added benefit of increasing the lifetime of the shaft seal.
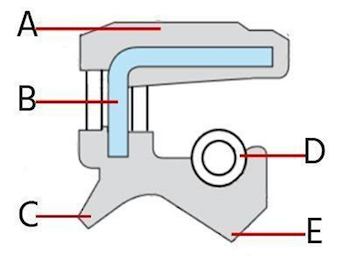
Figure 2: Shaft seal components: Outside covering which seals against the housing (A), metal ring providing stability (B), dust lip (C), the garter spring which clamps the V-shaped radial seal to the axis (D), and the V-shaped radial seal(E)
Shaft seal types
Shaft seals are made according to DIN 3760. The outside of the shaft seal can be made from either rubber or metal. A rubber shaft seal is most commonly used. Their advantage is that they cannot rust, they can seal a slightly damaged housing much better and when operating in high temperatures, the rubber will expand fast ensuring a tight fit. A metal shaft seal is generally more cost-efficient. However, care must be taken that the seal, the housing and shaft have similar thermal expansion properties. Excessive differential thermal expansion can be the cause of leaks when the system experiences temperature changes.
There are three basic types of shaft seals with different construction forms: A, B, and C. If the shaft seal contains a dust lip, an S is added. If it seals from both directions for two different fluids, a 'D' is added. An 'O' in the type means no garter spring. In Figures 3 through 7 the solid black is metal and the plaid pattern is rubber.
Type A/AS
Type A is mainly made from rubber. This ensures no leakage occurs when temperatures change or when the housing hole has a high degree of roughness. Type AS has an additional dust lip to protect the sealing edge from dirt and dust from the outside.
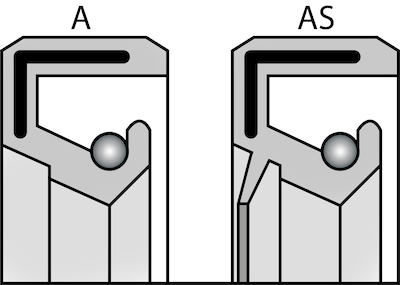
Figure 3: Type A/AS
Type B/BS
Type B has an outside made from metal. To ensure no leakage will occur on the outside, they require narrow tolerances at the housing hole. Type BS has an additional dust lip to protect the sealing edge from dirt and dust from the outside.
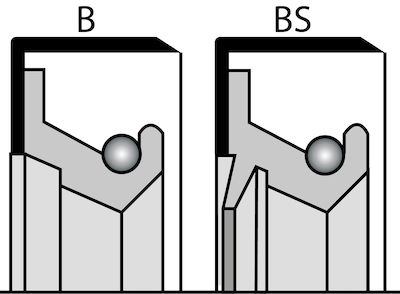
Figure 4: Type B/BS
Type C/CS
Type C is similar to type B, but with an extra reinforcing cap. This makes the shaft seal suitable for harsh operating conditions. It is also more common in shaft seals with a large diameter. Type CS has an additional dust lip to protect the sealing edge from dirt and dust from the outside.
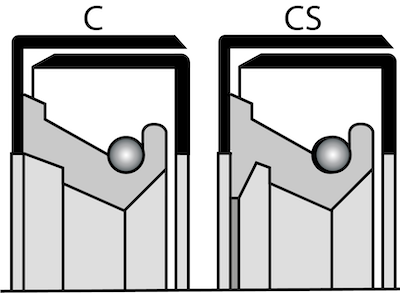
Figure 5: Type C/CS
Type AD/BD
Type AD and BD have two sealing edges, which makes it possible to separate two fluids from each other. Type AD has a metal reinforcing ring, covered by rubber, while type BD has a full metal jacket. Type AD has excellent static sealing on the outer diameter due to a higher press fit allowance and is relatively easy to install. Type BD has a very tight and exact fit in the housing due to the metal press fit.
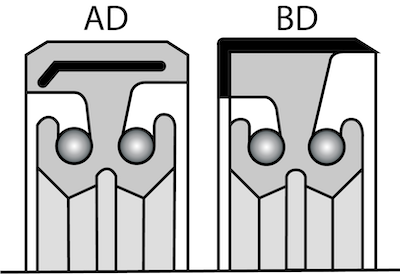
Figure 6: Type AD/BD
Type AO/BO
Type AO and BO are designed without the radial spring that clamps the seal edge onto the shaft. They are therefore mostly used in smaller applications with needle bearings or when the type of lubrication is grease.
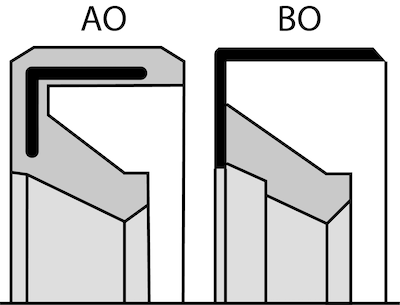
Figure 7: Type AO/BO
Materials
The two most common materials for shaft seals are NBR and FKM. Consult our chemical compatibility chart to ensure chemical compatibility.
- NBR: This material is typically the best choice for general usage. It is resistant to lubricating oil, hydraulic oil, water, and suitable for temperatures between -30°C and 100°C (-22° -212 °F). It is however not resistant to acids and dissolvents. The max running speed (shaft surface speed) of this material is 12m/s.
- FKM: This material is the best choice for applications with high temperatures. It is suitable for temperatures between -20 and 200°C (-4° - 392 °F). It also is a lot better resistant to acids and dissolvents. The max running speed of this material is 38m/s.
A calculation can be made to determine which material suits a system the best by using the below diagram.
Material selection diagram
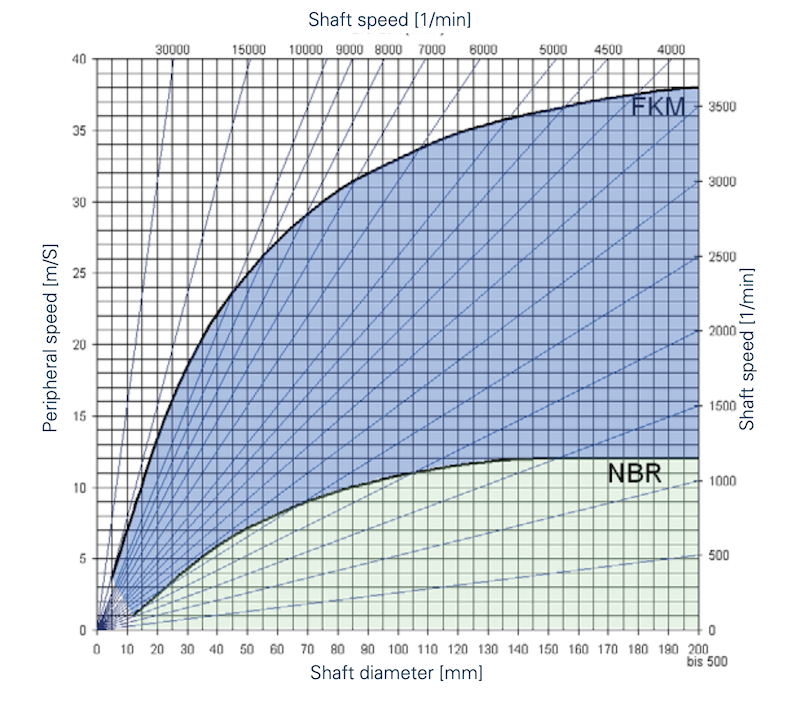
Figure 8: Shaft seal material selection diagram
- With known shaft diameter and rotational speed:
- Determine the point of intersection of the vertical line above the corresponding shaft diameter in [mm] at the base of the diagram with the appropriate diagonal rotational speed line starting from the right or upper edge of the diagram.
- With established shaft diameter and peripheral speed:
- Determine the point of intersection of the vertical line above the corresponding shaft diameter in [mm] at the base of the diagram with the appropriate horizontal line starting from the left edge of the diagram at the corresponding peripheral speed in [m/s].
For example:
- Shaft diameter (d): 100mm
- Rotational speed (n): 1500 1/min
- Peripheral speed (v): unknown m/s
Looking at the graph based on these specifications, we can see that the peripheral speed is 7.9 m/s. It also is in the NBR section of the graph, indicating that this should be the selected material. If the analysis is outside of the NBR or FKM range, a special shaft seal material is required. If it is on the borderline, typically FKM is used as it is of higher quality.
Note: It is still important to look at the chemical compatibility of each material! For more information, read our bearing lubrication article.
Selection criteria
Shaft seals have the following criteria to consider when selecting the right one for your application:
- Dimensions
- Ensure the shaft seal properly seals against the shaft and housing to fill the entire gap between the stationary and rotating components.
- Lubrication
- The choice for a specific type of seal depends for a large part on the type of media used for lubrication.
- If grease is the only medium in the system a type AO or BO shaft seal made from NBR will be sufficient.
- If acids or dissolvents are used a shaft seal made of Type A/AS, AD/BD, B/BS, C/CS is recommended made from FKM.
- Working temperature
- Type A seals should be used for applications that have frequent temperature changes as it can expand/contract with the change in temperature.
- If the temperature of the application is above 100°C (212°F) then FKM should be used.
- If the temperature ranges between -20° to -30°C (-4 to -22°F) NBR should be used. Between these ranges, it depends on the media type.
- Operating load
- If the shaft is exposed to a lot of irregular forces like in an off-road truck, a type C shaft seal is recommended. If the running speed of the axle exceeds 14m/s you should get a shaft seal made of FKM. Use our material selection diagram.
- Environment
- If there is a lot of dirt or dust in the environment, it is recommended to select a shaft seal that has a dust lip. This will increase the lifetime of the shaft seal.