Air Pressure Gauge - How It Works
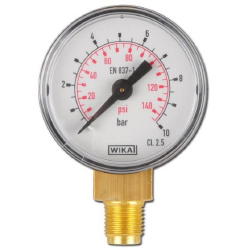
Figure 1: An air pressure gauge with steel/brass housing
Air pressure gauges measure the pressure of air in a pneumatic system. The measurement of air pressure is essential for the proper functioning of many systems and can be used to monitor and control the performance of compressors, pneumatic systems, and other equipment that utilizes air. They are applicable in a wide range of industries, including automotive, aerospace, and manufacturing.
Table of contents
- Gauge pressure
- Types of air pressure gauges
- Principle of operation
- Air pressure gauge applications
- Selection criteria
View our online selection of pressure gauges!
Gauge pressure
Typically, an air pressure gauge measures gauge pressure. Gauge pressure is a liquid or gas's pressure relative to the local atmospheric pressure. Negative gauge pressure is also called vacuum pressure. Measuring gauge pressure is important because it helps to monitor and control the pressure of a system, which can improve safety, efficiency, and performance. To learn more about pressure types, read our article on the different types of pressure measurements.
Types of air pressure gauges
There is a variety of pressure gauges used in pneumatic systems. The following are typical examples:
Digital air pressure gauge
A digital air pressure gauge (Figure 2) uses an electronic sensor to measure the pressure. It displays the reading on an electronic display. These gauges require batteries or an external power source and provide a more accurate and reliable pressure reading than mechanical gauges. Additionally, digital pressure gauges can connect to PLCs (programmable logic controllers), SCADA (supervisory control and data acquisition) systems, or other control systems, allowing for automated pressure control in the pneumatic system as well as data logging. They are commonly used for pneumatic industrial processes, for example, a filling and packaging line in a beverage manufacturing facility. Digital pressure gauges make it easy for operators to identify and address pressure fluctuations, which can help prevent equipment damage, improve safety, and optimize performance.
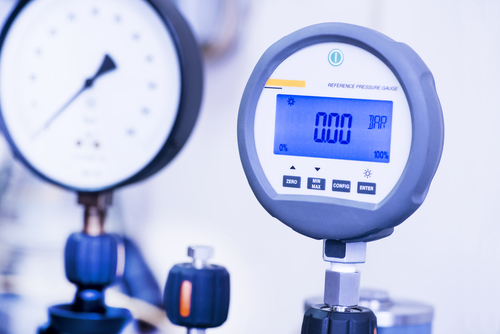
Figure 2: A digital pressure gauge
Air compressor pressure gauge
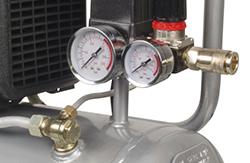
Figure 3: An air pressure gauge on an air compressor.
An air compressor pressure gauge is designed specifically for use with air compressors. It is typically used to measure the pressure of the air in the compressor's tank and the pressure of the air being released from the compressor. Air compressor pressure gauges are often built with durable materials. They are designed to withstand air compressor systems' high pressure and vibration.
Dual needle air pressure gauge
A dual needle air pressure gauge features two needles that move independently of each other. One needle indicates the current pressure, while the other indicates the maximum or minimum pressure reached. This gauge type is commonly used in industrial applications where the pressure can fluctuate rapidly, a common example being pneumatic cylinders. Pneumatic cylinders are used in various industrial applications, such as robotics and automation, packaging, and material handling.
Inline air pressure gauge
An inline air pressure gauge is installed directly in the airline, allowing for continuous pressure monitoring. This type of gauge is beneficial in systems where it is not practical to install a gauge at the source of the pressure, such as in long airlines. Inline air pressure gauges are also helpful for monitoring the compressed air pressure in a pneumatic system. They are typically small and easy to install, making them a popular choice for many applications.
Principle of operation
When measuring air pressure, there are different gauges to choose from. Each type has its strengths and weaknesses. These pros and cons are the measurable pressure range, sensitivity, response time, and interaction between the media and the gauge's internal parts.
Bourdon tube pressure gauge
A bourdon tube pressure gauge uses a flexible metal tube that connects to the measured system. As the pressure in the system increases, the bourdon tube straightens out, which moves a pointer on the gauge face to indicate the pressure level. The metal construction of the bourdon tube makes it resistant to vibration and shock, ensuring accurate pressure measurement in harsh pneumatic applications (e.g., construction and mining equipment). For applications with exceptional vibrations and shock, see liquid-filled pressure gauges.
Diaphragm pressure gauge
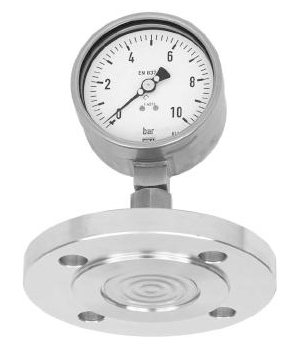
Figure 4: A diaphragm pressure gauge
A diaphragm pressure gauge works by using a flexible diaphragm, the only part of the gauge that makes contact with the measured system. As the pressure in the system increases, the diaphragm pushes against a spring, which moves a pointer on the gauge face to indicate the pressure level. The flexibility of the diaphragm allows for very accurate measurement of pressure, even for small changes in pressure. This accuracy is necessary for pneumatic applications that require precise pressure control—for example, laboratory equipment such as mass spectrometers and gas chromatographs.
Bellows air pressure gauge
Bellows gauges work by using a metal bellows that expands as the pressure in the system increases. The expanding bellows moves a pointer on the gauge face to indicate the pressure level. The metal bellows construction precisely measures even small pressure changes. Also, it allows for a fast response time to pressure changes.
Bellows gauges excel over other gauges in aerospace and defense pneumatic systems. The flight and operation of aerospace and defense vehicles, such as helicopters and fighter jets, expose pressure gauges to high vibration and shock. Bellows gauges can withstand this shock while providing fast and accurate pressure change measurements, which is critical in these industries.
Air pressure gauge applications
Several applications for air pressure gauges have been discussed throughout this article already. The following are a summary and expansion of those applications:
- Air compressors: Air compressors operate at very high pressures and require careful pressure control to prevent damage and danger.
- Pneumatic cylinders: Pneumatic cylinders are applicable in many different industries. While operating, pressure in the cylinders fluctuates rapidly. Dual needle air pressure gauges allow operators to closely monitor the current and peak pressures.
- Heavy machinery: Pneumatic systems in heavy machinery use air pressure gauges to ensure safe and efficient operation.
- Laboratory and sanitary: Laboratory applications or applications that demand a high degree of sanitation use hygienic pressure gauges to ensure pressure measurements without dangerous mixing of media.
- Aerospace: The aerospace industry uses pneumatic pressure gauges for applications such as pressurizing the cabin and fuel tanks.
Selection criteria
There are many factors to consider when selecting an air pressure gauge, including the application, pressure range, connection, and temperature. Read our guide on selection tips for pressure gauges to learn more.