Industrial Hose Types and Selection Criteria
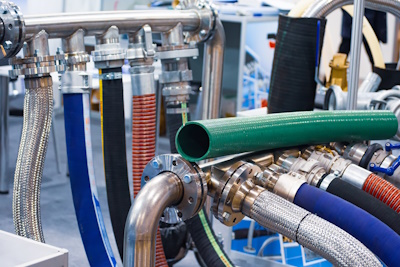
Figure 1: Different types of hoses in an industry
Industrial hoses transfer materials such as air, water, chemicals, and petroleum products in industries. These hoses are designed to withstand extreme temperatures, high pressure, and harsh chemicals, ensuring durability and reliability in demanding environments. The performance of an industrial hose is largely determined by its material composition; for instance, rubber hoses offer flexibility and durability, while metal hoses excel in high-temperature and high-pressure applications. This article discusses the main types of industrial hoses and their typical selection criteria.
Table of contents
- Selection criteria
- Chemical hoses
- Water and liquid hoses
- Air and gas hoses
- Lay flat hoses
- Milk and dairy hoses
- FAQs
Selection criteria
When selecting industrial hoses, consider the following crucial parameters:
- Internal and outer diameter: The internal diameter determines the flow capacity, while the outer diameter affects compatibility with fittings and space constraints. Choose a diameter that matches the required flow rate and fits the available space and connections.
-
Hose material: Select a material compatible with the substances being transported and the environmental conditions, such as:
- PVC for general use
- Polyurethane (PUR) for abrasion resistance
- Teflon (PTFE) for chemical and heat resistance
- EPDM for weather and steam resistance
- NBR (Nitrile Rubber) for oil and fuel resistance
- Pressure and temperature range: Ensure the hose can handle the maximum operating pressure and temperature of the application. This prevents failures and ensures safety.
- Bending radius: The bending radius indicates how flexible the hose is without kinking. Choose a hose with a bending radius that suits the installation layout, especially in tight spaces, to maintain flow and prevent damage.
- Bursting pressure: Bursting pressure is the maximum pressure the hose can withstand before failing. The safety factor for a hose's bursting pressure varies based on the type of hose and its application, as seen in Table 1.
- Number of inlays: Inlays provide reinforcement, improving the hose's strength and flexibility. More inlays generally mean higher pressure resistance. Less inlays are suitable for low-pressure applications where flexibility and ease of handling are crucial.
-
Approvals and standards: Adhering to industry standards and approvals is crucial for ensuring safety, quality, and market acceptance.
- Regulation (EC) No. 1935/2004: Ensures food-contact materials in the EU are safe and do not alter food.
- Regulation (EU) No. 10/2011: Sets rules for safe use of plastic food-contact materials in the EU.
- FDA 21 CFR 175.300: Regulates safe resinous and polymeric coatings for food-contact surfaces in the U.S.
Table 1: Common safety factors for different types of hoses in various applications.
Application | Common safety factor |
Hydraulic applications | 4:1 |
Air and multipurpose hoses | 4:1 |
Petroleum and chemical hoses | 4:1 |
Water hoses | 3:1 or lower |
Steam hoses | 10:1 |
Chemical hoses
Chemical hoses and tubes transport various chemicals to and from different processing points within a system. These hoses are suitable for acids, alkalis, hydrocarbons, and industrial solvents, among others.
Chemical hoses are typically manufactured from rubbers and plastics such as EPDM, EPM and PTFE. Depending on the application the hoses can have an inlay made of a high tensile-strength material like steel or textile. The main features of these chemical hoses are:
- UV, ozone, and ageing resistance
- Very large temperature range (-196 to 260 𐩑C, or -321 to 500 𐩑F)
- Excellent chemical resistance
The chemical hoses can release toxic fumes when overheated. Always ensure it operates within its specified temperature range and use it in well-ventilated areas to disperse any potential fumes. Also, the workers wear appropriate masks or respirators to protect against inhalation of harmful substances.
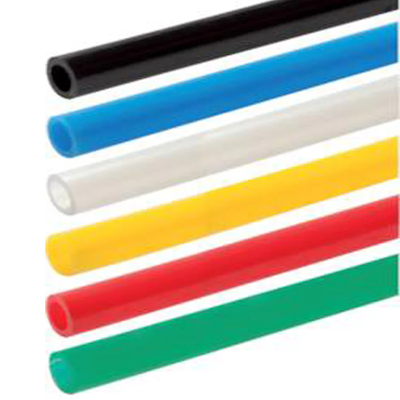
Figure 2: Chemical resistant hose made of PTFE
Water and liquid hoses
Universal water and liquid hoses
Industrial water hoses transport liquids between processing points within a system. These hoses are suitable for drinking water, food-grade liquids, and industrial applications. They are typically made from materials such as polyurethane, polyethylene, NBR rubber, PVC, and EPDM. Depending on the application, some hoses feature inlays made from high tensile-strength materials like steel or textile fibers for enhanced durability. The main features are:
- High flexibility due to polyether-polyurethane material.
- Hydrolysis and microbe resistant
- Suitable for drinking water and food-grade products
- Works at a high temperature range of -35 𐩑C to 60 𐩑C (-31 °F to 140 °F)
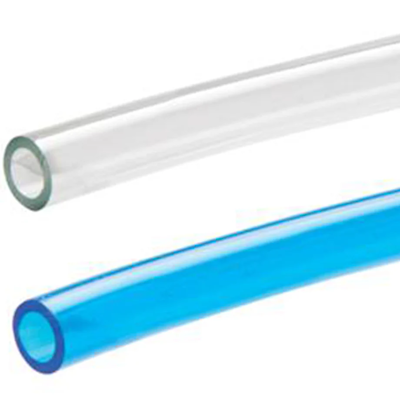
Figure 3: Polyurethane food grade/drinking water hose
Steam hoses
Steam hoses transport steam to and from various processing points within a system. There are hoses suitable for high and low-pressure steam, and oil-protected applications. These hoses are made from synthetic EPDM rubber and may include inlays of high tensile-strength materials such as steel or copper, depending on the application requirements. The main features are:
- EPDM hose material makes it resistant to acids and alkalis and suitable for hot water and saturated steam.
- Suitable for both water and steam due to the high temperature range (-40 to 164 𐩑C)
- The outer EPDM layer is perforated to ensure no cover bubbles or blisters form.
- The steam hoses are only suitable for low-pressure steam applications but is versatile due to the high temperature range
Note: Steam exists in different states, wet saturated steam, dry saturated steam and superheated steam, depending on the operating pressure and temperature. Superheated steam can damage steam hoses. Read our steam hoses article for the various types of steam hoses and their selection criteria.
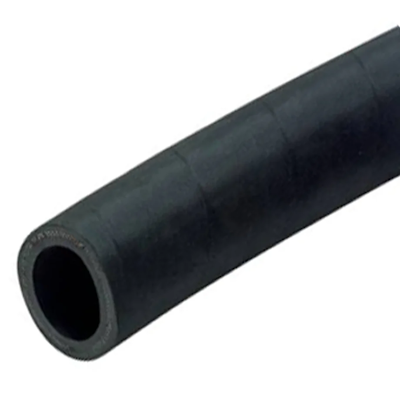
Figure 4: EPDM steam hose
Garden hoses
Garden hoses are used for irrigation in both professional and consumer settings. These flexible hoses direct water from a tap to the desired location, such as for watering plants, filling ponds, or washing cars. Typically made from flexible PVC, the garden hoses are reinforced with materials like metal or plastic between the inner and outer layers. This reinforcement makes the hoses pressure-resistant, more durable, and less prone to kinking. The high-quality construction of these hoses makes them suitable for intensive use in gardens and professional environments, such as sports fields or garden centers. The main features are:
- Pressure-resistant, wear-resistant, and kink-resistant, ideal for heavy-duty use.
- The PVC-free inner layer protects water quality, crucial for sensitive applications like nurseries.
- Offers excellent handling and can withstand a wide temperature range, making it versatile for various climates.
- Capable of handling high pressure, suitable for demanding tasks in professional and leisure settings.
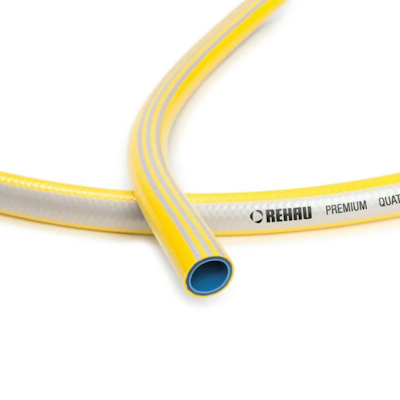
Figure 5: Garden hose
Air and gas hoses
Air and gas hoses are suitable for compressed air, propane, breathing air, and combustible gas applications are designed to transport various gasses to and from different processing points within a system. These hoses are typically made from materials such as polyurethane, polyethylene, NBR rubber, PTFE, PVC, and EPDM. They must be non-porous to ensure leak-free operation. Read our air and gas hose article for more information on their features, materials, and applications.
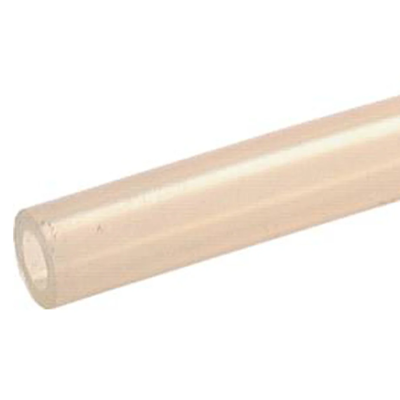
Figure 6: Low pressure silicon gas hose
Lay flat hoses
Lay flat hoses are designed to be flat when not in use, making them easy to store and transport. They are commonly used in applications such as irrigation, water discharge, and firefighting. These hoses are typically made from materials like polyester or NBR. Read our lay flat hoses article for more information.
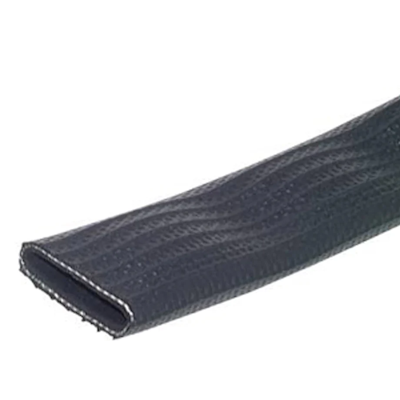
Figure 7: Lay flat hose
Milk and dairy hoses
Milk and dairy hoses are essential components in modern dairy farms and the dairy industry, used for milking machinery and transporting milk and dairy products. These hoses are designed to meet FDA and EU standards to ensure sanitation, maintain milk quality, and prevent chemical contamination. Typically made from materials like NBR, these hoses are reinforced for durability and are resistant to oils and fats, making them suitable for various dairy applications. Read our milk and dairy hose article for more information.
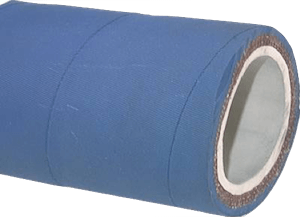
Figure 8: Milk and dairy hose
FAQs
What materials are industrial rubber hoses made from?
They are typically made from natural or synthetic rubbers like EPDM, NBR, or SBR for flexibility and durability.
What is the purpose of industrial hose fittings?
Industrial hose fittings connect hoses to equipment, ensuring a secure and leak-free transfer of materials.
What is the difference between a garden hose and a regular hose?
A garden hose has a larger diameter, allowing for increased water pressure, and is constructed with thicker, more durable materials.