What Is a Lift Check Valve
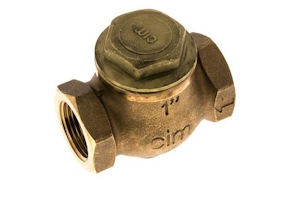
Figure 1: A lift check valve
Lift check valves allow one-way fluid flow by opening during normal flow conditions and closing under low-flow or backflow conditions. Lift check valves must be installed horizontally, since gravity assists in closing the valve. They are critical components in many industrial piping systems, designed to ensure unidirectional fluid flow and prevent backflow. Lift check valves are used in systems across various industries, including water supply, chemical processing, and power generation.
Table of contents
- Components of lift check valves
- How lift check valves work
- Comparisons with other check valve types
- Lift check valve advantages and disadvantages
- Lift check valve applications
- Symbol
- Selection criteria
- FAQs
Components of lift check valves
Lift check valves the following key parts: the body, disc, and seat.
- Body: The body (Figure 2 labeled A) houses the internal components and provides structural integrity.
- Materials: Gunmetal, also known as red brass, is a common material for a lift check valve's body. It is an alloy of copper, tin, and zinc. Typically 88% copper, 8-10% tin, and 2-4% zinc. Gunmetal is corrosion and dezincification resistant.
- Disc: The disc (Figure 2 labeled B), which is often a plug or ball design, is the moving part that lifts to allow fluid flow and prevent backflow.
- Seat: The seat (Figure 2 labeled C) is the sealing surface for the disc when closed.
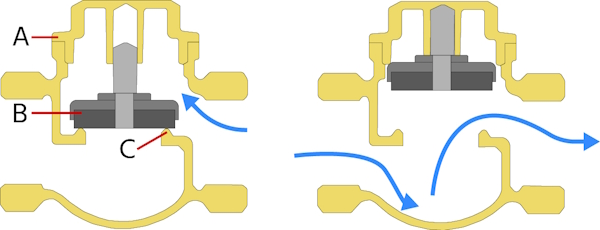
Figure 2: Lift check valve design and function. Key components are body (A), disc (B), and seat (C). Upon backflow (left), the disc closes. During normal flow (right), the disc opens.
How lift check valves work
Lift check valves operate based on pressure differences within the system. When the upstream pressure exceeds the downstream pressure (Figure 2 right), the disc lifts, allowing fluid to pass through. If the pressure drops or reverses (Figure 2 left), the disc falls back into the seat, effectively blocking any reverse flow. This automatic operation is essential for preventing contamination and protecting equipment from potential damage.
Comparisons with other check valve types
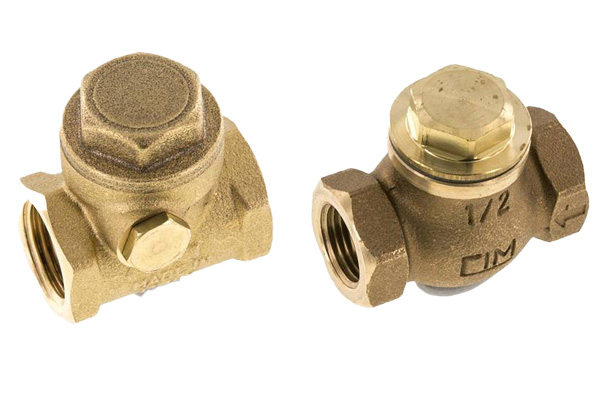
Figure 3: At first inspection, swing and lift check valves can appear similar. Lift check valves, though, typically have rounder bodies similar to globe check valves.
Lift check valves have their advantages but are not suitable for every application. It's useful to compare them with other check valve types in order to choose the best type of check valve for an application. See Table 1 for a comparison with swing check valves and spring-loaded check valves.
Table 1: Lift check valve vs swing check valve vs spring-loaded check valve
Feature/Criteria | Lift check valves | Swing check valves | Spring-loaded check valves |
---|---|---|---|
Operation | Disc lifted by fluid flow, closes by gravity or back pressure | Hinged disc swings open with flow, closes when flow reverses | Spring mechanism compresses to open, expands to close |
Advantages | Good sealing for high-pressure applications | Low pressure drop Suitable for fluids with suspended solids |
Fast response to flow changes Can be installed in any orientation |
Limitations | Lift check valve pressure drop is higher due to disc lifting Limited to horizontal installation Sensitive to debris, which can obstruct disc movement |
Generally limited to horizontal installation Slower response, allowing potential backflow before sealing |
Higher cost due to spring mechanism Potential for spring wear in high-cycling applications |
Ideal applications | Clean fluid systems with consistent flow | Water and wastewater systems with large volumes and suspended solids | Systems requiring quick response and versatile installation |
Installation flexibility | Limited (horizontal only) | Limited (primarily horizontal) | High (any orientation) |
Cost | Moderate | Low | Higher |
Maintenance | Low to moderate, depending on debris exposure | Low | Moderate to high, due to potential spring wear |
Lift check valve advantages and disadvantages
Lift check valves offer several advantages, including durability, reliability, and low maintenance requirements. They are well-suited for high-pressure and high-temperature applications. However, they can be prone to water hammer effects, which can be mitigated by installing dampeners or adjusting system pressure. Also, debris in the fluid must be filtered in order to prevent getting stuck in the seat and stopping the valve from opening. Finally, do its flow path, pressure drop across a lift check valve is significantly greater than across other check valve types.
Lift check valve applications
Lift check valves are used in a wide range of industries:
- Water supply systems: Used in municipal water supply systems to prevent backflow and maintain pressure.
- Pumping stations: Installed at the discharge side of pumps to prevent reverse flow when the pump is turned off.
- Boiler systems: Used in steam and hot water boiler systems to prevent backflow of steam or hot water.
- Oil and gas industry: Employed in pipelines to prevent backflow of oil, gas, or other fluids.
- Chemical processing: Used in chemical plants to ensure the correct flow direction of chemicals and prevent contamination.
- HVAC systems: Installed in heating, ventilation, and air conditioning systems to ensure proper flow of refrigerants and other fluids.
- Fire protection systems: Used in fire sprinkler systems to prevent water from flowing back into the main supply.
- Irrigation systems: Used in agricultural irrigation systems to prevent backflow and contamination of water sources.
- Marine applications: Used in shipboard systems to prevent backflow in bilge and ballast systems.
- Power plants: Used in cooling water systems and other applications to ensure proper flow direction and prevent backflow.
Symbol
Lift check valve symbols can vary. However, the key characteristic of the symbol is that it looks similar to a typical check valve symbol with the addition of a solid circle in the top left corner of the symbol. Figure 4 shows two examples of lift check valve symbols.
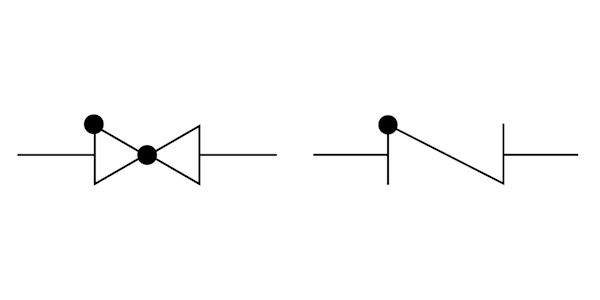
Figure 4: Two examples of lift check valve symbols. The key characteristic is the solid circle in the top left corner of the symbol.
Selection criteria
When selecting a lift check valve, several factors should be considered.
- Connection size: Sizes range from 1/2" to 4 inches
- Connection type: BSPP-G internal threads are common. Ensure the valve's connection type will match the part of the application it will connect to.
- Material (housing and seal): Red brass, in other words gunmetal, is a common housing material due to its corrosion resistance. Teflon (PTFE) is similarly resistant. Ensure the valve's materials will be suitable for the application.
- Max pressure: Ensure the valve can handle the application's max operating pressure to prevent damage. 16 bar and 20 bar are common max pressure capabilities.
- Temperature range: The valve's material, specifically its seal material, controls the temperature range. For example, gunmetal housing and a Teflon seal can handle between -10 °C and 100 °C.
- Kv value: The Kv value (or Cv value) expresses the valve's flow rate. Select a valve that has a flow rate similar to the application to prevent undersizing or oversizing the valve.
- Minimum opening pressure: Ensure the application's pressure will easily open the valve based on its minimum opening pressure, or cracking pressure. If the pressure is too low, the valve will chatter, causing premature wear.
FAQs
What is a lift check valve?
A lift check valve allows one-way fluid flow by opening during normal flow and closing under low-flow or backflow conditions.
What are the advantages and disadvantages of a lift check valve?
Advantages include simple design and reliability; disadvantages include higher pressure drop and need for horizontal installation.
What is the difference between a lift check valve and a swing check valve?
A lift check valve uses a piston to block flow, while a swing check valve uses a hinged disc, resulting in different flow characteristics and pressure drops.