Spring Loaded Check Valves Overview
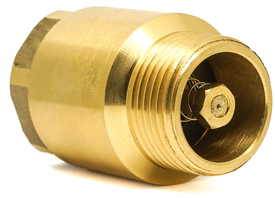
Figure 1: Spring check valve
Spring-loaded check valves prevent backflow and ensure unidirectional flow. These valves are characterized by their simple yet effective mechanism and versatility, and they can be installed in any orientation. They are available with various end connections to suit different applications. They are commonly used in HVAC systems, sprinkler systems, and sump pumps, where preventing backflow is critical. Despite their higher cost compared to other check valves, their reliability and noise control capabilities make them a preferred choice in many low-risk applications.
Table of contents
- Spring loaded check valve components
- How does a spring loaded check valve work?
- Installation guidelines
- Materials
- Selection criteria
- Advantages and disadvantages
- Applications
- FAQs
View our online selection of check valves!
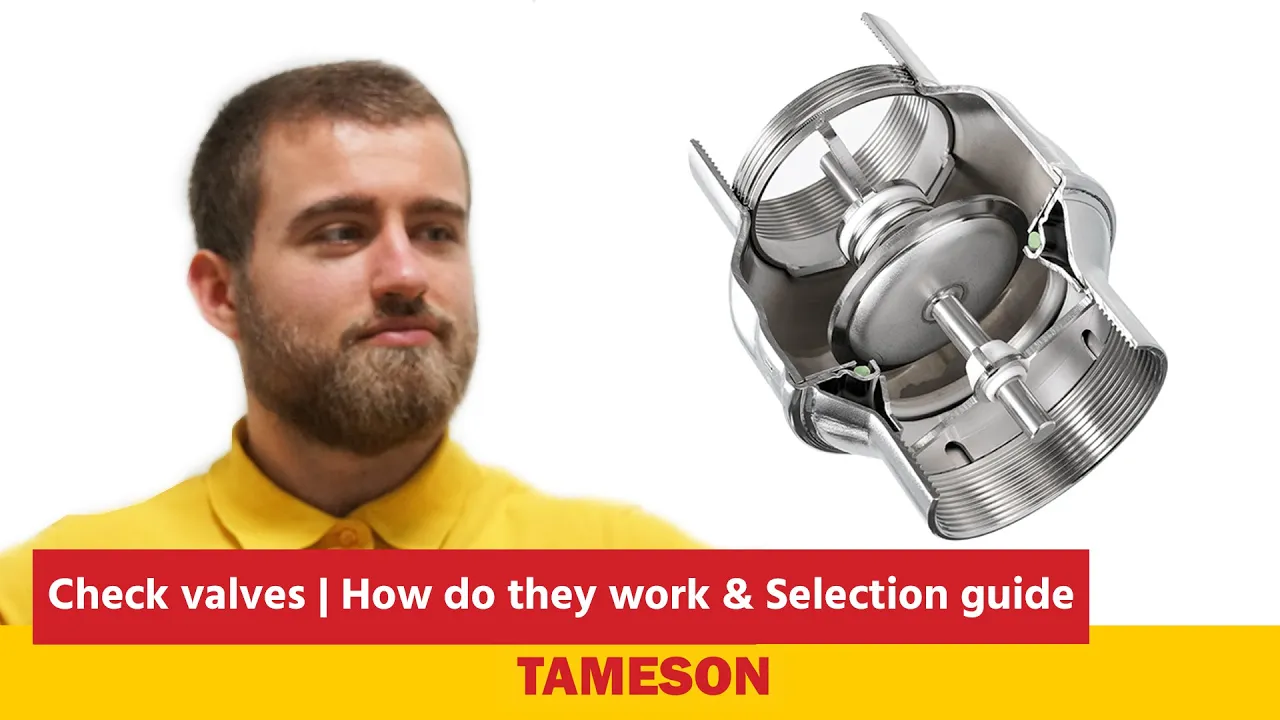
Spring loaded check valve components
A spring check valve's housing (Figure 2 labeled A) protects the inner components from the environment. The disc (Figure 2 labeled B) opens and closes to allow or prevent flow through the valve. The spring (Figure 3 labeled C) controls the valve's cracking pressure and closes it. Finally, the guide (Figure 2 labeled D) keeps the disc properly aligned to ensure a complete seal when it is closed.
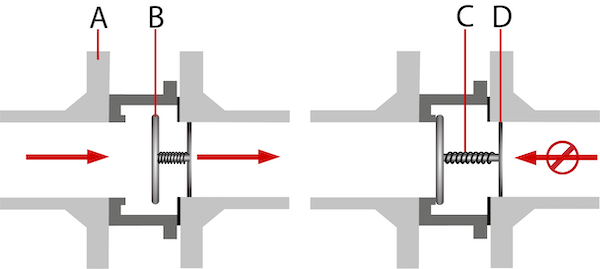
Figure 2: Spring check valve components: body (A), disc (B), spring (C), and guide (D). When media flows in the valve's flow direction (left), the flow pressure opens the valve. When the pressure drops significantly enough, or there is backflow (right), the spring closes the valve.
How does a spring loaded check valve work?
A spring-loaded check valve's function is straightforward. The fluid pushes against a disc or poppet inside the valve in normal flow conditions. This force overcomes the tension of the spring, causing the valve to open and allowing the fluid to pass through. The spring is calibrated to provide just enough force to close the valve when the flow stops, but not so much that it prevents the valve from opening under normal flow conditions. The tension of the spring can often be adjusted to suit different applications.
The minimum pressure required to overcome the spring force and open the valve is known as the cracking pressure, which is a critical parameter in valve design and application. When the fluid flow stops or attempts to reverse, the spring pushes the disc or poppet back into its seat, closing the valve and preventing any backflow of fluid.
Pressure drop
A spring-loaded check valve's pressure drop is the pressure reduction as fluid passes through it. A lower drop means less flow resistance, making the system more efficient. In a spring-loaded check valve, a larger valve size reduces pressure drop by providing a bigger passage for fluid, which decreases flow resistance, while a lower flow rate reduces pressure drop by decreasing fluid velocity and resistance. Conversely, higher spring tension increases pressure drop by requiring more pressure to open the valve.
Spring check valve symbol
As seen in Figure 3, the spring-loaded check valve's symbol has a horizontal Y that opens towards the flow direction. Opposite the horizontal Y is a horizontal line with a zigzag line passing through it. This zigzag line represents the spring and the circle represents that the check valve is spring-assisted.
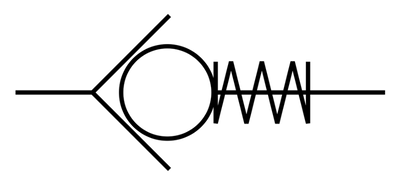
Figure 3: Spring check valve P&ID symbol
Installation guidelines
Consider the valve's orientation and end connections when installing a spring-assisted check valve. Firstly, the valve must be installed in the correct direction so media can flow through it. Typically, an arrow is stamped on the valve body to display the valve's flow direction.
A primary advantage of spring check valves is that they can be installed in any orientation. This means that the spring check valve vertical installation is possible, whether the flow direction faces downwards or upwards, because the spring can hold the valve closed against the force of gravity.
End connection types
Specific applications require certain end connections. Spring check valves are highly versatile and have many different types of end connections (See Table 1).
Table 1: End connections and their installation guidelines
End connection | Description | Installation guidelines | Factors affecting installation |
---|---|---|---|
Threaded connections | Versatile with inner (NPT, BSP, BSPP-G, BSPT-Rp, metric) and outer threads | Suitable for low (brass) and high-pressure (stainless steel) applications | Material choice based on pressure; thread type compatibility |
Flanged connections | Use gaskets between valve and pipe flanges; ideal for large valves | Easy disassembly for maintenance; excellent sealing | Gasket quality; flange alignment and bolt torque |
Compression ring | Leak-proof seal without welding; medium-pressure applications | Allows easy disassembly and reassembly | Proper alignment and tightening; material compatibility |
Glued sleeve connections | Permanent, leak-proof seal; used in low-pressure plastic systems | Ensure proper curing time for glue; permanent installation | Glue type and curing conditions; material compatibility |
Hose pillar connections | For flexible hose attachments; low to medium-pressure | Suitable for systems requiring frequent disconnection | Hose material and size; pressure rating |
Push-in connections | Quick installation without tools; low-pressure applications | Common in pneumatic systems; ensure proper fit | Tube size and material; pressure rating |
Cutting ring connections | Reliable seal for high-pressure applications; used in hydraulics | Ensure proper cutting ring installation for leak-proof connection | Proper assembly technique; pressure rating and material compatibility |
Victaulic connections | Grooved coupling system for quick assembly/disassembly. | Suitable for various materials; used in fire protection, industrial, and commercial. | Groove alignment; gasket condition; pressure and temperature limits. |
Materials
The appropriate material for a spring check valve depends on the system’s media, temperature, and pressure. For more information about material chemical resistances, read our chemical resistance guide.
Valve body
- Stainless steel: Handles high temperatures up to 815°C (1500°F) and pressures over 138 bar (2000 psi). Ideal for demanding industrial applications.
- Brass: Suitable for moderate conditions, withstanding temperatures up to 204°C (400°F) and pressures around 41 bar (600 psi). Common in plumbing and HVAC systems.
- Brass, nickel-plated: Offers similar temperature and pressure ratings as regular brass but with enhanced corrosion resistance.
- Red brass: Manages temperatures up to 260°C (500°F) and pressures around 41 bar (600 psi). Used in water supply systems for its corrosion resistance.
- Polypropylene (PP): Best for lower temperatures up to 82°C (180°F) and pressures up to 10 bar (150 psi). Ideal for chemical and water treatment applications.
- Steel: Withstands high pressures over 207 bar (3000 psi) and temperatures up to 427°C (800°F). Used in industrial settings.
-
Plastic: Plastic spring check valves come in a variety of different materials:
- Polypropylene: Best for lower temperatures up to 82°C (180°F) and pressures up to 10 bar (150 psi). Ideal for chemical and water treatment applications.
- PVC (polyvinyl chloride): PVC spring check valves are suitable for temperatures up to 60 °C (140 °F) and pressures around 10 bar (150 psi). Commonly used in residential and commercial plumbing due to its cost-effectiveness and chemical resistance.
- PA (polyamide/nylon): Can handle temperatures up to 120 °C (248 °F) and pressures around 20 bar (290 psi). Known for its strength and abrasion resistance, making it suitable for industrial applications.
Valve seal
- EPDM (ethylene propylene diene monomer): Excellent resistance to heat, ozone, and weather. Good resistance to polar substances and steam. Poor resistance to petroleum-based fluids.
- NBR (nitrile butadiene rubber): Good resistance to oils, fuels, and other chemicals. Moderate temperature resistance. Poor resistance to ozone and weathering.
- FKM (fluoroelastomer, commonly known by the brand name Viton): Excellent heat and chemical resistance. Good resistance to oils, fuels, and a wide range of chemicals. High temperature stability.
- PTFE (Teflon, polytetrafluoroethylene): Exceptional chemical resistance, low friction, and high-temperature stability. Non-reactive and non-stick properties.
- FEP (fluorinated ethylene propylene): Similar to PTFE but with improved flexibility. Excellent chemical resistance and high-temperature performance. Transparent and can be welded.
- Metal: High strength, durability, and temperature resistance. Can be made from various metals including stainless steel, copper, and aluminum.
Selection criteria
There are several variables to consider when choosing the most suitable spring-loaded check valve for an application:
- Media: Choose a spring-loaded check valve made of the material that best suits media properties and budget.
- System temperature: Temperature is a critical factor when using PVC check valves. However, when using metal check valves, focus on the temperature limitations of the rubber seal.
- System pressure: Ensure that the system's pressure will overcome the valve's cracking pressure and be able to open it fully.
- Closing speed: The spring’s setting impacts how quickly the valve closes. If the valve closes too quickly, water hammer may occur.
Advantages and disadvantages
Advantages
- Versatility: With correct spring settings, spring check valves can be installed in any orientation. Spring check valves perform well in vertical piping locations. These valves depend on the spring’s potential energy to close the valve. Therefore, the valve closes independently without waiting for the fluid to force its way back into the piping.
- Ease of installation: Because of their versatility, spring-loaded check valves are more likely to fit in the system without rearranging pipe configurations.
- Noise control: If water hammer does occur, spring check valves are more able to diminish any disruptive noises. They are considered silent check valves.
- Sealing: With the spring’s support, check valves can fully seal without backflow.
Disadvantages
Spring-loaded check valves are typically more expensive than other check valves (e.g., swing check valves) and have a lower flow capacity. Learn more in our article swing check valves vs spring check valves.
Applications
Spring check valves are suitable for low-risk applications that require zero backflow. For example:
- HVAC systems
- Sprinkler systems
- Sump pumps
High-risk applications that require zero backflow, for example, drinking water systems that connect to public water sources, require backflow preventers.
Learn about other check valves in our article on different types of check valves.
FAQs
What is a spring-loaded check valve?
A spring-loaded check valve has a spring that applies pressure and seals the valve’s disc. It allows media flow in one direction and prevents backflow.
What is the difference between a swing check valve and a spring-loaded check valve?
A spring check valve uses a spring to force the valve to close. A swing check valve has a flapper that allows flow passage but returns to its original position when it stops.
How much pressure is needed to open a spring check valve?
It takes 0.07 to 0.3 bar to overcome the valve's cracking pressure.
Is a swing or spring check valve better?
Spring check valves are more versatile than swing check valves and have better sealing properties. However, spring check valves cost more than swing check valves.
Can a spring check valve be installed horizontally?
Yes, a spring check valve can be installed horizontally and vertically. With the proper spring properties, the valve's flow direction can face in any direction.