Swing Check Valve vs Spring Check Valve
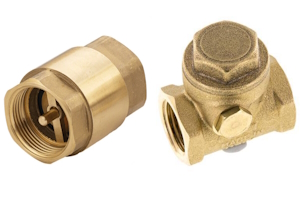
Figure 1: A spring check valve (left) and swing check valve (right)
Swing and spring check valves are essential components in various industrial applications, each offering unique features and benefits. Understanding their differences can help in selecting the correct valve for specific needs. Swing check valves are typically less expensive and suitable for lower flow rates. In contrast, spring check valves are ideal for higher-pressure applications requiring quick valve closure.
View our online selection of check valves!
What is a swing check valve?
The design and operation of swing check valves are straightforward yet effective. These valves consist of a bonnet (Figure 2 labeled A), hinge (Figure 2 labeled B), disc (Figure 2 labeled C), and body (Figure 2 labeled D).
The disc is attached to the hinge, allowing it to swing freely. When fluid flows in the downstream direction, the disc swings away from the valve seat, permitting flow (Figure 2 right). If the flow reverses, gravity or back pressure pushes the disc back against the seat, preventing backflow (Figure 2 left). The bonnet allows easy access to the inside of the valve so it can be cleaned.
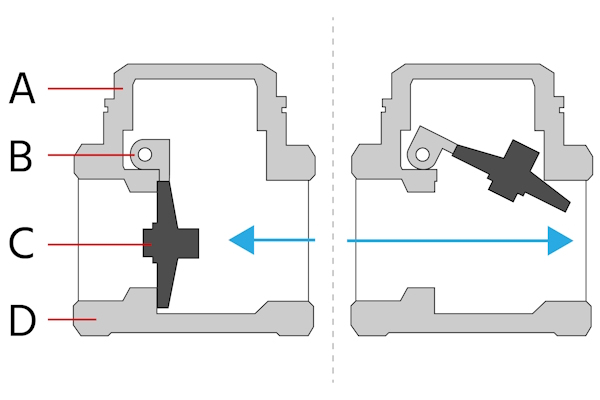
Figure 2: A swing check valve with key components bonnet (A), hinge (B), disc (C), and body (D). It closes if there is backflow (left) and opens during normal flow conditions (right).
Key characteristics & applications
- Simple design: The uncomplicated structure makes them easy to maintain and repair.
- Low pressure drop: The unobstructed flow path results in minimal pressure loss.
- Horizontal and vertical installations: They can be installed in both orientations, although horizontal is more common. For vertical installation, ensure its flow direction is facing upwards.
Swing check valves are useful and work well in many areas because they are simple and dependable. They are used in the following ways:
- Water and wastewater systems: They stop water from flowing backward in city water and sewage systems (e.g., sewer check valves).
- Pumping systems: In pumps, they keep water or fluid from going back into the pump when it's off.
- HVAC systems: They help control where the fluid goes in heating, air-conditioning, and ventilation systems. Learn more in our article that explains the types and uses of HVAC valves.
What is a spring check valve?
Spring check valves, also known as spring-loaded check valves, are designed to allow fluid flow in one direction while preventing backflow. They use a spring mechanism to achieve this function.
The valve's key components are its body (Figure 3 labeled A), closing mechanism which can be a disc, poppet, or ball (Figure 3 labeled B), and spring (Figure 3 labeled C). The spring holds the closing mechanism in place. When fluid flows in the downstream direction, the pressure overcomes the spring tension, pushing the closing mechanism open to allow flow (Figure 3 bottom). If the flow reverses, the spring forces the closing mechanism back against the seat, stopping the flow (Figure 3 top).
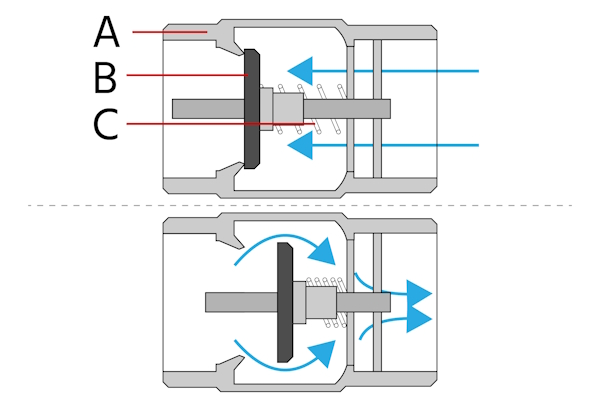
Figure 3: A spring check valve with components body (A), disc or poppet (B), and spring (C). The closed position (top) and open position (bottom).
Key characteristics & applications
- Quick response: The spring mechanism ensures rapid closure, which is beneficial in systems where preventing backflow is critical.
- Compact design: Generally more compact than swing check valves, making them suitable for installations with space constraints.
- Horizontal and vertical installations: Suitable for both orientations.
Spring check valves are useful in many applications where quick response to flow changes is essential. They are used in the following ways:
- Pneumatic systems: Ensure air flows in the correct direction and prevent backflow that could damage equipment.
- Hydraulic systems: Help maintain system pressure and prevent reverse flow, crucial for system stability.
- Fuel and gas lines: Prevent backflow, ensuring safety and efficiency.
- High-pressure systems: Suitable for high-pressure applications where preventing backflow is critical.
Selection criteria: spring vs swing check valve
There are several factors to consider when selecting between a swing check valve and a spring check valve for a specific application. Making the right choice depends on understanding the operational requirements and constraints of the system. Consider the following factors to ensure optimal performance for the application:
-
Flow rates: Swing check valves are generally better for systems with lower to moderate flow rates, while spring check valves can handle a wider range of flow conditions due to their rapid response.
- High-flow rate swing check valves are available
- Pressure: Spring check valves are often preferred in high-pressure applications because of their quick closure, which helps prevent backflow and potential system damage.
-
Orientation: Swing check valves are typically used in horizontal installations, whereas spring check valves can be installed in any orientation without affecting performance.
- Swing check valves can be installed vertically if the downstream flow direction is upwards.
- Maintenance requirements: Swing check valves have a simpler design, making them easier to maintain and repair. Additionally, they typically have a bonnet that allows for easy access to internal components. However, spring check valves may require more frequent maintenance due to the additional components like springs.
- Space constraints: Consider the available space for installation. Spring check valves are more compact, making them suitable for areas with limited space.
- Potential for water hammer: If water hammer is a concern, a swing check valve may be more suitable due to its slower closure speed. However, if the swing check valve is vertically installed or the backflow is especially high, water hammer can still occur with a swing check valve.
Selection examples
Here are some example scenarios that illustrate when one type of check valve might be preferred over the other:
-
Scenario 1: Municipal water supply system
- Preferred valve: swing check valve
- Reason: In municipal water systems, where flow rates are generally stable and pressure is moderate, the simple design and low pressure drop of swing check valves make them an ideal choice. Their cost-effectiveness and ease of maintenance are additional benefits.
-
Scenario 2: High-pressure steam system
- Preferred valve: spring check valve
- Reason: In high-pressure steam applications, the quick response of spring check valves is crucial to prevent backflow and potential damage. Their ability to handle high-pressure environments and provide reliable sealing makes them suitable for such scenarios.
-
Scenario 3: Compact HVAC system
- Preferred valve: spring check valve
- Reason: In HVAC systems with limited installation space, the compact design of spring check valves is advantageous. Their flexibility in orientation and reliable performance in various flow conditions make them a practical choice.
-
Scenario 4: Gravity-dependent drainage system
- Preferred valve: swing check valve
- Reason: For drainage systems that rely on gravity, swing check valves are effective due to their simple operation and ability to handle low-pressure conditions. Their design is well-suited for horizontal installations typical in such systems.
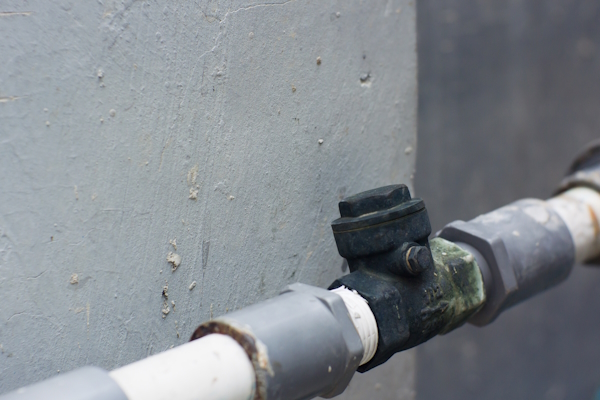
Figure 4: A swing check valve installed in a water pipe system.
FAQs
What is a swing check valve?
A swing check valve uses a hinged disc to allow flow in one direction and prevent backflow, ideal for low-pressure applications.
What is a spring check valve?
A spring check valve uses a spring-loaded disc to quickly close and prevent backflow, suitable for high-pressure applications.
How do swing and spring check valves differ?
Swing check valves are cost-effective for low flow rates, while spring check valves offer rapid closure for high-pressure systems.
When should I use a swing check valve vs a spring check valve?
Use a swing check valve for low-pressure systems and a spring check valve for high-pressure, fast-closing needs.