Understanding the deadband of a pressure switch
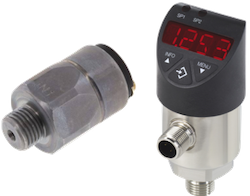
Figure 1: Pressure switches
Understanding how the deadband of a pressure switch affects the operation of the switch is important when deciding on the right type of pressure switches to select. The deadband prevents the pressure switch from continuously toggling the switch position which can damage the equipment it controls. Choosing the correct deadband is therefore also an economical choice. Depending on the type of pressure switch, the deadband can be fixed or adjustable within a range such as in mechanical pressure switches or through the entire range of measured pressure values such as in electronic pressure switches.
Table of contents
- Deadband of a pressure switch
- Dead band working principle
- Characteristics
- Determining the deadband range of a pressure switch
- Selection criteria
Deadband of a pressure switch
The term 'deadband' as used in pressure switches is the difference in pressure value between the setpoint (the pressure at which the switch activates) and the reset point (the pressure at which the switch deactivates). It is sometimes used interchangeably with the terms 'differential' or 'hysteresis' of a pressure switch. The main purpose of a deadband in pressure switches is to prevent chattering of the switch by introducing a threshold for when the electrical connection should close and open. Therefore, for a pressure switch to work correctly, it must have a deadband.
Dead band working principle
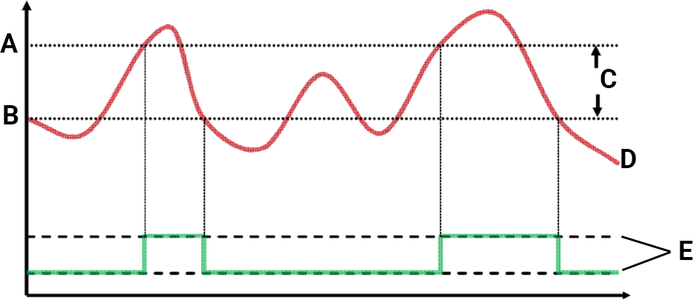
Figure 2: The effect of pressure variations on switch status. Setpoint (A), Reset point (B), Deadband (C), Pressure (D), Switch on/off (E)
The principle of the deadband of a pressure switch is quite simple. As illustrated in Figure 1, the variations in the pressure values do not change the status of the switch until the setpoint is reached. The switch remains in an ON position until the pressure drops below the reset point.
For example: Imagine a fluid vessel supplying its content to a process stream. The system requires the pump to stop when the pressure is above the setpoint. When the pressure drops back down below the reset point, it will start back up until once again it reaches above the setpoint.
Without a deadband, the switch will start and stop the pump continuously as the measured pressure goes above and below the setpoint. This is an undesired condition that could damage the pump. By setting a deadband (or reset point), a differential is created between when the pump is stopped and when the pump is started. This simple solution prevents the continuous start and stop of the pump, thereby extending its useful life.
Another illustration is when you try to prevent the suction side of a compressor from operating below atmospheric conditions for safety reasons. The setpoint is 1 bar (14.5 psi) and the reset point is 1.5 bar (21.7 psi). The deadband is therefore 0.5 bar (7.2 psi). With this configuration, the compressor will stop working when the pressure at the suction side drops below 1 bar (14.5 psi) but will only start working when the pressure rises above 1.5 bar (21.7 psi).
Characteristics
There are two main types of pressure switches: The mechanical pressure switch (sometimes called electromechanical pressure switch) and the electronic pressure switch (often called the solid-state pressure switch).
Mechanical pressure switch
The mechanical pressure switch is activated by different pressure sensing principles such as the weld-sealed metal diaphragm, bourdon tubes, elastomeric diaphragm on piston, direct piston, etc. The robustness of the pressure sensing principle sets the operating range and the possible deadband values of the pressure switch. The direct piston pressure switches have extensive deadbands while diaphragm and bourdon tube pressure switches have limited deadbands. The deadbands for mechanical pressure switches are adjusted by knobs attached to the switch but are often fixed by the manufacturer or linearly adjustable with the setpoint.
Electronic pressure switch
The electronic pressure switch is activated by a pressure-sensing element similar to pressure transmitters. They are quite rigid with the possibility of sending analog signals to a controller. The deadband of an electronic pressure switch covers the entire range of operation of the pressure switch and can be adjusted through digital displays on the switch or a controller.
Deadband selection
Applications with control logic typically require wider deadbands as compared with pressure switches used to trigger an alarm or prevent a dangerous operating condition. A wider deadband may be useful to control a pump while a narrow deadband will be sufficient to stop a compressor from operating below atmospheric conditions.
Determining the deadband range of a pressure switch
It is important to remember that the deadband is sometimes called a differential or a hysteresis of a pressure switch. For most mechanical pressure switches, the deadband value is specified in a percentage range, typically 10 – 30%. This percentage range implies that the difference between the setpoint and the reset point can be at a value between 10 – 30% less than the setpoint. In other words, if a setpoint is 10, then the reset point can be between 7 and 9. The pressure switch manual will state if the deadband is adjustable and give instructions on how to adjust it.
Selection criteria
- Application: Is there a need for a narrow deadband, or for a wide deadband? For control purposes, a wider deadband usually suffices, while for safety purposes, a narrow deadband is usually needed.
- Field adjustability: Is it a fixed deadband set by the manufacturer, adjustable in the field, or through a controller?
- Wide adjustable deadband: Is the range of deadband suitable for your application?
- Independent adjustments for setpoint and reset point: Can the setpoint and reset point be independently adjusted or are they linearly dependent?
- Minimum and maximum deadband: Is there a minimum deadband setting beyond or below which the pressure switch control is no longer consistent?