Pressure Monitoring In Pump Systems
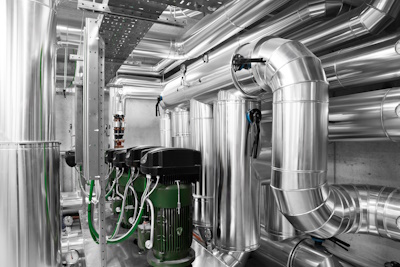
Figure 1: Pressure monitoring devices ensure efficient and safe operation in HVAC systems
Monitoring pressure in pumping systems is essential for maintaining optimal performance and identifying potential problems. Variations from standard pressure levels can indicate issues like clogged filters, blocked pipes, or worn impellers. By consistently tracking pressure data, maintenance teams can identify these problems early and take corrective measures to prevent further damage and ensure efficient pump operation. This article examines how maintaining optimal pump pressure enhances the efficiency and reliability of pump systems.
Table of contents
- Importance of pressure monitoring in pump systems
- Key components of a typical pump system
- Types of pressure monitoring devices in a pump system
- Independent and interdependent devices
- Applications of pressure monitoring devices in the pump industry
- FAQs
View our online selection of pressure monitoring devices!
Importance of pressure monitoring in pump systems
Pumps are used in various systems like air compressors, irrigation systems, and heat exchangers to move air or water. If the pressure in these systems is too high or too low, it can have serious consequences for the pump, pipes, or the entire system. Most engineers select pumps that operate within 80-110% of their Best Efficiency Point (BEP), where the pump is most efficient. Operating outside of this range can degrade pump performance, making pressure monitoring vital to maximize efficiency.
Insufficient pressure can negatively impact the performance of a pump system in several ways:
- Increased energy usage: Pumps operating at lower pressures often need more energy to achieve the desired flow rates. By monitoring pressure, pump settings can be optimized to reduce energy consumption and enhance efficiency.
- Lower flow rate: When pressure is inadequate, the flow rate decreases, which can prevent the pump from meeting system demands. This can result in inefficiencies in industrial processes or shortages in water supply.
- Shortened component lifespan: Low pressure puts extra stress on pump components, causing them to wear out more quickly. Bearings, seals, and impellers are especially vulnerable to damage under these conditions, which can reduce the overall lifespan of the pump system.
Key components of a typical pump system
A typical pump system includes several essential components that facilitate fluid movement:
- Pump: Pump transfers different fluids from one location to another through mechanical action.
- Motor or driver: The power source that drives the pump's mechanical components, converting energy into kinetic energy for fluid movement.
- Piping and valves: Valves and piping in a pump system (Figure 6) control the flow and direction of fluids, ensuring efficient and safe transport from one location to another.
- Control systems: Devices and systems that regulate the pump's operation, like speed controllers, flow meters, pressure regulators, and monitoring equipment.
- Couplings and bearings: Couplings and bearings in a pump system connect and align rotating components while minimizing friction and wear, ensuring smooth and efficient operation.
Types of pressure monitoring devices in a pump system
Pressure gauge
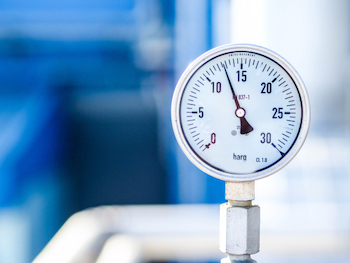
Figure 2: Pressure gauge
Pressure gauges are typically installed near the pump or on the pressure tank. It measures and displays the fluid pressure, ensuring the system operates within safe parameters. For example, a water pump or well pump pressure gauge monitors water pressure to maintain desired levels, diagnose issues, and control pump operation. It is generally connected via a threaded fitting and integrated with control devices like pressure switches to automate and optimize system performance. Read our pressure gauge overview article for more information on the working and applications of pressure gauges.
Pressure sensor/transducer
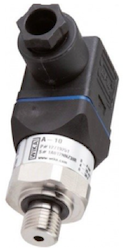
Figure 3: Pressure transducer
Pressure sensors or transducers (Figure 6 labeled F) are installed at critical points in the system, such as near the pump or along the pipeline. They convert input pressure into proportional electrical signals for monitoring and control. In pump systems, they provide precise and continuous pressure data, which can be used for real-time monitoring, automation, and safety mechanisms. These sensors are integrated with control systems to adjust pump operation, trigger alarms, or shut down the system in case of abnormal pressure conditions. Read our pressure transducer overview article for more information on the working and types of pressure transducers.
Pressure switch
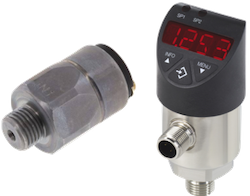
Figure 4: Pressure switches
Pressure switches (Figure 6 labeled M) are typically installed near the pump or pressure tank. They monitor the pressure within the system and activate or deactivate electrical circuits based on preset pressure thresholds. Pressure switch for a pump automates the pump operation. For example, when the system pressure drops below a certain level, the pressure switch closes its contacts to turn the pump on, and when the pressure reaches the upper threshold, it opens the contacts to turn the pump off. This ensures consistent pressure levels, prevents pump overrun, and protects the system from damage due to overpressure or under pressure conditions. Read our pressure switch overview article for more information on working mechanisms of pressure switch types, their typical selection criteria, and their applications.
Pressure regulator
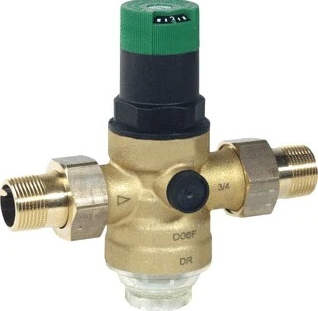
Figure 5: Water pressure regulator
Pressure regulators are typically installed downstream of the pump. They maintain a constant output pressure regardless of variations in input pressure or flow demand. For example, a fuel pump with a pressure regulator ensures that the fuel is delivered to the engine at a consistent and optimal pressure. This compensates for any fluctuations in the fuel supply, and helps prevent issues such as fuel starvation, over-pressurization, and potential damage to the fuel injectors or other engine components. Read our pressure regulator overview article for more information on the design and operating principles of pressure regulators.
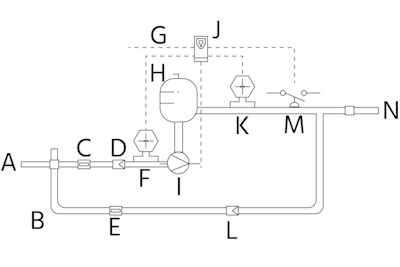
Figure 6: Water pump system example: Water supply (A), optional bypass (B), ball valve (C, E), check valve (D, L), pressure sensor (F, K), power supply (G), pressure tank (H), pump (I), variable frequency drive (J), pressure switch (M), and flow output (N).
Independent and interdependent devices
While most pressure monitoring devices are designed to work together, some can function independently:
-
Independent devices:
- Pressure gauges: Pressure gauges can operate independently, providing manual pressure readings without the need for integration with other systems.
- Pressure regulators: Pressure regulators can maintain a constant output pressure without requiring input from other monitoring devices.
-
Interdependent devices:
- Pressure sensors/transducers and control systems: These devices rely on each other for real-time monitoring and control. The sensor provides data, and the control system uses this data to adjust pump operation.
- Pressure switches and pumps: Pressure switches are often directly connected to pumps, automating their operation based on pressure levels.
Applications of pressure monitoring devices in the pump industry
- Water lift systems: Pumps are used to lift water to higher elevations where traditional gravity-fed systems fall short. Pressure monitoring devices ensure standard operation and maintain optimal pressure levels.
- Clean water systems: In clean water systems, pumps transport water between treatment facilities via pipelines. Pressure instruments provide feedback to Variable Frequency Drives (VFDs) for reliable transportation and consistent pressure maintenance.
- Sewage pumping systems: Pumps deliver sewage to treatment plants. Monitoring inlet and outlet pressure helps control flow rates and ensures the system operates within safe pressure limits.
- Industrial pumping systems: Used in chemical processing, oil and gas, and manufacturing, these systems rely on pressure monitoring for safety and efficiency. Continuous data and real-time feedback help maintain desired pressure levels and trigger alarms if necessary.
- HVAC systems: Pumps circulate water or refrigerant in HVAC systems. Pressure monitoring devices ensure efficient and safe operation, providing control feedback and facilitating maintenance checks.
- Fire suppression systems: Pumps deliver water or fire retardant in emergencies. Pressure devices ensure system activation and proper pressure delivery, indicating system readiness and maintaining pressure.
Example
Consider a municipal water supply system that maintains a consistent pressure, critical to ensure reliable water delivery to consumers. Pressure sensors monitor the pressure at various points in the distribution network. Data from these sensors is fed to a central control system, which uses VFDs to adjust pump speeds. Pressure switches are installed at critical points to automatically activate backup pumps if the pressure drops below a certain threshold. Pressure regulators ensure that the output pressure remains stable, preventing fluctuations that could disrupt water supply.
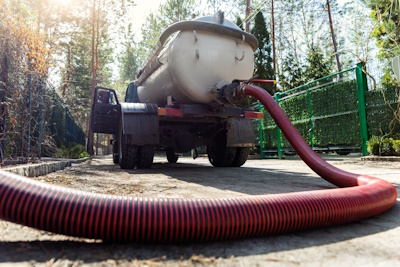
Figure 7: Sewage pumping systems use pressure monitoring devices to control flow rates and ensure the system operates within safe pressure limits.
FAQs
What is a pressure switch for a well pump?
It ensures that the water pressure is maintained within the desired range, automatically controlling the pump to provide consistent water supply and protect the system from damage.
Why is a pump pressure test needed?
A pump pressure test diagnoses and prevents potential issues in pump systems. The test measures the pressure at various points in the system to ensure it operates properly.