Common Solenoid Valve Issues and Fixes
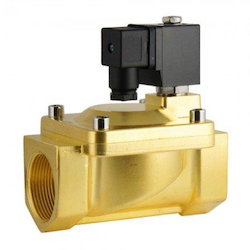
Figure 1: 2/2-way solenoid valve
While relatively simple, solenoid valves can encounter issues like not opening/closing properly, leaking, or overheating. Another common issue is a too-low differential pressure for indirect operated solenoid valves. These issues often stem from debris, damaged parts, or electrical problems. Fixes include cleaning, replacing damaged components, and repairing electrical or cooling systems.
Solenoid valve troubleshooting
This section provides comprehensive guidance on how to troubleshoot the following common solenoid problems:
- The solenoid valve does not open
- The solenoid valve opens partially
- The solenoid valve makes a humming noise
- The solenoid coil is burnt
View our online selection of solenoid valve products!
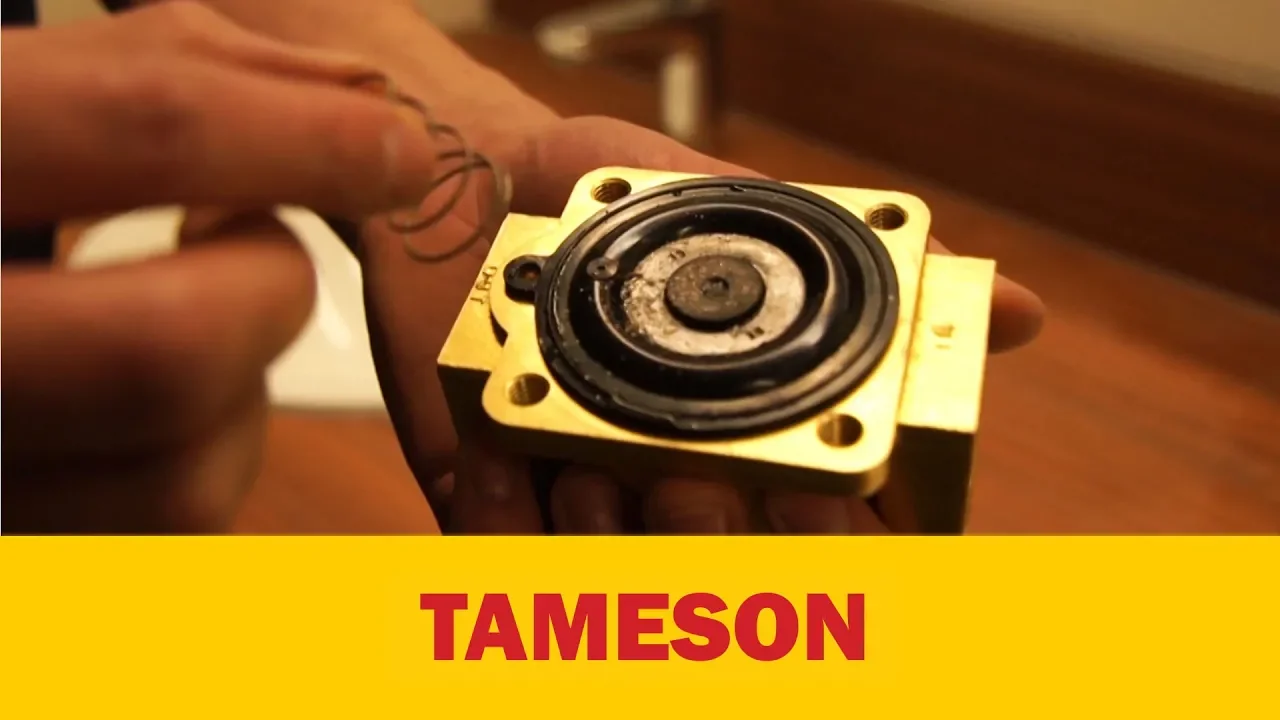
Solenoid valve does not open
Probable cause | Solution |
No power to the coil | Check if the valve is normally open (closes when electrically energized) or normally closed (opens when electrically energized). Measure the voltage across the coil with the aid of a voltmeter or multimeter. Ensure voltage across the coil matches its required specifications. Pull the coil up a little and feel if the coil produces resistance to displacement (magnetic field). Note: Removing a powered coil may cause the coil to burn. Check the relay contacts, wires and fuses. |
Incorrect voltage/frequency | Make sure the power supply matches the valve specification. Measure the voltage across the coil. |
The coil is burnt | See the section below about burnt coils. |
Differential pressure is too high | Check the pressure differential across the valve using two separate pressure gauges or a differential pressure gauge. Compare the differential with the valve specification. If possible, you can make the pressure difference smaller, for example by reducing the input pressure. |
Differential pressure is too low | Check the valve specification. Indirect controlled solenoid valves need a small differential pressure to operate properly. If necessary, replace the solenoid valve for a suitable alternative, such as a (semi) direct operated solenoid valve. |
Damaged or deformed valve | Replace the solenoid valve |
Dirt on the membrane | Clean the membrane. If necessary, replace broken or damaged components. |
Polluted valve seat or valve | Clean the valve. If necessary, replace broken or damaged components. |
Corrosion (rust) | Replace damaged components |
Components missing after disassembly | Install the missing components |
The solenoid valve opens partially
Probable cause | Solution |
Pressure too low | Check the valve specification for the minimum differential pressure. Indirectly controlled solenoid valves require a small differential pressure for proper operation. Replace the valve with a type that operates from 0 bar, such as a (semi) direct operated solenoid valve or an electric ball valve. |
Damaged or bent armature tube | Replace the valve |
Dirt on the membrane | Clean the membrane and, if necessary, replace the broken parts |
Dirt in the valve seat/valve/pipe fittings | Clean the valve, if necessary, replace broken parts |
Corrosion | Replace defective parts |
Part missing after the assembly | Replace the missing parts |
The solenoid valve makes a humming noise
Probable cause | Solution |
Buzzing | AC coils can cause a humming noise, which can get louder if nearby parts vibrate at the same frequency. Securing these parts can reduce the noise. Installing a rectifier, like a power saver module, can also solve the buzzing problem. |
Water hammer | Increase the pipe diameter to reduce the fluid velocity. Reduce the pressure with a pressure-reducing valve before the solenoid valve. Dampen the water hammer by using a flexible hose or buffer before the solenoid valve. Use a solenoid valve with a longer response time. This reduces the pressure transients. |
Differential pressure too high and/or pulsation in input line | Check valve specification and differential pressure. Check pressure and flow. Replace with a suitable valve. Check out the rest of the installation. |
Coil is burnt
Probable cause | Solution |
Incorrect voltage/frequency | Check the coil specification. If necessary, replace it with an appropriate type of coil. Check the wiring diagram. Check the voltage variations. |
Coil short circuit (possibly fluid) | Check the rest of the installation for possible short circuits. Check the connections of the coil. Replace the coil when the error is found. Note the installation of the coil, make sure that no moisture can flow or drip in the connection. |
The plunger moves with high friction (by dirt, damage or bending) | Replace broken parts and remove dirt |
The temperature of the medium is too high. | Check the valve specification. If necessary, replace the valve with a suitable variant. |
The ambient temperature is too high. | If possible, move the valve to a cooler environment. Check the valve specification. Increase ventilation around the coil and valve. |
FAQs
How to fix a stuck solenoid valve
To fix a stuck solenoid valve, first, ensure power is off. Check for debris and clean. Inspect and lubricate the plunger. Verify electrical connections and correct voltage. Replace damaged parts.
What are common solenoid valve issues?
Common solenoid valve issues include not opening/closing properly, leaking, overheating, and low differential pressure for indirect operated valves.
What causes a solenoid valve to get stuck?
A solenoid valve can get stuck due to debris, corrosion, damaged internal components, or electrical issues.