Control Valve Overview - Globe, Angle Seat, Diaphragm, & Disc Valves
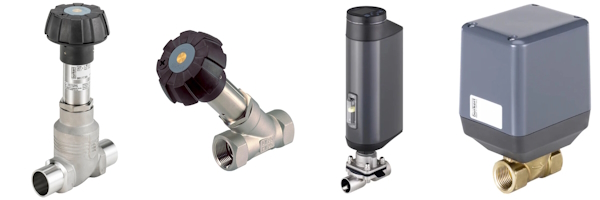
Figure 1: Common control valves used across industries: globe, angle seat, diaphragm, and disc valves
Control valves play a crucial role in the regulation of flow, pressure, and temperature in various industrial processes. Among the various valve types, globe, angle seat, diaphragm, and disc valves stand out for their specific functionalities and applications. This article provides a comprehensive overview of these four key types of control valves, highlighting their design principles, operational mechanisms, and suitability for different process conditions.
Note: A control valve is used to control the media through it. There are numerous valve types that can control media flow, but for the purpose of this article only globe valves, angle seat valves, diaphragm valves, and disc valves are discussed as these are generally referred to within the "control valves" nomenclature.
Table of contents
View our online selection of control valves!
Globe valves
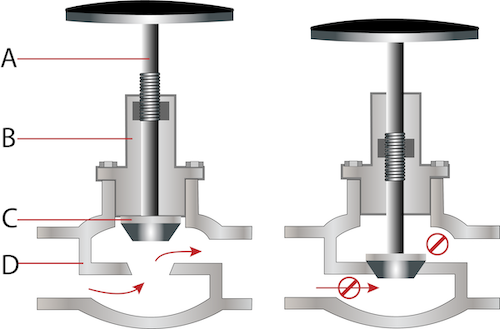
Figure 2: A globe valve in the open position (left), and in the closed position (right) with the valve stem (A), bonnet (B), disc or plug (C), and valve body (D).
Globe valves, characterized by their spherical body shape, are designed to regulate flow in a pipeline. The internal mechanism consists of a movable disk-type element and a stationary ring seat in a generally spherical body. The primary feature of a globe valve is its precise flow control. It has a linear motion valve stem that moves perpendicular to the seat, which is operated by a handwheel or actuator. This design facilitates the valve's function in starting, stopping, and throttling flow.
Main features
- Linear motion: The stem of a globe valve moves in a linear direction, providing precise control over the flow rate. This is particularly advantageous for applications requiring fine adjustment of flow.
- Tight shut-off capability: Globe valves are known for their superior shut-off capabilities, making them suitable for applications where leakage must be minimized.
- Throttling characteristics: The design of the globe valve allows for excellent throttling capabilities. The flow pattern and the disc shape are conducive to gradual changes in flow, reducing the risk of water hammer.
- Pressure drop: Due to the complex path the fluid must navigate through the valve, globe valves inherently have a higher pressure drop compared to other valve types, which must be considered in system design.
Applications
Globe valves are extensively used in applications that require frequent stroking, fine throttling, and where the pressure drop through the valve is not a critical factor. Their ability to precisely control flow makes them ideal for use in:
- Cooling water systems where flow needs to be regulated.
- Fuel oil systems where leak integrity is of high importance.
- Feedwater and steam systems in power plants where precise flow control is necessary.
Advantages
- Precision control: The design of globe valves allows for precise control of flow, making them suitable for applications where this is critical.
- Durability: Globe valves are robust and durable, capable of withstanding high pressure and temperature conditions.
- Versatility: Available in various materials, globe valves can be used for a wide range of fluid types, including corrosive substances.
Limitations
- Higher pressure drop: The design that facilitates precise control also results in a higher pressure drop across the valve, which can be a significant factor in system design and efficiency.
- Multi turn: Not suitable for applications requiring quick shutoff due to the multi-turn operation
- Cost: Globe valves can be more expensive than other types of valves due to their complex design and the materials required for their construction.
Read our globe valve repair guide for more details on the steps involved in globe valve installation, repairs, and the importance of regular maintenance.
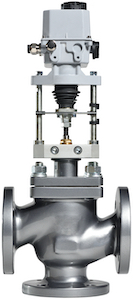
Figure 3: A pneumatic globe valve
Angle seat valves
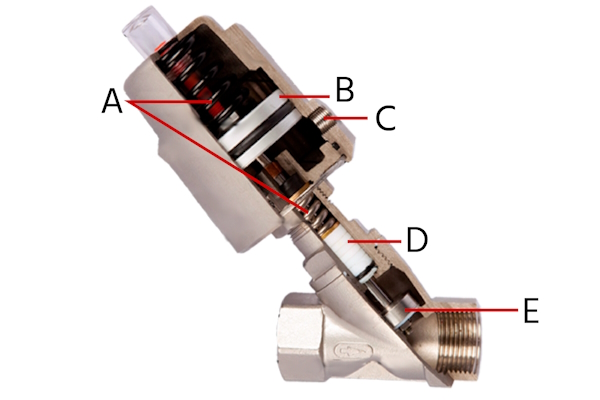
Figure 4: Section view of an angle seat valve
Angle seat valves are characterized by their distinctive Y-shaped body that allows fluid to flow through at an angle, optimizing flow rate and minimizing pressure drop across the valve. They typically operate using a pneumatic actuator that moves a piston or diaphragm, which in turn lifts the valve plug off its seat. This design is particularly effective for applications involving viscous fluids or slurries, as the flow path is less restrictive compared to other valve types.
Main features
- High flow rates: The angled design facilitates a smoother flow of fluid, allowing for higher flow rates compared to other valve types with a similar size.
- Durability: Constructed typically from stainless steel and other corrosion-resistant materials, angle seat valves are designed to withstand harsh operating conditions, including high temperatures and corrosive environments.
- Minimal clogging: The flow path through an angle seat valve reduces the risk of clogging, making it suitable for applications involving particulate-laden fluids.
Applications
Angle seat valves are versatile and can be used in a wide range of applications. Their high flow rate and resistance to clogging make them particularly suitable for:
- steam control in sterilization processes, where their ability to handle high temperatures is crucial
- controlling viscous fluids or slurries in the chemical and food processing industries, where the smooth flow path reduces the risk of clogging
Advantages
- High flow rate: The design of angle seat valves allows for efficient flow control, even in systems with high flow rates and viscous media.
- Long life: High cycle life, making them a long-life alternative to ball valves
- Low maintenance: The simplicity of the design and the durability of the materials used in construction contribute to lower maintenance requirements.
- Versatility: Suitable for a wide range of temperatures and fluids, including steam, water, gasses, and chemicals. Also, angle seat valves exhibit resistance to clogging, making them an excellent choice for applications prone to particulate matter buildup.
Limitations
- Limited precision control: While angle seat valves offer efficient flow control, they may not provide the same level of precision as globe valves in applications requiring fine throttling.
- Actuation: Being typically pneumatically operated, the requirement for a compressed air supply can be a limitation in environments where this is not readily available.
Diaphragm valves
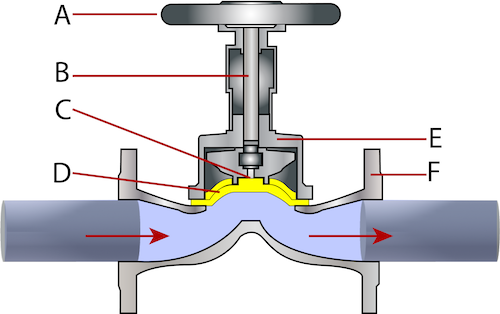
Figure 5: The components of a diaphragm valve: handwheel/manual actuator (A), stem (B), compressor (C), diaphragm (D), bonnet (E), and valve body (F).
Diaphragm valves consist of a valve body with two or more ports, a diaphragm, and a "weir" or saddle upon which the diaphragm presses against to close the valve. The diaphragm is a flexible, pressure-responsive element that transmits force to open, close, or modulate the valve. This design isolates the valve mechanism and the flowing medium, making it ideal for handling corrosive substances, gasses, and bio-pharmaceutical process fluids where purity and contamination prevention are critical.
Main features
- Fluid isolation: The diaphragm effectively separates the fluid from the valve operating mechanism, minimizing the risk of leakage and contamination.
- Corrosion resistance: With the appropriate selection of diaphragm materials (e.g., EPDM, PTFE), diaphragm valves can handle a wide range of corrosive fluids.
- Sanitary applications: The valve's design, without crevices or dead spots, makes it suitable for sanitary applications, as it can be easily cleaned or sterilized in place (CIP/SIP).
Applications
Diaphragm valves are extensively used in industries where hygiene and purity are paramount, as well as in applications involving corrosive or particle-laden fluids:
- Chemical processing: For controlling the flow of corrosive gasses and liquids, where material compatibility and leak prevention are crucial.
- Pharmaceuticals and bioprocessing: In systems requiring sterile conditions, such as fermentation and media preparation, where the valve's cleanability and minimal risk of contamination are essential.
- Water treatment: For handling chlorine and other disinfectants in water treatment plants, where corrosion resistance and reliability are necessary.
Advantages
- Leak-proof design: The tight seal formed by the diaphragm ensures a high level of leak protection, enhancing safety and process integrity.
- Corrosion resistance: Diaphragm valves can be constructed from or lined with materials that are resistant to corrosion, making them ideal for handling aggressive chemicals.
- Minimal contamination: The design of diaphragm valves ensures that the process fluid is completely isolated from the valve mechanism, reducing the risk of contamination.
- Low maintenance: The absence of packing glands or stuffing boxes reduces maintenance needs and the risk of leaks.
Limitations
- Temperature and pressure limits: Diaphragm valves are generally not suitable for high temperature and high-pressure applications due to the limitations of the diaphragm material.
- Throttling capability: While capable of throttling, they may not offer the same level of precision control as globe valves, especially under varying pressure conditions.
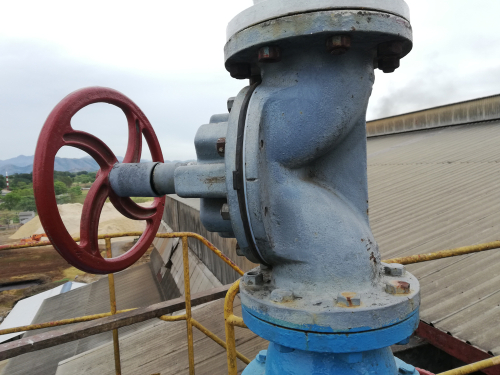
Figure 6: A diaphragm valve used in a hot water pumping system
Disc valves
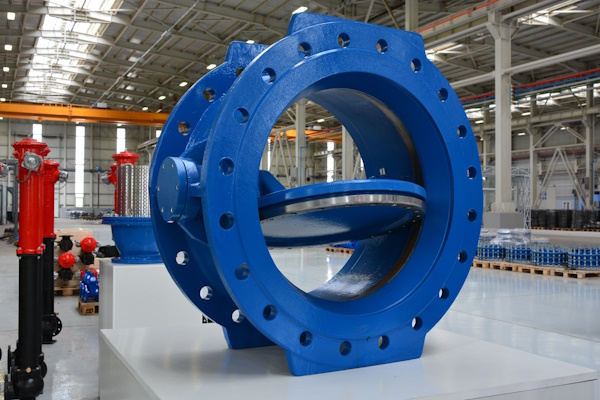
Figure 7: Butterfly valve showing an open disc
The operation of disc valves involves a circular disc mounted on a central shaft or hinge. This disc can rotate to open or close the flow path. This design allows for quick and efficient flow control with minimal pressure drop across the valve.
Main features
- Compact and lightweight: The streamlined design of disc valves makes them significantly smaller and lighter than other types of valves, such as globe or gate valves, facilitating easy installation and maintenance in space-constrained applications.
- Quick operation: The quarter-turn operation of disc valves enables rapid opening and closing, which is beneficial in applications requiring fast flow stoppage or where flow conditions change frequently.
- Versatility: Available in a wide range of materials for the disc and seals, disc valves can be used with a variety of fluids, including water, chemicals, and gasses.
Applications
Disc valves are versatile and can be used across a broad spectrum of applications, though they are particularly favored in the following scenarios:
- Water and wastewater treatment: For controlling flow in water distribution systems, including pump stations and filtration units, where their quick operation and durability are advantageous.
- HVAC systems: In HVAC systems, where their compact size and ease of operation facilitate efficient flow control of air and water.
- Light industrial applications: For handling gasses and liquids in manufacturing processes, especially where space is limited and quick valve operation is required.
Advantages
- Cost-effectiveness: Disc valves are generally less expensive than other types of valves, making them a cost-effective option for many applications.
- Low pressure drop: The straight-through flow path when the valve is open results in a minimal pressure drop, enhancing system efficiency.
- Ease of maintenance: The simple design and minimal number of moving parts reduce maintenance requirements and downtime.
Limitations
- Sealing: While disc valves can provide a tight seal, achieving a zero-leakage seal is more challenging compared to some other valve types, particularly in high-pressure applications.
- Wear: The components, especially the seals, may wear more quickly in high-cycle applications, impacting the valve's longevity and performance.
Comparison of control valves
Table 1: Control valve types comparison
Feature | Globe valves | Angle seat valves | Diaphragm valves | Disc valves |
Design | Spherical body with a movable disk and stationary seat | Y-shaped body with a pneumatic actuator and angled seat | Valve body with a flexible diaphragm that separates flow from the mechanism | Compact design with a disc-shaped closure element mounted on a rod |
Operation | Linear motion of the valve stem for precise control | Pneumatic actuation for efficient flow control | Flexible diaphragm operated manually or by actuation for flow control | Quarter-turn operation for quick opening and closing |
Main features | Precise flow control, tight shut-off capability | High flow rates, minimal clogging | Fluid isolation, corrosion resistance, suitable for sanitary applications | Compact and lightweight, quick operation, versatile |
Advantages | Excellent throttling and control, durable | Efficient flow control with low maintenance, good for viscous fluids | Leak-proof design, low maintenance, good for corrosive and sanitary applications | Cost-effective, low pressure drop, easy maintenance |
Limitations | Higher pressure drop, more expensive | Limited precision control, requires compressed air | Limited to low-pressure and temperature applications, less precise control | Challenges in achieving zero-leakage seal, potential for wear in high-cycle applications |
Typical applications | Applications requiring frequent stroking and fine throttling, such as cooling water systems and fuel oil systems | High flow rate applications and steam control, such as in chemical and food processing | Chemical processing, pharmaceuticals, water treatment, where purity and corrosion resistance are crucial | Water and wastewater treatment, HVAC systems, light industrial applications for gasses and liquids |
Material compatibility | Available in various materials for different fluid types | Typically stainless steel for corrosion resistance | Variety of body and diaphragm materials for specific process requirements | Wide range of materials for disc and seals to suit various fluids |
Pressure drop | Higher due to design | Lower compared to globe valves | Low, suitable for applications sensitive to pressure drop | Minimal when fully open |