What Is a Flanged Fitting
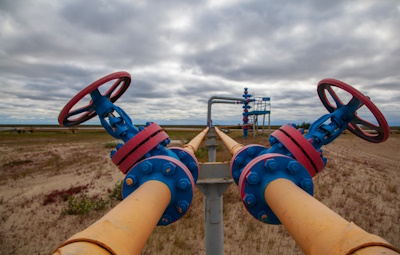
Figure 1: Flanged valves used in oil and gas industry
Flanged fittings allow easy assembly and disassembly for inspection, cleaning, or repair in piping networks transporting water, chemicals, gas, or other media. These fittings are crucial in various piping systems, providing a secure and accessible means of connecting pipes, valves, pumps, and other equipment. This article explores the various types of flanged fittings, the materials used, and their sizing considerations.
Table of contents
- What are flanged fittings
- Flanged fitting types
- Materials
- Flanged fitting dimensions
- Sizing chart
- FAQs
What are flanged fittings
Flanged tube fittings have a flange or a set of flanges on one or both ends. A flange connects pipes, valves, pumps, and other equipment to form a piping system. Flanged fittings are typically joined together using bolts and a gasket to provide a seal (Figure 2). However, other joining methods exist for specific applications, like welding and fusion bonding. The choice of joining method depends on the specific application, pressure rating, and desired ease of disassembly. Read our pipe flanges overview article for more information on the various flange types.
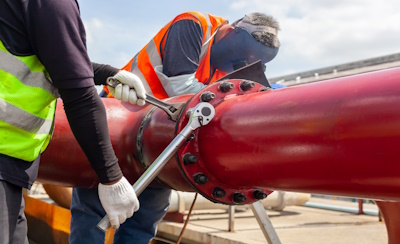
Figure 2: Tightening bolts and nuts of a flange connection in a piping system
Flanged fitting types
Here are some common flanged fitting types:
- Flanged elbows: These are elbows with flanges attached to them. They are used to change the direction of the pipe run. They come in various angles, most commonly 45° and 90°.
- Flanged tees: Flanged tee fittings have a T-shape. They are used to either combine or split media flow. There are straight tees (the diameter is the same across all three ends) and reducing tees (one of the ports is smaller than the other two).
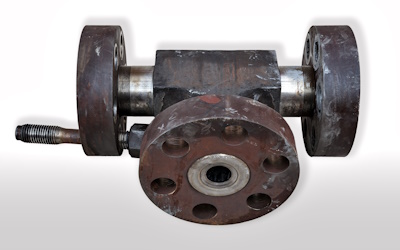
Figure 3: Flanged tee fitting
- Flanged reducers: These fittings connect pipes of different sizes. They have a flange on each end, with one end larger than the other to accommodate different pipe diameters.
- Flanged crosses: These are similar to tees but have four openings in four directions. These are used when four pipes converge at a single point.
- Flanged adapters: Adapters can have one flanged end and another with a different connection type, such as threaded or butt-weld. These are used to connect pipes with different end connections.
- Flanged valves: Gate valves, globe valves, check valves, ball valves, and butterfly valves often have flanges to connect flanged pipes and fittings. Read our flanged vs screwed valve article for a comparison between flanged and screwed valve types.
- Flanged strainers and filters: Flanged strainers are installed in the pipeline to remove unwanted particles from the fluid. The flanges help connect to other pipeline components.
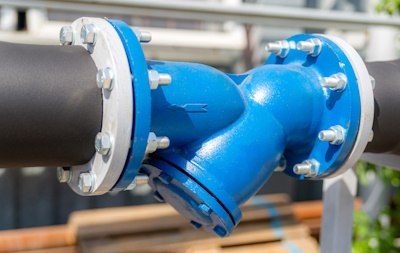
Figure 4: Flanged strainer used in industry
- Flanged expansion joints: Flanged expansion joints absorb thermal expansion or terminal movement in piping systems. They are flexible connectors that have flanges on both ends.
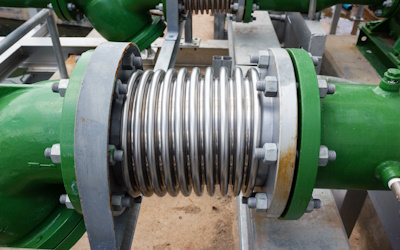
Figure 5: Flanged expansion joint
Materials
Table 1: Flange fitting materials
Material type | Characteristics | Applications | Specifications/grades |
Carbon Steel | Cast iron flanged fittings are strong, cost-effective, moderate to high-temperature resistance | Oil and gas, petrochemical, water supply systems | ASTM A105 |
Stainless Steel | Flanged stainless steel fittings are corrosion-resistant, and used at a wide range of temperatures | Water, steam, gas, and chemical transport | Stainless steel 304, 316 and 321 |
Alloy Steel | Increased strength, corrosion resistance due to other alloying elements like Cr, Mo, and Ni | High-pressure and high-temperature environments, power plants, refineries | ASTM A182 |
Duplex & Super Duplex Stainless Steel | Higher strength and superior corrosion resistance compared to standard stainless steel | Offshore, marine, chemical processing | Duplex 2205, Super Duplex 2507 |
Nickel Alloys | Excellent resistance to heat and corrosion, used in highly corrosive environments | Chemical processing, marine, aerospace, oil and gas | Inconel, Monel, Hastelloy, Incoloy |
Copper/Copper alloys | Flange copper pipe fittings have good thermal conductivity and corrosion resistance | Heat exchangers, water supply systems | C11000 (Copper), C36000 (Free-cutting Brass), C61400 (Aluminum Bronze) |
Plastics | Flanged PVC pipe fittings are lightweight, excellent chemical resistance, used in low-pressure applications | Chemical processing, water treatment, sewage | PVC, CPVC, PP, PVDF |
Composite Materials | Resistance to chemical attack, suitable for highly corrosive environments | Chemical processing, water treatment, sewage | FRP, thermoplastic-lined composites |
Flanged fitting dimensions
Flange fitting dimensions are standardized to ensure they fit together with components from different manufacturers. The dimensions of flanges are governed by a series of standards that specify their size, shape, and tolerances.
Here are some key dimensions typically found in flange specifications:
- Nominal pipe size (NPS): The flange size corresponds to the pipe to which it is to be attached. NPS is a standard designation that does not necessarily reflect the exact dimensions of the pipe. For example, a garden hose with an NPS of 1/2 inch, may have a slightly larger diameter.
- Flange diameter (OD): The flange's overall diameter is typically larger than the diameter of the pipe to allow space for bolt holes and bolting.
- Bolt circle diameter (BCD): The diameter of an imaginary circle that passes through the center of all the bolt holes in a particular configuration. This helps ensure compatibility and proper alignment between components.
- Flange thickness (T): The thickness of the flange which can vary depending on the pressure class of the flange.
- Number of bolt holes: The number of bolt holes in the flange; this typically increases with the size and pressure rating of the flange.
- Bolt hole diameter: The size of the holes for the bolts. These must be slightly larger than the diameter of the bolts that will pass through them.
- Flange bore (ID): The inner diameter of the flange that matches the inner diameter of the pipe to provide a smooth flow.
- Flange face type: The type of flange face affects the dimensions and includes types such as flat face (FF), raised face (RF), ring-type joint (RTJ), tongue and groove (T&G), and male and female (M&F).
- Pressure rating: Flanges are rated by class, which relates to the maximum pressure the flange can handle. Common classes include 150, 300, 600, 900, 1500, and 2500 for ASME/ANSI B16.5 and B16.47 standards. Read our flange rating article for more information.
The exact dimensions for each flange size and pressure class can be found in the relevant standards. Some of the most commonly used standards are:
- ASME/ANSI B16.5: Covers pipe flanges and flanged fittings for sizes NPS ½” to 24” for above NPS 24” to 60”.
- ASME/ANSI B16.47: Covers large diameter steel flanges for NPS 26” to 60”.
- EN 1092-1: European standard for steel flanges.
- ISO 7005-1: International standard for steel flanges.
Flange fitting sizing chart
A flange fitting size chart is a reference table that provides the standardized dimensions for flange fittings; it helps select the correct flange sizes for piping systems. Remove the pipe from the equipment and use a set of calipers to measure the inner and outer diameters accurately.
- Standardized reference: The chart provides a standardized reference for flange sizes based on the Nominal pipe size (NPS). This allows quick and easy identification of the appropriate flange size for a pipe diameter.
- Dimensional information: The chart lists various dimensions for each NPS, including flange outer diameter (OD), bolt circle diameter (BCD), number of bolt holes, bolt hole diameter, and flange thickness (T). By comparing these dimensions to the actual measurements of your pipe, you can ensure a compatible fit.
The size chart ensures compatibility between flanges, pipes, and other components within a piping system, preventing leaks, system failures, or safety hazards.
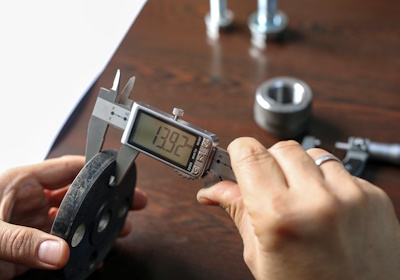
Figure 6: Measuring flange thickness using a caliper
Applications
Flanged fittings are used in various industries.
- Oil and gas: Flanged fittings provide secure and leak-proof joints, essential for maintaining system integrity under high pressure in oil and gas pipelines.
- Chemical processing: Their ability to ensure tight seals makes them ideal for systems that handle corrosive and hazardous chemicals, preventing leaks that could lead to environmental contamination or workplace hazards.
- Power generation: In power plants, flanged fittings facilitate the frequent maintenance and inspection required due to their ease of disassembly while reliably handling high-pressure steam and liquids.
- Water treatment: Flanged fittings are durable and resilient to fluctuating pressures, making them suitable for the complex piping networks of water treatment facilities, ensuring safe water transport and distribution.
- Shipbuilding: The maritime environment demands robust components that can withstand the dynamic stresses on ships; flanged fittings meet this need.
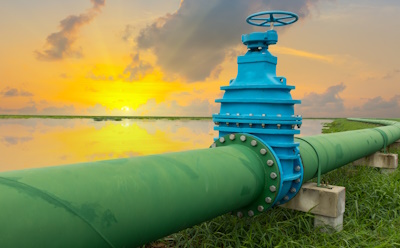
Figure 7: Flanged valve used in a water distribution system
FAQs
What are flange plumbing fittings?
Flange plumbing fittings have a flange that helps bolt together two piping sections and are used to connect sections of pipes, valves, pumps, and other equipment.
What are flange compression fittings?
Flange compression fittings use a compression ring to create a seal between the flange and the pipe.
What materials are typically used for flange hose fittings?
Common materials for flange hose fittings include stainless steel, brass, carbon steel, and aluminum.