Using Pressure Gauges, Switches, and Transducers
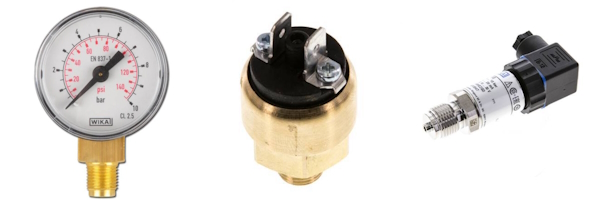
Figure 1: A pressure gauge (left), pressure switch (center), and pressure transducer (right).
Pressure gauges, switches, and transducers help provide accurate pressure monitoring. These devices can be used alone or together, like a pressure gauge with a pressure switch, to improve accuracy, ensure safety, maintain efficiency, and help meet industry standards and rules. This article gives a summary of each type of device and explains how they work together to offer complete pressure monitoring.
Table of contents
- Pressure gauges
- Pressure switches
- Pressure transducers
- Comparing pressure gauges, switches, and transducers
- How they work together
- FAQs
View our online selection of pressure gauges, switches, and transducers!
Pressure gauges
A pressure gauge measures and displays fluid pressure (liquid or gas) within a system. The main function of a pressure gauge is to show the pressure level, letting operators check and ensure the system works within the desired pressure range. Industrial pressure gauges can be analog, featuring a dial and needle, or digital, providing a numerical readout. They are essential for real-time monitoring and are widely used in various industries, including manufacturing, HVAC, and automotive.
Pressure gauges come in various types, each suited for specific applications and requirements. The main types include:
- Analog pressure gauges: These gauges feature a needle that moves across a graduated scale. Analog gauges are simple, reliable, and do not require a power source, making them suitable for many industrial applications.
- Digital pressure gauges: These gauges use electronic sensors to measure pressure and display the reading on a digital screen. They offer higher accuracy and can include additional features such as data logging, alarms, and connectivity to other systems.
- Bourdon tube gauges: These analog gauges use a coiled tube that straightens under pressure. The movement of the tube is transferred to a needle on a dial, providing a pressure reading. They are widely used due to their durability and accuracy.
- Diaphragm gauges: These gauges use a diaphragm that deflects under pressure to move a needle on a dial. They are suitable for measuring low pressures and are often used in corrosive or viscous fluid applications.
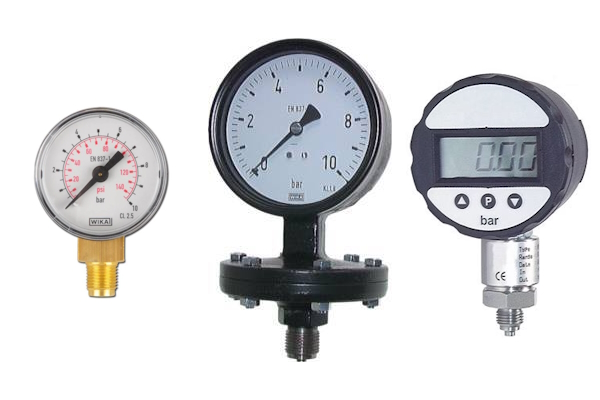
Figure 2: A Bourdon pressure gauge (left), a diaphragm pressure gauge (center), and a digital pressure gauge (right).
Pressure switches
When a predetermined pressure level is reached, a pressure switch activates or deactivates an electrical circuit. The main function of a pressure switch is to provide automatic control and safety in systems by keeping pressure levels within set limits.
Pressure switches come in various types, each designed for specific applications and operating conditions. The main types include:
- Mechanical pressure switches: These switches use mechanical components such as diaphragms, pistons, or Bourdon tubes to detect pressure changes. Mechanical pressure switches are simple, reliable, and do not require a power source.
- Low-pressure switches: These mechanical pressure switches work up to 6 bar (87 psi)
- High-pressure switches: These mechanical pressure switches work up to 50 bar (725 psi)
- Electronic pressure switches: These switches use electronic sensors to detect pressure changes and control the electrical contact. They offer higher precision and can include features such as adjustable set points, digital displays, and remote monitoring capabilities.
- Vacuum pressure switches: These switches work like other pressure switches but are made to respond to negative pressure (vacuum) conditions.
- Air compressor pressure switches: These switches check the pressure in an air compressor's tank and control the motor to keep the desired pressure range. The switch turns on the compressor when the pressure drops below a set point. When the pressure goes above the upper limit, it turns off the compressor.
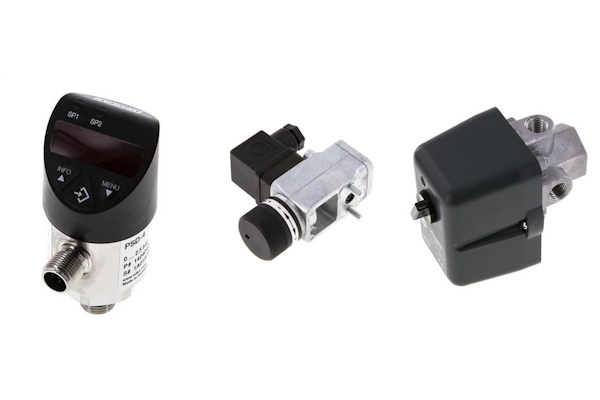
Figure 3: A digital pressure switch (left), a vacuum pressure switch (center), and an air compressor pressure switch (right).
Pressure transducers
A pressure transducer converts pressure into an electrical signal. It provides precise and continuous pressure measurements that control, data acquisition, and monitoring equipment can use. Pressure transducers usually have a pressure-sensitive part, like a diaphragm or piezoelectric crystal, and an electrical part that changes the mechanical movement of the pressure-sensitive part into an electrical signal. The output signal is usually a voltage, current, or digital signal corresponding to the measured pressure.
Pressure transducers come in various types, each utilizing different sensing technologies to measure pressure. One common pressure transducer type to highlight is the strain gauge pressure transducer. These transducers use a strain gauge bonded to a diaphragm.
When pressure is applied, the diaphragm deforms, causing a change in the electrical resistance of the strain gauge. This change is converted into an electrical signal proportional to the pressure. Strain gauge transducers are known for their accuracy and stability.
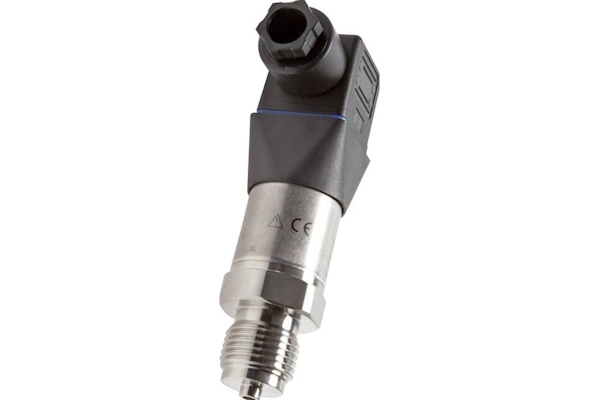
Figure 4: A strain gauge pressure transducer.
Comparing pressure gauges, switches, and transducers
Pressure gauges, switches, and transducers each serve distinct functions and are used in different applications. A comparison of several aspects concerning the three devices is provided in Table 1.
Table 1: A comprehensive comparison between pressure gauges, switches, and transducers
Aspect | Pressure gauges | Pressure switches | Pressure transducers |
---|---|---|---|
Functionality | Visual pressure measurement | Automatic control based on pressure levels | Converts pressure into electrical signals |
Measurement type | Real-time, visual | Threshold-based activation/deactivation | Continuous, precise |
Output | Dial or digital readout | Electrical contact (open/close) | Voltage, current, or digital signal |
Power requirement | None (analog); battery or external (digital) | None (mechanical); external power (electronic) | External power required |
Accuracy | Moderate (analog); higher (digital) | Moderate (mechanical); higher (electronic) | High |
Integration | Standalone | Standalone or basic integration | Seamless integration with control systems |
Applications | Real-time monitoring | Safety systems, automation, process control | Industrial automation, aerospace, medical, etc. |
Cost | Low (analog); moderate (digital) | Moderate (mechanical); higher (electronic) | Higher |
Advantages | Simple, cost-effective, no power needed | Automatic control, safety, reliability | High accuracy, continuous monitoring, integration |
Disadvantages | Limited to visual monitoring | Limited precision | Higher cost, requires power and complex setup |
Selection criteria | Basic monitoring needs, budget constraints | Need for automatic control and safety | High accuracy, integration with digital systems |
How they work together
Integrating pressure gauges, switches, and transducers can significantly enhance the accuracy, safety, and efficiency of pressure monitoring systems. Take advantage of the strengths of each device to achieve a comprehensive and robust monitoring solution. Here are some practical ways these devices can be combined:
Pressure gauge with pressure switch
Combining a pressure gauge with a pressure switch allows for both real-time visual monitoring and automatic control. For example, in an HVAC system, a pressure gauge can monitor the pressure of refrigerant lines, while a pressure switch can automatically shut down the system if the pressure goes above safe limits, preventing damage to the compressor.
Pressure gauge with pressure transducer
Integrating a pressure gauge with a pressure transducer offers the benefits of real-time visual monitoring and precise, continuous electronic measurement. For example, in a water treatment plant, a pressure gauge can monitor the pressure in filtration systems, while a pressure transducer sends continuous pressure data to a central control system for real-time monitoring and automatic adjustments to keep optimal filtration conditions.
Pressure switch with pressure transducer
Combining a pressure switch with a pressure transducer enhances automatic control and precise monitoring capabilities. For example, in an industrial air compressor system, a pressure switch can control the compressor motor to keep the desired pressure range, while a pressure transducer provides continuous pressure data to a supervisory control and data acquisition (SCADA) system for monitoring and optimization.
Comprehensive integration: pressure gauge, switch, and transducer
Using all three devices—pressure gauge, pressure switch, and pressure transducer—offers a multi-layered approach to pressure management for the best pressure monitoring solution. For example, in a chemical processing plant, a pressure gauge can be used to monitor the pressure in reaction vessels, a pressure switch can automatically shut down the process if the pressure exceeds safe limits, and a pressure transducer can provide continuous pressure data to the plant's distributed control system (DCS) for real-time monitoring and process optimization.
Benefits of combined pressure monitoring systems
- Increased accuracy: Combining devices ensures that pressure measurements are accurate and reliable, reducing the risk of errors.
- Enhanced safety: Automatic control mechanisms provided by pressure switches help prevent dangerous overpressure or underpressure conditions.
- Improved efficiency: Continuous monitoring and precise control enable optimal system performance and reduce downtime.
- Regulatory compliance: Comprehensive monitoring helps meet industry standards and regulatory requirements.
- Data integration: Pressure transducers facilitate the integration of pressure data into digital control and monitoring systems, enabling advanced data analysis and process optimization.
FAQs
What is a pressure gauge with a pressure switch?
A pressure gauge with a pressure switch combines visual pressure readings with an automatic switch to control systems based on pressure levels.
What is the difference between a pressure gauge and a pressure transducer?
A pressure gauge provides a visual display of pressure, while a pressure transducer converts pressure into an electrical signal for monitoring and control.
What is the difference between a pressure switch and a pressure transducer?
A pressure switch activates or deactivates a circuit at a set pressure, while a pressure transducer converts pressure into an electrical signal for continuous monitoring.
What are the benefits of using a pressure transducer vs a pressure gauge?
A pressure transducer offers real-time data and integration with digital systems, whereas a pressure gauge provides a simple, visual indication of pressure.