Comparing Solenoid Valves with Other Valve Types: Advantages and Disadvantages
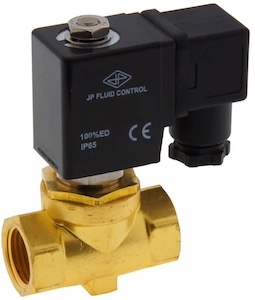
Figure 1: A 2-way brass solenoid valve
Solenoid valves are highly regarded for their rapid response, dependable performance, and user-friendly integration into automated systems. However, they are just one option among a variety of control valves and may not be suitable for every application. This article provides a comparative analysis of solenoid valves alongside five other types of shutoff valves, highlighting the unique advantages and potential drawbacks of each.
View our online selection of solenoid valves!
Advantages and disadvantages table
Table 1 offers a very brief comparison of solenoid valves to other control valve types. The other valves discussed in this article are gate valves, butterfly valves, ball valves, needle valves, and angle seat valves. Each piece of information in Table 1 is in comparison to solenoid valves. For example, the table describes the response time of gate valves as slower. This means that gate valves have a slower response time than solenoid valves.
Valve type | Response time | Flow control | Flow capacity | Pressure rating | Temperature rating | Cost |
Gate valve | Slower | on/off | Higher | Higher | Higher | Lower |
Needle valve | Slower | on/off and proportional | Lower | Higher | Higher | Similar |
Butterfly valve | Slower | on/off and proportional | Higher | Similar | Higher | Similar |
Ball valve | Slower | on/off | Higher | Higher | Higher | Lower |
Angle seat valve | Slower | on/off | Higher | Higher | Higher | Lower |
Table 1: Brief overview of various valve types compared to solenoid valves. Response time "slower" for gate valves means that a gate valve has a slower response time than a solenoid valve.
Solenoid valves vs other control valves
Compared with other control valves, solenoid valves have several advantages and disadvantages. This section takes a closer look at these factors by giving further information on the brief overview in Table 1.
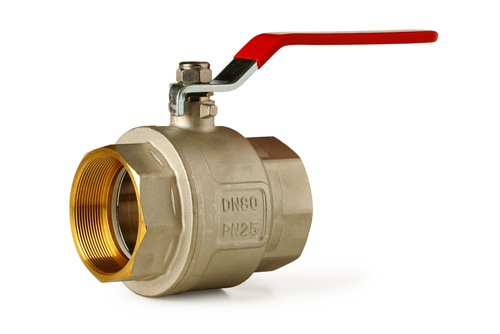
Figure 2: A brass ball valve
Response time
One of the most significant advantages of solenoid valves over other valve types is their response time, which is nearly instantaneous in the low milliseconds. This response time is necessary for applications such as fuel injection in automotive systems, regulating pressure in a hydraulic system, and controlling airflow in an HVAC system.
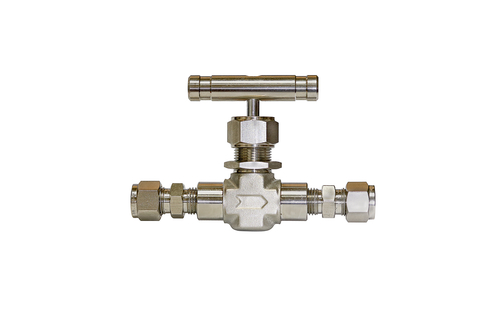
Figure 3: A stainless steel needle valve
Flow control
All of the valves this article discusses are, in their basic form, on/off control valves. Solenoid valves, above all others, are valued for their near instantaneous switching between fully open and fully closed states. Beyond on/off control, though, proportional solenoid valves can modulate flow.
Needle valves and butterfly valves also allow for precise flow control between the on/off states. A standard ball valve does not allow for this, but a v-port ball valve does. Angle seat valves and gate valves do not offer precise flow control.
Flow capacity
Besides needle valves, all valve types in this article have higher flow rates than solenoid valves. While indirect solenoid valves can handle higher flow capacities than semi-direct and direct-acting solenoid valves, they still have much lower flow capacities than control valve types. For example, a 2.5-inch indirect solenoid valve may have a Kv value of 40 cubic meters per hour. In contrast, a 2.5-inch ball valve has a Kv value of 320 cubic meters per hour. To learn more about how to measure flow rate, read our Kv calculator article. For imperial units, read our Cv calculator article.
Power source
Solenoid valves are always electrically controlled and therefore require electricity to operate. The other valves discussed in this article, however, are manually controlled. That being said, each valve can be controlled by electric, pneumatic, or hydraulic actuators to overcome the limitations of manual control.
Media purity
There should not be any contaminants or particles in the media flowing through a solenoid valve. These can easily clog the valve, causing it to stay in the open position, and damage the internal components. Needle valves and angle seat valves similarly work best with clean media. Butterfly, ball, and gate valves, though, can operate better with contaminated media, making them ideal for situations such as wastewater applications. Ultimately, though, valves do work best with media that does not contain contaminants or particles.
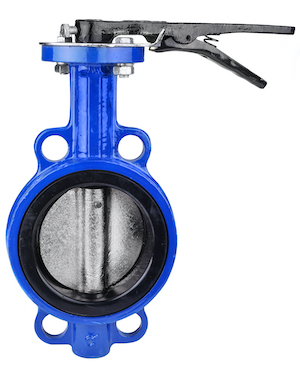
Figure 4: A cast iron butterfly valve
Pressure rating
A significant disadvantage of solenoid valves is that they cannot handle as high pressure as other control valves. Among the valves discussed in this article, only butterfly valves have a max operating pressure limitation similar to solenoid valves. Angle seat valves are slightly higher, and needle valves, ball valves, and gate valves have max operating pressures significantly higher. Therefore, the latter three valves are often employed in high-pressure industrial processes.
Temperature rating
Solenoid valves also have a relatively low max operating temperature. This is due to the electrical components in the valve that can easily be damaged at temperatures above 120 °C (250 °F). The other valves discussed in this article do not have electrical components in their standard designs but can be actuated by electric actuators. Using an electric actuator can reduce a valve's suitability for high-temperature applications.
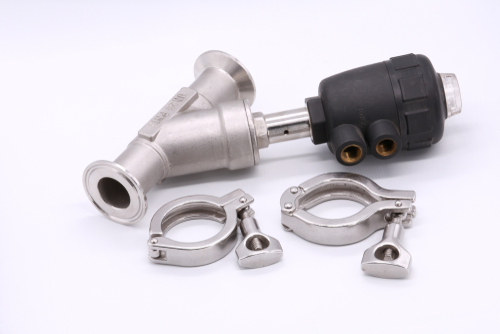
Figure 5: An angle seat valve
Applications
Using the right valve for a particular application is essential, maximizing the application's efficiency and the valve's lifetime. It's not simple to choose just the right valve for every application since some applications can use multiple types. Always study the application's parameters (e.g., max operating pressure, temperature, and environment) to determine whether or not a particular valve meets the needs.
This section offers some typical applications for the valves discussed in this article. This list is incomplete, but it can give some insight into typical uses.
-
Solenoid valves
- Irrigation systems for gardens, parks, etc.
- Fluid flow control in oil and gas industries
- Compressed air and HVAC systems
-
Ball valves
- Isolating fluid flow in plumbing systems
- High-pressure applications such as natural gas pipelines
- Fluid flow control in chemical plants
-
Gate valves
- Water supply or wastewater treatment systems
- Large-scale industrial processes, like power plants and refineries
- Isolating flow in pipelines and storage tanks
-
Butterfly valves
- Flow control in cooling systems and food and beverage processing plants
- Airflow control in HVAC systems
- Fire protection system emergency shutoff
-
Needle valves
- Precise control of fluid or gas in laboratory equipment
- Fine adjustment of flow in fuel injection systems
- High-pressure fluid flow regulation in hydraulic systems
-
Angle seat valves
- Steam and thermal fluid systems
- Fluid flow control in high-viscosity applications
- Compressed air systems' pressure regulation
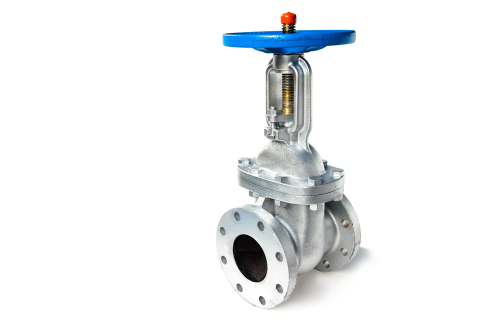
Figure 6: A gate valve
FAQ
When should I choose a solenoid valve over other valve types for my application?
Choose a solenoid valve for low-pressure applications that require remote actuation, fast response, and rapid opening and closing of the valve.