Steam Check Valve Overview
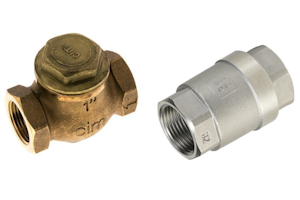
Figure 1: Red brass (left) and stainless steel (right) are two excellent options for steam check valves.
Steam check valves prevent the backflow of steam and ensure efficient, safe operation across various industries. By allowing steam to flow in only one direction, these valves protect equipment from damage and maintain process integrity, optimizing performance in power generation, manufacturing, and food processing. Understanding how check valves function, their applications, and the critical parameters for their selection and installation is vital for maximizing their benefits. This article delves into the workings of steam check valves, their diverse applications, and the key considerations for selecting and installing the correct valve to meet specific system requirements.
Table of contents
View our online selection of check valves!
How check valves work
Check valves permit fluid to flow in one direction and block reverse flow. They consist of a valve body and an internal mechanism, such as a disc, ball, or flap, that responds to fluid flow. In the desired flow direction, pressure opens the mechanism, allowing fluid passage. If flow reverses, pressure changes close the mechanism against a seat, preventing reverse flow. This automatic operation relies solely on the pressure differential across the valve, requiring no external control. Learn more in our check valve overview article.
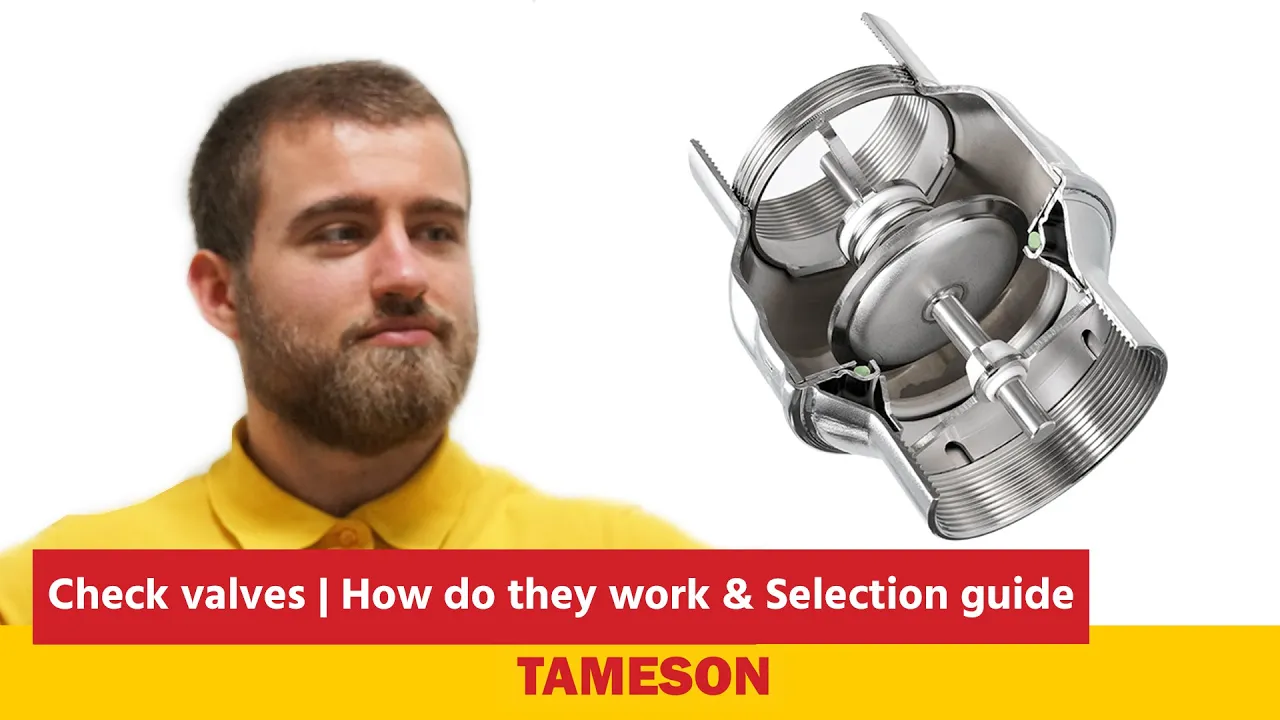
Applications
Here are some typical steam applications where steam rated check valves are used:
- Power generation: In power plants, check valves maintain unidirectional steam flow through turbines. They are also necessary in boiler feedwater systems to prevent steam backflow into the feedwater supply.
- Manufacturing: Steam is used for heating, sterilization, and cleaning. Check valves ensure steam flows in the intended direction.
- Food processing: Check valves for steam lines used for cooking, blanching, and sterilization maintain hygiene and prevent contamination.
- HVAC systems: In HVAC systems, check valves regulate steam flow to heating coils and radiators, preventing reverse flow and ensuring consistent heating and energy efficiency.
- Steam boiler: Check valves for steam boilers maintain the correct flow of steam and prevent backflow, which can cause pressure imbalances and potential damage to the system.
Application parameters
The maximum operating pressure for a steam application can vary widely depending on the equipment and specific application. Here are some general guidelines:
- Low-pressure steam systems: Typically operate at pressures below 1 bar (15 psi) and temperatures up to around 120 °C (248 °F). These systems are often used for heating and certain industrial processes.
- Medium-pressure steam systems: Operate at pressures between 1 bar and 10 bar (15 psi to 150 psi) with temperatures typically up to 180 °C (356 °F). These are common in industrial applications.
- High-pressure steam systems: Operate at pressures above 10 bar (150 psi), and temperatures can reach up to 250 °C (482 °F). High-pressure steam is used in power generation and other heavy industrial applications.
- Supercritical steam systems: These operate at pressures above 220 bar (3,200 psi) and temperatures above 374 °C (705 °F). Supercritical steam is used in advanced power generation applications.
The actual maximum operating pressure and temperature will depend on the design specifications of the system and the materials used in construction. Always refer to the manufacturer's specifications and industry standards for the specific equipment and application.
Materials
Material considerations are crucial to ensure durability, performance, and safety. The materials used in the construction of steam check valves must withstand the high temperatures and pressures typical in steam applications.
Stainless steel
- Check valve type: Spring check valve
- Maximum operating pressure: 63 bar (914 psi)
- Minimum opening pressure (bar then psi): 0.022, 0.028, 0.03, 0.037, 0.048, 0.055, 0.06, 0.065, 0.085 (0.319, 0.406, 0.435, 0.537, 0.696, 0.798, 0.870, 0.943, 1.233)
- Maximum operating temperature: 200 °C (392 °F)
- Minimum operating temperature: -20 °C (-4 °F)
- Seal material: Teflon (PTFE)
Red brass (gunmetal)
- Check valve type: Lift check valve
- Maximum operating pressure: 16 bar (232 psi) or 20 bar (290 psi)
- Minimum opening pressure: 0.02 bar (0.29 psi)
- Maximum operating temperature: 100 °C (212 °F)
- Minimum operating temperature: -10 °C (14 °F)
- Seal material: Teflon (PTFE)
Spring and lift check valve comparison
Table 1: Comparison of Different Check Valves
Feature/Criteria | Lift check valves | Spring-loaded check valves |
---|---|---|
Operation | Disc lifted by fluid flow, closes by gravity or back pressure | Spring mechanism compresses to open, expands to close |
Advantages | Good sealing for high-pressure applications |
|
Limitations |
|
|
Ideal applications | Clean fluid systems with consistent flow | Systems requiring quick response and versatile installation |
Installation flexibility | Limited (horizontal only) | High (any orientation) |
Cost | Moderate | Higher |
Maintenance | Low to moderate, depending on debris exposure | Moderate to high, due to potential spring wear |
Selection criteria
Selecting the right check valve for steam systems is a critical decision that impacts the system's efficiency, safety, and longevity. Several factors must be considered to ensure the chosen valve meets the application's specific needs.
When selecting a check valve for steam systems, ensuring compatibility with system specifications is paramount. This involves several key considerations:
- Connection size and type: The valve must match the pipe size to prevent excessive pressure drop or flow restriction. Steam check valves are generally threaded (BSP).
- Flow rate: The valve should accommodate the system's flow rate without causing significant pressure loss.
- Kv or Cv: With the flow rate and pressure differential across the valve, the Kv and Cv values can be calculated to ensure the selected valve fits the system.
- Avoid oversizing and undersizing: Oversized valves may not fully open, leading to valve chatter and potential damage. Undersized valves can restrict flow and increase pressure drop, reducing system efficiency.
- Pressure and temperature ratings: The valve should be rated to handle the maximum pressure and temperature of the steam system to ensure safe and reliable operation. (See material section above)
- Material compatibility: The materials used in the valve must be compatible with the steam and any other substances in the system to prevent corrosion or degradation. (See material section above)
- Certifications: Check for application-specific certifications like drinking water, WRAS, NSF ANSI 61, etc.
Installation
When installing check valves in steam systems, following best practices is essential to ensure optimal performance and safety. The following list is a good start for best practices. Read our check valve installation article to learn more.
- Correct orientation: Ensure the check valve is installed in the correct orientation, as specified by the manufacturer. Some valves are designed for horizontal installation, while others can be installed vertically.
- Proper alignment: Align the valve with the pipeline to prevent stress on the valve body and ensure smooth operation. Misalignment can lead to leaks and premature wear.
- Support and anchoring: Provide adequate support and anchoring for the valve and adjacent piping to minimize vibration and movement, which can cause damage over time.
- Clearance and accessibility: Install the valve with sufficient clearance for maintenance and inspection. Ensure that it is easily accessible for future servicing needs.
- System flushing: Before installation, flush the system to remove debris that could damage the valve or impede its operation.
FAQs
What is a steam check valve?
A steam check valve prevents backflow in steam systems, ensuring steam flows in one direction to protect equipment and maintain process integrity.
How does a check valve for steam boilers work?
A check valve for steam boilers allows steam to flow in one direction, preventing reverse flow that could damage the boiler or connected equipment.
Why are steam rated check valves important?
Steam rated check valves are crucial for ensuring safe, efficient steam flow, protecting systems from backflow and potential damage.
Where are steam boiler check valves used?
Steam boiler check valves are used in power generation, manufacturing, and food processing to maintain safe, efficient steam flow.